Расчет режимов резания — РИНКОМ
Расчет режимов резания — РИНКОМСкрыть уведомление
Внимание! Все заказы, сделанные в предстоящие праздники с 6.05 по 9.05, будут обработаны в первый же рабочий день (10 мая)!
Главная
Статьи
Расчет режимов резания Расчет режимов резания
23 декабря 2021
Гирин Кирилл
Расчет режимов резания осуществляется при механизированной и ручной обработке металла. По результатам вычислений подбирается оснастка, определяется оптимальный способ проведения работ и размер производственных расходов.
В материале:
- Способы проведения расчетов
- Параметры, учитываемые при проведении расчетов
- Обработка резцами
- Сверление
- Зенкерование
- Работа с развертками
- Фрезерование
- Шлифование
- Заключение
Ключевые задачи процедуры:
- повышение скорости и качества операций;
- снижение материалоемкости производства;
- уменьшение нагрузки на персонал;
- снижение процента брака;
- внедрение ресурсосберегающих технологий;
- повышение рентабельности.
Подбор режимов резания происходит для каждой технологической операции. Работы проводятся комплексно, предполагают использование справочников режимов резания, отраслевых нормативов и прочей документации.
Способы проведения расчетов
Режимы резания металлов рассчитываются одним из двух способов.
- Аналитический. Вычисления производятся эмпирически. Специалисты выполняют тестовые операции на основе формул теории резания. В результате подбираются оптимальные режимы обработки для конкретного материала или заготовки.
- Статистический. Способ обработки подбирается по справочнику режимов резания. Такой подход не предполагает проведения экспериментов, ориентирован на работу с общими отраслевыми нормативами.
Применяемый инструмент должен иметь рациональную конструкцию, обеспечивать максимальное использование всех возможностей оборудования.
Параметры, учитываемые при проведении расчетов
При расчете режимов резания инструментов используются следующие показатели.
- Глубина реза. Расстояние, на которое погружается инструмент в процессе обработки заготовки.
- Подача. Степень перемещения инструмента в рамках одного рабочего такта.
- Скорость режима резания. Отношение скорости перемещения режущей кромки ко времени, затрачиваемому на обработку детали.
- Расчетные размеры. Параметры заготовки. К ним относится диаметр, длина и ширина обрабатываемой поверхности.
В ходе подбора режимов резания металлов учитываются припуски на обработку, затрачиваемое время и количество проходов.
Обработка резцами
При назначении режимов резцового резания определяется порядок обработки материала, учитывается специфика воздействия инструмента на заготовку.
Рис. 1 Обработка металла резцом (принципиальная схема)
На рисунке 1 представлены показатели, влияющие на токарный режим резания:
- t – глубина реза;
- s – подача;
- f – площадь номинально срезанного слоя;
- Н – высота остаточного сечения;
- ϕ − главный угол;
- ϕ1− вспомогательный угол.
Подбор режимов подачи осуществляется по специальным таблицам.
Таблица 1. Расчет подачи для незакаленных сталей и чугунов
Таблица 2. Расчет подачи для закаленных сталейОзнакомиться с ассортиментом токарных резцов, используемых при расчете режима резания металлов, поможет представленная ссылка.
Рис. 2 Работа резца по металлу
Сверление
Режимы работы со сверлами определяются с учетом конфигурации инструмента, параметров заготовок и специфики применяемого оборудования. Как правило, используются формулы и табличные значения. Они позволяют подобрать режим резания для сверл с высокой точностью.
Для расчета подачи сверла применяется формула s = C х D0,6, в которой:
- s – подача;
- D – диаметр применяемого сверла;
- С – нормативный коэффициент.
Значения коэффициента представлены в таблице.
Таблица 3. Значения коэффициента С для сверл
Сила, подача и момент резания рассчитываются по типовым формулам с применением соответствующих коэффициентов.
Таблица 4. Коэффициенты, позволяющие рассчитать режимы резания для сверл
Корректное использование таблиц и формул расчета резания позволит подобрать оптимальный режим. Он обеспечит высокую эффективность инструмента и минимальные затраты на последующую обработку детали.
Для ознакомления со сверлами, участвующими в различных режимах резания стали, посетите раздел сверла по металлу.
Рис. 3 Работа сверла по металлу
Зенкерование
Геометрия режущей части зенкеров не нормирована. Производители применяют различные технологические решения, с целью повысить эффективность и продлить срок службы продукции.
При определении режима резания стали зенкером специалисты учитывают следующие параметры:
- задний и передний угол зенкера;
- угол наклона винтовой канавки;
- угол при навершии;
- угол при наклоне режущей кромки.
Как и в случае с прочим режущим инструментом, расчетные процедуры выполняются по базовым формулам и рекомендациям нормативов по режимам резания.
Рис. 4 Работа зенкера по металлу
Ознакомиться с инструментами, для которых рассчитываются технологические режимы резания, поможет раздел «Зенкеры и зенковки». В нем представлен широкий спектр продуктов, присутствуют решения для различных вариантов обработки.
Работа с развертками
Развертки используются для предварительной и окончательной обработки заготовок. Они позволяют создать отверстия требуемого качества и формы. Инструмент востребован на производстве и в быту.
Расчет параметров режимов резания осуществляется с учетом следующих показателей разверток:
- угол наклона канавок;
- задний угол;
- передний угол;
- угол конуса заборной части.
При работе с пластинами из твердого сплава подача определяется по таблице.
Таблица 5. Подача разверток с пластинками из твердого сплава
Определить стойкость изделий также помогают нормативные значения.
Таблица 6. Стойкость разверток в минутах
Полный перечень разверток, используемых при организации технологических операций, представлен в соответствующем разделе. Специалистам доступен инструмент для ручного и механизированного труда. В ассортименте решения, работающие с чугуном, цветными металлами, конструкционными и легированными сталями.
Рис. 5 Работа развертки
Фрезерование
При расчете общемашинных режимов резания посредством фрез учитываются геометрические параметры режущей части инструмента:
- задний и передний угол;
- угол наклона винтовой канавки зубцов;
- главный и вспомогательный угол в плане угловой кромки;
- дополнительный угол в плане, в случае двойной заточки кромок;
- угол наклона режущей кромки.
Получить дополнительные сведения о характеристиках фрезерного инструмента можно посредством справочников и производственных документов. Последние предоставляется заводом-изготовителем по запросу покупателя.
Рассчитать подачу фрез при работе со сталями, стальным литьем и чугунами поможет следующая таблица.
Таблица 7. Расчет подачи фрез при работе с различными материалами
Показатели стойкости фрез также представлены справочными значениями.
Таблица 8. Стойкость фрез в минутах
В случае скоростного фрезерования на механизированном оборудовании применяются дополнительные значения и коэффициенты.
Таблица 9. Средние значения скорости резания при работе с чугунами, углеродистыми и легированными сталями
При определении параметров режима резания учитывается расчетная мощность, сила и момент резания, а также основное технологическое время.
Получить дополнительную информацию касательно работы с фрезерным инструментом поможет статья «Фрезерование концевыми фрезами». Для знакомства с перечнем фрез по металлу перейдите в соответствующий раздел каталога.
Рис. 6 Работа фрезы по металлу
Шлифование
Посредством шлифовального инструмента осуществляется первичная, вторичная и финишная обработка заготовок. При наличии соответствующей оснастки мастеру доступен широкий спектр работ:
- шлифование центральной части заготовки;
- внутреннее и наружное шлифование бесцентрового типа;
- внутреннее шлифование с использованием патрона;
- плоское шлифование периферией или торцом инструмента;
- фасонное шлифование.
Возможна заточка режущего инструмента различной конфигурации.
При проведении расчетов учитывается скорость вращения шлифовальных кругов.
Таблица 10. Скорость вращение шлифовального инструмента в процессе обработки заготовки
Продолжительность эксплуатации кругов при выполнении различных процедур также имеет нормированное значение.
Таблица 11. Стойкость шлифовальных кругов
Режимы резания зависят от параметров шлифования и специфики применяемого оборудования.
Таблица 12. Подбор режимов резания при работе с абразивным инструментом
В случае работы с резьбовыми соединениями применяются особые режимы резания.
Таблица 13. Режимы резания при работах по шлифованию резьбы
При шлифовании выделяется большое количество тепла. Для его рассеивания применяются охлаждающие жидкости. Допускается использование водных растворов 5 типов:
- 1% кальцинированной соды и 0,15 нитрита натрия;
- 2-3% кальцинированной соды;
- 2% мыльного порошка;
- 5-7% раствор эмульсола;
- 3,5% раствор эмульсола с добавлением олеиновой кислоты.
Качественное охлаждение исключит температурную деформацию заготовки, предотвратит преждевременный износ инструмента и нарушение технологии обработки.
Рис. 7 Работа абразивного круга
Для получения подробной информации касательно абразивного инструмента посетите соответствующий раздел каталога. В нем представлены круги, шлифовальные шкурки на тканевой и бумажной основе, сетки и приспособления для шлифования.
Заключение
Расчет режимов резания – обязательное условие для большинства технологических операций. Однако, для корректного выполнения работ недостаточно вычислений. Важно использовать качественный инструмент, способный выполнить необходимые действия. Последний можно приобрести у нас. Магазин «РИНКОМ» реализует широкий спектр продукции для работы с деревом и металлом. Мы гарантируем высокое качество товара, приемлемые цены и строгое соблюдение сроков поставки.
Больше полезной информации
Полезные обзоры и статьи
Все статьи
21 апреля 2023
Виды концевых фрез
4 апреля 2023
Фрезерование концевыми фрезами
27 марта 2023
Режущий инструмент по металлу
23 января 2023
Фрезы со сменными пластинами
Все статьи
Подписывайтесь на нас
Присылаем скидки на инструмент и только полезную информацию!
Не нашли нужной позиции в каталоге?
Мы готовы изготовить и поставить уникальные виды инструмента специально под ваш заказ!
Заказать
Каталог
Корзина СравнитьВход
Мы используем файлы cookie. Они помогают улучшить ваше взаимодействие с сайтом.
Принимаю
?>
Расчет и табличное определение режимов резания при фрезеровании | Методическая разработка на тему:
Расчёт и табличное определение режимов резания при фрезеровании
Дано: Материал заготовки – Серый чугун, 210 НВ
Вид обработки – черновое торцовое фрезерование плоскости шириной В=80 мм, длиной l = 120 мм.
Припуск на обработку h = 2мм.
Заготовка – отливка.
Обработка без охлаждения.
Станок вертикально-фрезерный 6Т12
Необходимо: выбрать режущий инструмент; назначить режим резания; определить основное время.
Решение
1 Выбираем фрезу и устанавливаем её геометрические параметры (см. Приложение 1). Для торцового фрезерования диаметр фрезы определяется по формуле
Dф = 1,6 · В (1)
где В – ширина фрезерования, мм.
Dф = 1,6 · 80 = 128 мм
Принимаем стандартное значение диаметра торцовой насадной фрезы со вставными ножами, оснащенными пластинами из твердого сплава ВК6 по ГОСТ 9473-80 Dф = 125 мм [1, с.187].
Число зубьев фрезы, оснащенной твердым сплавом, определяется по формуле
z = (0,08÷0,1)·D, (2)
где обозначения прежние
z = (0,08÷0,1)·125 = 10 шт.
Определим геометрические параметры торцовой фрезы: ω=35 °; φ1 = 1; φ=30 °; α1 = 8 °; αn = 12 °; γ = 10 ° [4, с.390].* 1
2 Назначаем режим резания
Глубина резания определяется по заданию t=h=2мм
Назначаем стойкость инструмента и его допустимый износ: Т = 180 мин [1, с.290], hз = 2 мм [5, с.50]* 2
Назначаем подачу, мм/зуб* 3
Sz = 0,2 – 0,4 мм/зуб.
Принимаем Sz = 0,3 мм/зуб [1, с.283].
Определяем скорость резания, допускаемую режущими свойствами фрезы, аналитическим методом по формуле
, (3)
где Сv , q, m, x, y, u, p – коэффициент и показатели степени,
Сv = 445, q = 0,2, m = 0,32, x = 0,15, y =0,35, u = 0,2, p = 0 [1, с. 286]
Dф – диаметр фрезы, мм;
Т – стойкость инструмента, мин;
t – глубина резания, мм;
Sz –подача на зуб, мм/зуб;
В – ширина фрезерования, мм;
z – число зубьев фрезы;
Кv – поправочный коэффициент на скорость резания
(4)
где Км – коэффициент, зависящий от обрабатываемого материала;
____________________________________________________________________________________
* 1 Дополнительные источники: [2, с.248] [4, с.369] [4, с.676, 790, 945] [6, с.366]
* 2 Дополнительные источники: [2, с.444] [4, с.400] [6, с.203]
* 3 Если в справочной литературе дана подача на оборот Sо, мм/об, необходимо найти подачу на зуб по формуле Sz = So/z, где z – число зубье
[1, с.262] (5)
где НВ – фактические параметры обрабатываемого материала;
n – показатель степени,
n = 0,95 [1, с. 262];
Кп – коэффициент, учитывающий влияние состояния поверхности заготовки,
Кп = 0,8 [1, с.263];
Ки – коэффициент, учитывающий влияние инструментального материала,
Ки = 1 [1, с.263];
м/мин
Определим скорость резания табличным методом
v = vТ · Kv , (6)
где vТ – табличное значение скорости резания,
vТ = 126 м/мин [9, с.307]
Кv – поправочный коэффициент на скорость резания
Kv = Kм· Kи· Kn· Кс· Кф· Kо · Kв · Kφ, (7)
где Kм – коэффициент, учитывающий марку обрабатываемого материала
Kм = 0,89 [9, с.20];
Kи – коэффициент, учитывающий материал инструмента
Kи = 1,0 [9, с.308];
Kn – коэффициент, учитывающий состояние обрабатываемой поверхности
Kn = 0,8 [9, с. 308];
Кс – коэффициент, учитывающий шифр типовой схемы фрезерования
Кс = –
Кф – коэффициент, учитывающий форму обрабатываемой поверхности
Кф = –
Kо – коэффициент, учитывающий условия обработки
Kо = 1,0 [9, с.308];
Kв – коэффициент, учитывающий отношение фактической ширины фрезерования к нормативной
Kв = 1,0 [9, с.309];
K φ – коэффициент, учитывающий влияние главного угла в плане
K φ = 1,3 [9, с.308].
Подставляя значения в формулу 7 и 6, получим
Кv = 0,89 · 1 · 0,8 · 1 · 1 · 1,3 = 0,92
v = 126 · 0,92 = 116,6 м/мин
Определим частоту вращения шпинделя по формуле
(8)
где Vрез – аналитическая скорость резания;
остальные обозначения прежние
об/мин
Корректируем частоту вращения по паспорту станка
nд = 315 об/мин [7, с. 422]
Определим действительную скорость резания, м/мин, по формуле
(9)
где обозначения прежние
м/мин
Находим минутную подачу, м/мин, по формуле
SM = Sz · z ·nд (10)
где Sz – подача на зуб, мм/зуб;
z – число зубьев фрезы, шт;
nд – действительная частота вращения шпинделя, об/мин
SM = 0,3 · 10 · 315 = 945 м/мин
Корректируем подачу по паспорту станка. Принимаем SMд = 1000 м/мин [7, с.422]
Из формулы 10 найдем подачу на зуб
Sz = мм/зуб
Определяем силу резания, Н, по формуле
, (11)
где Сp , x, y, u, q, w – коэффициент и показатели степени,
Ср = 54,5; x = 0,9, y =0,74, u = 1,0, q = 1, w = 0 [1, с. 291]
Dф – диаметр фрезы, мм;
t – глубина резания, мм;
Sz –подача на зуб, мм/зуб;
В – ширина фрезерования, мм;
z – число зубьев фрезы;
n – действительная частота вращения шпинделя, об/мин;
Кмр – поправочный коэффициент на силу резания, учитывающий обрабатываемый материал
[1, с.264] (12)
где НВ – фактические параметры обрабатываемого материала;
n – показатель степени,
n = 1,0 [1, с.264];
Н
Сравниваем силу резания с допустимой силой механизма станка
Pz
где Pzдоп = 15000 Н [7, с.422];
2639
следовательно, выбранная подача допустима
Определяем крутящий момент, Н·м
(14)
где обозначения прежние
Н·м
Находим мощность, затрачиваемую на резание, по формуле
, (15)
где Рz – сила резания, Н;
vд – действительная скорость резания, м/мин
Сравниваем мощность резания с мощностью привода станка
Nрез ≤ Nшп , (16)
где Nшп – мощность шпинделя станка
Nшп = Nэ. дв · η, (17)
где Nэ.дв – мощность электродвигателя станка, кВт
Nэ.дв = 7,5 кВт [7, с.422];
η – КПД станка
η = 0,8 [7, с.422]
Nшп = 7,5 · 0,8 = 6 кВт
Так как 5,4
3 Определяем основное время, мин, по формуле
, (18)
где L – длина пути инструмента или детали в направлении подачи, мм, определяется по формуле
L = l + l1 + l2 , (19)
где l – длина обрабатываемой поверхности, мм;
l1 – длина врезания, мм
l1 = 19 мм [3, с.84];
l2 – длина перебега фрезы, мм
l2 = 1 ÷ 6 мм [3, с.84]. Принимаем l2 = 5 мм
L = 120 + 19 + 5 = 144 мм
SМ – минутная подача, м/мин;
i – число проходов
i = h|t (20)
где h – припуск на обработку, мм;
t – глубина резания, мм.
Так как h = t, то i = 1
По формуле 18
мм
Рисунок 1 – Схема фрезерования плоскости торцовой фрезой
Перечень использованной литературы
1 Косилова А.Г., Мещеряков Р.К. Справочник технолога – машиностроителя, Т2. М.: Машиностроение, 1986. 496 с.
2 Малов А.Н. Справочник технолога – машиностроителя, Т2 М.: Машиностроение, 1973 г.
3 Антонюк В.Е. и др. Краткий справочник технолога механического цеха. Минск: Беларусь, 1968 г.
4 Малов А.Н. Справочник металлиста., Т3 М.: Машиностроение, 1977 г.
5 Абрамов Ф.Н. Справочник по обработке металлов резанием. К.: Машиностроение, 1983. 239 с.
6 Общемашиностроительные нормативы режимов резания, 4.1 – М.: Машиностроение, 1974 г.
7 Нефедов Н.А., Осипов К.А. Сборник задач и примеров по резанию металлов и режущему инструменту. М.: Машиностроение, 1990.-448 с.
8 Долматовский Г.А. Справочник технолога, М.: Машиностроение, 1956 г.
9 Баранчиков В.И., Жаринов А.В. Прогрессивные режущие инструменты и режимы резания металлов. – М.: Машиностроение, 1990.-400 с.
Приложение 1
Выбор диаметра фрезы в зависимости от вида фрезерования
При торцовом фрезеровании диаметр фрезы определяется по формуле
Dф = 1,6 · В,
где В – ширина фрезерования, мм.
При фрезеровании дисковыми фрезами диаметр фрезы выбирается по ГОСТ в зависимости от ширины фрезерования В.
При фрезеровании концевыми и шпоночными фрезами диаметр фрезы можно принимать равным ширине фрезерования В.
Определение числа зубьев фрезы
Число зубьев фрезы из быстрорежущей стали при черновой обработке определяется по формуле
,
где Dф – диаметр фрезы, мм
При чистовой обработке
Для фрез, оснащенных твердым сплавом, число зубьев определяется следующим образом:
- для обработки чугуна z = (0,08÷0,1)·D;
- для обработки стали z = (0,04÷0,06)·D;
Для цилиндрических фрез число зубьев определяется по формуле
,
где m – коэффициент, определяется по таблице 1
Таблица 1
Цилиндрические фрезы | Угол наклона зуба ω | Коэффициент m |
С крупным зубом цельные | 1,05 | |
С мелким зубом цельные | 15 – 20 ° | 2 |
С крупным зубом сборные | 20 ° 45 ° 55 – 60 ° | 0,9 0,8 0,5 |
Расчет времени цикла обработки с ЧПУ
Расчет времени цикла обработки с ЧПУ
Опубликовано: 3 ноября 2021 г.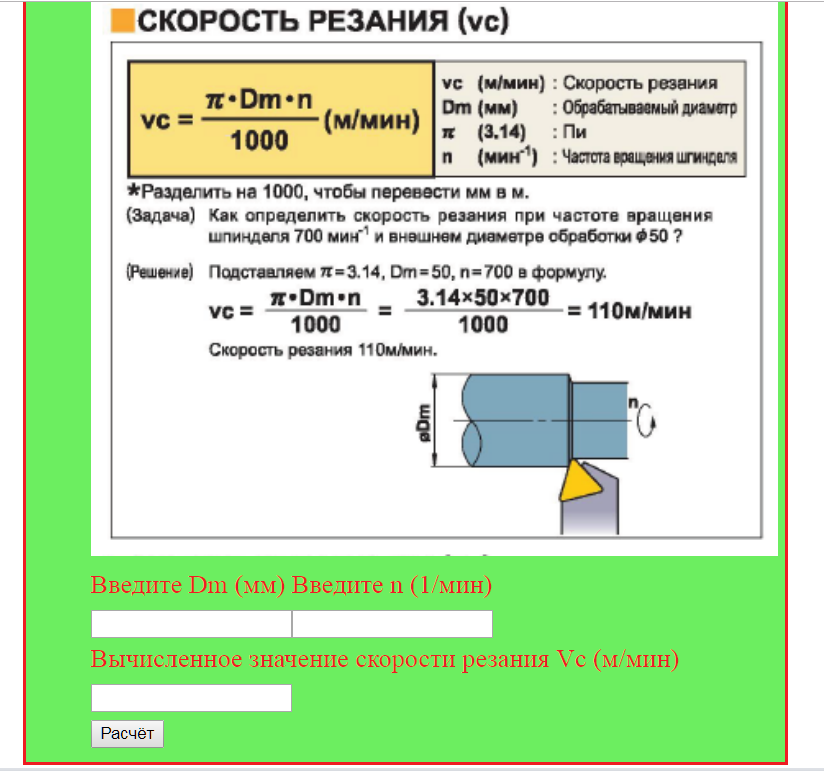
Если вам нужны уникальные детали, которые вы не можете найти больше нигде, обработка с ЧПУ — это процесс, который позволяет создавать точные компоненты для любой отрасли. Благодаря нашим полным производственным мощностям, высококачественным материалам и возможностям настройки, American Micro Industries может производить детали в соответствии с вашими спецификациями чертежа.
Но если вы работаете над проектом механической обработки самостоятельно, важно знать время цикла обработки ЧПУ и способы его расчета. Продолжайте читать, чтобы лучше понять необходимые расчеты и когда их использовать.
Что такое обработка с ЧПУ?
CNC-обработка или компьютеризированное числовое управление — это процесс, при котором запрограммированное компьютерное программное обеспечение управляет движениями вашего производственного оборудования. Эта технология берет виртуальный проект, часто из программы САПР, и преобразует его в физическую деталь, изготовленную из определенного материала, который вам нужен, например:
- Жесткий пенопласт
- Пена для резьбы
- Фенолы
- Пластик
Обработка с ЧПУ заменяет ручной труд для создания точных и уникальных деталей, независимо от вашей отрасли. Независимо от того, работаете ли вы в автомобильной, аэрокосмической, электронной, военной, медицинской или охранной отраслях, обработка с ЧПУ, скорее всего, принесет вам пользу. Когда вам нужны детали массового производства, отвечающие конкретным требованиям, обработка с ЧПУ может разработать и предоставить точные и точные решения.
Узнайте больше об услугах по обработке с ЧПУ
Что такое время цикла обработки с ЧПУ?
Понимание времени цикла станка с ЧПУ поможет вам оценить затраты на обработку и сократить время производства продукции. Сколько времени займет выполнение операции? Соответствует ли ваш бюджет проекту? Будет ли это сделано вовремя для вас или вашего клиента? Знание продолжительности цикла обработки также может помочь вам сравнить два или более разных процесса, которые лучше всего подходят для проекта.
Формулы, используемые для расчета времени обработки, легко включить в ваши повседневные операции, и многие профессионалы программируют свои калькуляторы на соответствующую формулу времени цикла обработки с ЧПУ. Однако, в зависимости от типа обработки с ЧПУ, такой как точение, фрезерование или обработка винтов, расчет времени цикла будет отличаться, что делает процесс немного сложным. К счастью, с помощью простой формулы вы можете упростить обработку с ЧПУ.
Как рассчитать время обработки с ЧПУ
Как и при расчете других времен, общая формула для обработки с ЧПУ представляет собой расстояние или длину, деленную на скорость или скорость. Когда дело доходит до расчета времени обработки, формула выглядит следующим образом:
- Время обработки = длина резания (мм) / подача (мм на оборот) x число оборотов в минуту
- оборотов в минуту = 1000 x скорость резания (мм в минуту) / π x диаметр стержня (мм)
В зависимости от проекта вам может понадобиться заменить миллиметры на дюймы.
Пример времени обработки с ЧПУ
Давайте начнем с примера в дюймах с ожидаемой целью:
- Диаметр отверстия = 1 дюйм
- Глубина отверстия = 0,75 дюйма
- Расстояние приближения = 0,1 дюйма
- Подача = 7 дюймов/минуту
Время, необходимое для сверления отверстия, даст десятичные минуты, которые необходимо преобразовать в секунды:
- Время сверления отверстия = расстояние перемещения (0,85) / скорость подачи (7) = 0,12143 минуты
- секунд = 0,12143 минуты / 0,0166 = 7,2887 секунды
Как только вы узнаете, сколько времени потребуется, чтобы просверлить отверстие, вы захотите определить скорость подачи в дюймах в минуту (IPM), что означает, что вы должны рассчитать RMP шпинделя и рассчитать скорость подачи в дюймах в минуту, поскольку в большинстве справочников подача указана в дюймах на оборот (IPR). Затем, поскольку рекомендации по скорости часто предоставляются при расчете поверхности в минуту (SFM), вам понадобятся следующие две формулы, которые помогут вам завершить расчеты:
- оборотов в минуту = 3,82 x SFM / общий диаметр
- IPM = оборотов в минуту x дюймов на оборот
В зависимости от инструмента скорость подачи может быть выражена в «на зуб», что мы рассмотрим, когда будем говорить о расчете времени фрезерной обработки с ЧПУ. В этом случае формула будет следующей:
- дюймов на оборот = IPT x количество режущих кромок
Эти формулы легко применить ко многим операциям, если только диаметр не меняется в процессе обработки. Например, если вы работаете над проектом, который требует нескольких проходов, постоянная скорость резания приведет к изменению скорости шпинделя в оборотах в минуту в зависимости от диаметра. Следовательно, вам нужно будет рассчитать новую скорость подачи RPM и IPM для каждого токарного прохода.
Хотя это общая формула, существуют различия между расчетами на фрезерном и токарном станках.
Фрезерование с ЧПУ Расчет времени обработки
Процесс ЧПУ, называемый фрезерованием, создает пазы, винтовые канавки или плоские поверхности на вертикальных, наклонных или горизонтальных плоскостях. В этом случае при оценке времени обработки с ЧПУ может использоваться скорость подачи на зуб, а это означает, что вам необходимо знать количество канавок, зубьев или режущих кромок на конкретном инструменте, который у вас есть.
При использовании исходной формулы для справки — Время обработки = длина реза (мм) / подача (мм на оборот) x число оборотов в минуту — расчет времени фрезерной обработки с ЧПУ равен Время обработки = длина реза (мм) x количество число проходов/подача (мм на оборот) x число оборотов в минуту со следующими характеристиками:
- Длина резания (мм) = Подход инструмента + Длина работы + Перебег инструмента + Обязательное расстояние
- Подача (мм на оборот) = подача на зуб x количество зубьев
- оборотов в минуту = 1000 x скорость резания / π x диаметр стержня (мм)
Здесь точность является ключом к получению наилучшей оценки времени обработки.
Расчет времени токарной обработки с ЧПУ
Для расчета времени цикла токарной обработки формула также основана на оригинале. Например, Время обработки = длина реза (мм) / подача (мм на оборот) x число оборотов в минуту со следующими характеристиками:
- Длина = подход инструмента + длина работы + проход инструмента x количество проходов
- Среднее число оборотов в минуту = 1000 x Скорость резания / π x Средний диаметр стержня (мм)
Процесс токарной обработки заключается в том, что одноточечный инструмент на токарном станке создает токарные детали. Для изготовления вращающихся — и часто сложных — форм инструмент подается линейно или перпендикулярно оси вращения детали, или инструмент движется по заданной траектории для создания вращательной формы. В процессе токарной обработки есть два движения резания — основное — это вращение заготовки, а второе — подача.
Узнайте больше о наших услугах по обработке с ЧПУ
Компания American Micro Industries стремится превзойти ваши ожидания, руководствуясь качеством и уделяя особое внимание изготовлению отдельных деталей по вашим спецификациям. Эксперты AMI специализируются на производстве труднодоступных деталей, принимая во внимание ваши идеи, чертежи и проекты САПР и помогая вам определить подходящие материалы для производства и доставки продукции из одного места. Здесь у наших профессиональных команд есть бесконечные возможности, чтобы помочь поддержать ваш растущий бизнес.
Для получения дополнительной информации запросите бесплатный расчет стоимости онлайн или позвоните представителю American Micro Industries по телефону 866-774-9353.
Формула для расчета процесса резки|A.L.M.T. Corp.
Расчет токарной обработки
Расчет токарной обработки [Расчет скорости резания и скорости вращения]
(1) Расчет скорости вращения по скорости резания
VC: скорость резания (м/мин)
Dm: диаметр заготовки ( мм)
n:Скорость шпинделя(мин -1 )
(2) Расчет скорости резания по скорости вращения
Dm:диаметр заготовки(мм)
n:скорость шпинделя(мин -1 )
VC: Скорость резания (м/мин)
Расчет [Расчет требуемой мощности]
VC: скорость резания (м/мин)
f: скорость подачи (мм/об)
ap: глубина резания (мм)
KC: удельная сила резания (МПа) )
η:КПД машины(0. 7~0.85)
ПК:Потребляемая мощность(кВт)
H: Требуемая мощность (л.с.)
Расчет токарной обработки [Расчет силы резания]
KC: Удельная сила резания (МПа)
q: Площадь стружки (мм 2 )
p:Усилие резания(кН)
KC: сила резания (МПа)
ap: глубина резания (мм)
f: скорость подачи (мм/об)
p: сила резания (кН)
9 0128 Расчет токарной обработки [Расчет шероховатости обрабатываемой поверхности]f:Скорость подачи(мм/об)
RE:Радиус вершины(мм)
h:Теоретическая шероховатость поверхности(мкм)
Расчет токарной обработки [Расчет количества отвода стружки]
VC:Скорость резания(м/мин)
ap:Глубина резания(мм)
90 004 f:Скорость подачи(мм /об)Q:Количество выхода стружки(см 3 /мин)
Расчет токарной обработки [Расчет времени обработки (OD)]
(1) Расчет по скорости шпинделя
L:Длина обработки(мм )
f:Скорость подачи(мм/об)
n:Скорость шпинделя(мин -1 )
T:Время обработки(сек)
(2) Расчет по скорости резания
L:Длина обработки(мм)
f:Подача(мм/об) 9 0005
Dm:OD работы материал (мм)
VC: скорость резания (м/мин)
T: время обработки (сек)
Расчет токарной обработки [Расчет времени обработки (канавка)]
f: скорость подачи (мм/об)
n: скорость шпинделя (мин. -1 )
D1: макс. диаметр рабочего материала (мм)
D2: Мин. диаметр обрабатываемого материала (мм)
T: время обработки (сек)
Расчет токарной обработки [Расчет времени обработки (отрезание)]
f: скорость подачи (мм/об)
n: скорость вращения шпинделя (мин.) -1 )
D1: макс. диаметр обрабатываемого материала (мм)
T: время обработки (сек)
Расчетные формулы фрезерования
Расчетные формулы фрезерования [Расчет скорости резания]
(1) Расчет скорости резания
DC:диаметр фрезы(мм)
n:скорость вращения(мин -1 )
VC:скорость резания(м/мин)
(2) Расчет скорости вращения
900 04 VC:Скорость резания(м/мин )DC:диаметр фрезы(мм)
n:скорость вращения(мин -1 )
Расчетные формулы фрезерования [Расчет скорости подачи]
(1) Скорость подачи в минуту
fz:Подача на зуб (мм/т)
Z:Количество зубьев (шт. )
n:Скорость вращения(мин -1 )
Vf: Скорость подачи в минуту (м/мин)
(2) Скорость подачи на зуб
Vf: Скорость подачи в минуту (м/мин)
Z: Количество зубьев (шт.) )
n: скорость вращения (мин. -1 )
fz: подача на зуб (мм/зуб) )
Vf: Скорость подачи в минуту(мм/мин)
ap:Глубина резания(мм)
Q:Количество удаления стружки(см 3 /мин)
Расчетные формулы для фрезерования [Расчет потребляемой мощности]
ae:Ширина резания(мм)
apГлубина резания(мм)
KC:Удельная сила резания(МПа )
vf:Скорость подачи стола в минуту (мм/мин)
η: КПД станка (около 0,75)
Pc: Требуемая мощность (кВт)
Q: Количество удаления стружки (см 3 /мин)
9000 4 KC:Удельная сила резания(МПа )η: КПД машины (около 0,75)
Pc: Требуемая мощность (кВт)
Расчетные формулы для фрезерования [Расчет требуемой мощности]
PC: Требуемая мощность (кВт)
H: Требуемая мощность (в лошадиных силах)
Расчетные формулы для концевого фрезерования
9012 8 (1) Расчет скорости резанияDC:диаметр концевой фрезы(мм)
n:скорость шпинделя(мин -1 )
VC:скорость резания(м/мин)
(2) Расчет скорости шпинделя
VC:Скорость резания(м/мин )
DC:Диаметр концевой фрезы(мм)
n:Скорость шпинделя(мин -1 )
(3) Расчет скорости подачи в минуту (1)
f:Скорость подачи на зуб(мм/об)
n:Скорость шпинделя(мин -1 )
Vf: Скорость подачи в минуту (м/мин)
(4) Расчет скорости подачи в минуту (2)
Z: Количество зубьев (шт.