Твердые сплавы. Виды, области применения
Твёрдые сплавы получают методами порошковой металлургии в виде пластин. Основными компонентами таких сплавов являются карбиды вольфрама (WC), титана (TiC) и тантала (ТаС), мельчайшие частицы которых соединены сравнительно мягким и менее тугоплавким кобальтом. Карбиды придают сплаву высокую твёрдость и теплостойкость, кобальт – прочность на изгиб.
Твердые сплавы имеют высокую твердость – 72…76 HRC и теплостойкость до 850… 1000 °С. Это позволяет работать со скоростями резания в 3 – 4 раза большими, чем инструментами из быстрорежущих сталей.
Применяемые в настоящее время твердые сплавы делятся на:
- Вольфрамовые сплавы группы ВК: ВК3, ВК3-М, ВК4, ВК6, ВК6-М, ВК6-ОМ, ВК8 и др.
В условном обозначении цифра показывает процентное содержание кобальта. Например, обозначение ВК8 показывает, что в нем 8 % кобальта и 92 % карбидов вольфрама.
- Титановольфрамовые сплавы группы ТК: Т5К10, Т15К6, Т14К8, ТЗОК4, Т60К6 и др. В условном обозначении цифра, стоящая после буквы Т, показывает процентное содержание карбидов титана, после буквы К — кобальта, остальное — карбиды вольфрама;
- Титанотанталовольфрамовые сплавы группы ТТК: ТТ7К12, ТТ8К6, ТТ20К9 и др. В условном обозначении цифры, стоящие после буквы Т, показывают процентное содержание карбидов титана и тантала, после буквы К – кобальта, остальное – карбиды вольфрама.
Твердые сплавы выпускаются в виде стандартизованных пластин, которые припаиваются, или крепятся механически к державкам из конструкционной стали.
Правильным выбором марки твердого сплава обеспечивается эффективная эксплуатация режущих инструментов. Для конкретного случая
обработки сплав выбирают исходя из оптимального сочетания его теплостойкости и прочности.
Инструменты из твердых сплавов группы ВК применяют при обработке деталей из конструкционных сталей в условиях низкой жесткости системы СПИД, при прерывистом резании, при работе с ударами, а также при обработке хрупких материалов типа чугуна, что обусловлено повышенной прочностью этой группы твердых сплавов и невысокими температурами в зоне резания.
Такие сплавы используются также при обработке деталей из высокопрочных, жаропрочных и нержавеющих сталей, титановых сплавов. Это объясняется тем, что наличие в большинстве этих материалов титана вызывает повышенную адгезию со сплавами группы ТК, также содержащими титан. Кроме того, сплавы группы ТК имеют значительно худшую теплопроводность и более низкую прочность, чем сплавы ВК.
Сплавы группы ТТК занимают промежуточное положение между сплавами ТК и ВК. Сплавы ТТК по применимости – универсальны.
Основная область их применения – резание с очень большими сечениями срезаемого слоя, тяжёлыми ударами и малыми скоростями резания (строгание и долбление).
Сплавы с низким процентным содержанием кобальта (Т30К4, ВК3, ВК4) обладают высокой твёрдостью, малой прочностью на изгиб и меньшей вязкостью. Применяются для чистовых операций. Наоборот, сплавы с большим содержанием кобальта (ВК8, Т14К8, Т5К10) являются более вязкими, обладают высокой прочностью на изгиб и применяются при снятии стружек большого сечения на черновых операциях.
Работоспособность твердых сплавов значительно возрастает при нанесении на них износостойких покрытий.
Победитовый пруток ВК8 в Москве
Победитовый пруток ВК8 купить по выгодным ценам
Мы осуществляем оперативную доставку по городу Москва, а также в другие регионы России и страны СНГ.
Для заказа позвоните по телефону +7 (499) 444-61-35 или оставьте заявку на почту [email protected].
Менеджеры представительства в городе Москва ответят на вопросы и помогут рассчитать стоимость товара.
Пруток победитовый ВК8
Пруток ВК8 относится к разряду твердых спеченных сплавов карбидо-вольфрамовой группы с легированием кобальтом (Со). В его наименовании ВК (карбид вольфрама) цифра после обозначения указывает на вхождение кобальта. Производство таких сплавов регулируется ГОСТом 3882-74. Он определяет вхождение карбида вольфрама WC на уровне 92%, включение кобальта на уровне 8%, дополнение сплава карбидом титана, танталом, углеродом, хромом. За счет карбида пруток получает твёрдость и пластичность, а за счет кобальта создается качественная цементирующая связка. За химический состав ВК8 отвечает стандарт ТУ 48-19-60-78.
Характеристики
Нормативные документы определяют для прутков ВК8 показатели:
- прочности на изгиб – 1700 Мпа;
- твердости – 88,5НRA;
- плотности – 14,8 г/см3;
- теплопроводности – 50,2 Вт/м.
Твердые прутки ВК8 характеризуются высокой износостойкостью и красностойкостью, работоспособностью в условиях температурного режима от +800°C до +1000 °C. Эти характеристики влияют на возможность высокоскоростной обработки со скоростью резания 800 м/мин.
Производство
Порошок ВК8 служит стартовым сырьем для изготовления одноименного твердого сплава. С помощью методов порошковой металлургии и технологических процессов создаются твердосплавные материалы по схеме: формовка мельчайших частиц/горячее прессование в вакууме/спекание в водороде. По ГОСТ 25405-90 отливаются пластины с разной конструкцией и размерами для бандажных и галтельных резцов. Их припаивают к корпусу инструмента.
Применение
Твердый сплав ВК8 используется для оснащения режущего инструмента, фрез, развёрток, резцов, зубонарезного и резьбонарезного оборудования, протяжек, горнорудного оснащения, быстроизнашивающихся деталей, механизмов, приборов, приспособлений. Основные сферы применения твердосплавных пластин ВК8:
- станкостроение;
- машиностроение;
- горнодобывающая промышленность;
- деревообработка;
- механическая обработка.
Победитовыми пластинами ВК8 обрабатывают белый, серый, высокопрочный чугун, стальной, цветной металлопрокат, различные сплавы, неметаллические материалы. ВК8 используются для обработки высокопрочных, жаропрочных, нержавеющих и труднообрабатываемых сталей, титановых сплавов.
Другие товары
СВЕРЛО СПИРАЛЬНОЕ С КОНИЧЕСКИМ ХВОСТОВИКОМ С ТВЕРДОСПЛАВНОЙ ПЛАСТИНОЙ ИЗ СПЛАВА ВК8, ГОСТ 22736-77
Описание
Характеристики:
Длина: Нормальная
Твердый сплав: ВК8
Класс точности: B
от 8 мм до 30 мм (шаг 0,5 мм): от 8 мм до 30 мм (шаг 0,5 мм)
Область применения:
Для высокопроизводительного сверления цилиндрических отверстий в заготовках и изделиях из чугунов, стекло наполненных пластмасс (текстолитах), закаленных сталей. Фиксация – во внутренний конус Морзе напрямую или через переходные втулки.
Наименование:
Сверло к/х ср. сер 8,0 (кл.В) с пл. ВК8 (l=75, L=156, КМ1, Р6М5)
Сверло к/х ср. сер 10,0 (кл.В) с пл. ВК8 (l=87, L=168, КМ1, Р6М5)
Сверло к/х ср. сер 11,0 (кл.В) с пл. ВК8 (l=94, L=175,КМ1, Р6М5)
Сверло к/х ср. сер 11,5 (кл.В) с пл. ВК8 (l=94, L=175,КМ1, Р6М5)
Сверло к/х ср. сер 12,0 (кл.В) с пл. ВК8 (l=101, L=182,КМ1, Р6М5)
Сверло к/х ср. сер 12,5 (кл.В) с пл. ВК8 (l=101, L=182,КМ1, Р6М5)
Сверло к/х ср. сер 13,0 (кл.В) с пл. ВК8 (l=101, L=182,КМ1, Р6М5)
Сверло к/х ср. сер 15,0 (кл.В) с пл. ВК8 (l=114, L=212,КМ2, Р6М5)
Сверло к/х ср. сер 16,0 (кл.В) с пл. ВК8 (l=120, L=218,КМ2, Р6М5)
Сверло к/х ср. сер 17,0 (кл.В) с пл. ВК8 (l=125, L=223,КМ2, Р6М5)
Сверло к/х ср. сер 18,0 (кл.В) с пл. ВК8 (l=130, L=228,КМ2, Р6М5)
Сверло к/х ср. сер 19,0 (кл.В) с пл. ВК8 (l=135, L=233,КМ3, Р6М5)
Сверло к/х ср.
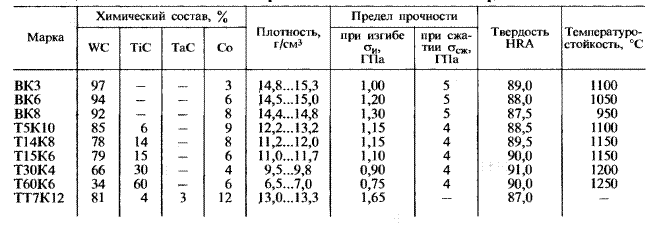
Сверло к/х ср. сер 21,0 (кл.В) с пл. ВК8 (l=145, L=243,КМ3, Р6М5)
Сверло к/х ср. сер 22,0 (кл.В) с пл. ВК8 (l=150, L=248,КМ3, Р6М5)
Сверло к/х ср. сер 23,0 (кл.В) с пл. ВК8 (l=155, L=253,КМ3, Р6М5)
Сверло к/х ср. сер 24,0 (кл.В) с пл. ВК8 (l=160, L=281,КМ3, Р6М5)
Сверло к/х ср. сер 25,0 (кл.В) с пл. ВК8 (l=160, L=281,КМ3, Р6М5)
Сверло к/х ср. сер 26,0 (кл.В) с пл. ВК8 (l=165, L=286,КМ3, Р6М5)
Сверло к/х ср. сер 28,0 (кл.В) с пл. ВК8 (l=170, L=291,КМ3, Р6М5)
Сверло к/х ср. сер 29,0 (кл.В) с пл. ВК8 (l=175, L=296,КМ3, Р6М5)
Сверло к/х ср. сер 30,0 (кл.В) с пл. ВК8 (l=175, L=296,КМ3, Р6М5)
Твердосплавные сверла по металлу
Высокую эффективность при обработке изделий из таких материалов, как чугун, цветные металлы, пластик, искусственный и натуральный камень, кирпич и бетон, демонстрируют твердосплавные сверла. Такое название они получили из-за того, что на их режущую часть напаиваются специальные пластинки из твердых сплавов. Использование этих сверл позволяет, например, почти в два раза увеличить производительность обработки чугуна по сравнению со сверлением, выполняемым инструментом из быстрорежущей стали.
Сверла твердосплавные для вырезания отверстий в рельсах
Несмотря на то, что режущие пластины, которыми оснащено такое сверло, отличаются исключительно высокой твердостью и износостойкостью, для обработки изделий из стали оно применяется нечасто, так как для этого необходимо обеспечить высокую жесткость рабочих элементов используемого оборудования. Если соблюдение этого требования не будет обеспечено, возникнет вибрация инструмента, которая приведет к выкрашиванию и даже выламыванию твердосплавных пластинок.
Критерии выбора
Выбирая твердосплавные сверла, которые могут иметь различные геометрические параметры и конструктивное исполнение, следует учитывать следующие характеристики: материал изделия, в котором необходимо просверлить отверстие, а также диаметр и глубину последнего. Наиболее значимыми параметрами, на которые необходимо обращать внимание, выбирая сверло с твердосплавными пластинами, являются:
- материал, из которого выполнена режущая часть;
- прочность используемого твердого сплава;
- качество изготовления сверла;
- торговая марка и страна-производитель;
- стоимость.
Сверла с твердосплавными пластинами для дрели имеют острые режущие грани
Несмотря на то, что сверла твердосплавные, выпущенные под известными торговыми марками, отличаются самой высокой ценой на рынке, выбирать желательно именно их, так как их качество и надежность находятся на самом высоком уровне. Учитывая тот факт, что любое твердосплавное сверло стоит недешево, выбирать инструмент сомнительного качества от неизвестных производителей не имеет никакого смысла.
Виды сверл с твердосплавными пластинами
На современном рынке представлено большое разнообразие твердосплавных сверл, предназначенных для выполнения работ по металлу и другим материалам. Классификация такого инструмента осуществляется по нескольким параметрам, к которым, в частности, относятся:
- материал изготовления твердосплавной пластины, в качестве которого могут использоваться сплавы марок ВК6, ВК8 и др.;
- способ крепления твердосплавных пластинок к основной части сверла;
- форма, которую имеют твердосплавные пластинки;
- форма канавок между рабочими поверхностями сверла, предназначенных для эффективного отвода отходов обработки.
В качестве материала изготовления режущих пластинок, которыми оснащается твердосплавное сверло, используются преимущественно сплавы вольфрамо-карбидной группы. Наиболее популярным является сплав марки ВК8.
Свойства и применение сплавов вольфрамовой группы
Такие сплавы, получаемые преимущественно методами порошковой металлургии, полностью соответствуют своему названию – «твердые». В частности, твердость популярного сплава марки ВК8 в зависимости от условий его производства находится в интервале 1670–2800 единиц по шкале Роквелла. Благодаря этому сверло, оснащенное режущими пластинами из сплава ВК8, можно успешно использовать для выполнения отверстий в таких материалах, как легированные стали (в том числе жаростойкой группы), чугун, твердые породы дерева. Немаловажным является и то, что сплав марки ВК8 по сравнению с другими твердосплавными материалами отличается доступной стоимостью.
Твердосплавные пластинки могут фиксироваться на режущей части сверла при помощи пайки или посредством винтового (механического) соединения. В первом случае твердосплавные пластины могут перетачиваться ограниченное количество раз, хотя и характеризуются более высокой надежностью. Кроме того, они довольно часто ломаются. Именно поэтому большую популярность завоевал инструмент, неперетачиваемые режущие пластины на котором крепятся механическим способом.
Типы твердосплавных пластин, используемых для сверл
Для оснащения сверл данного типа используются твердосплавные пластины в форме:
- параллелограмма;
- прямоугольника;
- ромба;
- неправильного треугольника (такие пластины характеризуются наличием шести режущих кромок).
Большое значение при использовании твердосплавных сверл по обработке металла и других материалов имеет форма канавок между рабочими поверхностями инструмента. Вне зависимости от формы таких канавок их внутренняя поверхность должна быть тщательно отполирована, что позволит обеспечить эффективный отвод стружки из зоны обработки.
Твердосплавное сверло с внутренней подачей охлаждающей жидкости
Особенности конструкции инструмента
Сверла с твердосплавными пластинами характеризуются рядом конструктивных особенностей. Перечислим наиболее важные.
- Уменьшенная на 20–35% рабочая длина сверла объясняется тем, что его переточка выполняется только по твердосплавной пластине. Длина сверл данного типа, если они используются в комплекте с кондуктором, может быть такой же, как и у быстрорежущего инструмента.
- Увеличение диаметра сердцевины сверла по направлению к хвостовику выполняется в пределах 1,4–1,8 мм на каждые 100 мм длины, как и у сверлильных инструментов других категорий.
- Величина угла наклона винтовой канавки инструмента зависит от того, какой глубины отверстие необходимо сделать.
- На поперечной кромке сверла необходимо выполнять подточку с размерами 1,8–3,5 мм, которая позволяет снизить осевые усилия и уменьшить нагрузку на тело инструмента.
- Конусный хвостовик, при помощи которого сверло фиксируется в шпинделе станка, должен быть точно подогнан под посадочную часть, что увеличит жесткость крепления сверла и минимизирует риск возникновения вибрационных нагрузок, могущих стать причиной выкрашивания твердосплавной пластины и даже ее поломки.
- Чтобы повысить надежность использования твердосплавных сверл по металлу, в их внутренней части часто выполняют отверстие для подачи смазывающе-охлаждающей жидкости. Это позволяет уменьшить температуру резания, уменьшить интенсивность износа инструмента, а также облегчить процесс отвода стружки из зоны обработки.
Устройство сверла со съемными пластинами
Чтобы придать рабочей части сверла требуемую твердость (56–62 единицы по шкале HRC), инструмент подвергают термической обработке, которую, как правило, выполняют одновременно с напайкой твердосплавных пластин.
Высокую производительность обработки, а также устойчивость сверл данной категории обеспечивает целый ряд параметров. Сюда относятся форма твердосплавной пластины, геометрические параметры ее передней поверхности, а также материал, из которого такая пластина выполнена. В настоящее время наибольшее распространение получили инструменты с твердосплавными пластинами правильной трех- и четырехгранной конфигурации, которые позволяют выполнять сверление отверстий с практически плоским дном.
Более качественных результатов сверления можно добиться, если использовать инструмент, оснащенный профилированными твердосплавными пластинами.
Сверла с такими пластинами, режущая часть которых выполнена в форме волны, позволяет выполнять обработку по технологии пошагового врезания. Использование последней не только обеспечивает стабилизацию положения инструмента в момент его врезания в обрабатываемый материал, но и минимизирует риск его увода в процессе выполнения дальнейшей обработки. Кроме того, сверло с волнообразной режущей кромкой позволяет значительно снизить силы резания, формирующиеся в процессе сверления.
Сверла с механическим креплением сменных многогранных пластин (сверла с МНП)
Конструкция сверл, оснащенных съемными твердосплавными пластинами, позволяет выполнять с их помощью не только сверление, но и такие технологические операции, как растачивание заранее выполненных отверстий, обработка фасок. В таких случаях задействуется периферийная твердосплавная пластина, закрепленная на инструменте.
Сверла с твердыми пластинами, которые закреплены на инструменте механическим способом, эффективно используются для обработки наклонных и вогнутых поверхностей, при этом обработка таким инструментом может выполняться без предварительного засверливания отверстий. Чтобы успешно справиться с такой технологической задачей, величину подачи, с которой инструмент врезается в обрабатываемый материал, необходимо уменьшить на 50–70%.
youtube.com/embed/91k_lsMGumc”/>Охлаждение и смазка твердосплавных сверл
Как уже говорилось выше, чтобы сделать обработку сверлом с твердосплавными пластинами более эффективной, необходимо обеспечить внутреннее охлаждение инструмента. Не использовать при применении таких сверл смазывающе-охлаждающую жидкость можно в тех случаях, когда глубина формируемого отверстия не превышает одного диаметра инструмента.
На качество выполняемого отверстия, а также на скорость его сверления оказывает влияние не только количество подаваемой во внутреннюю полость сверла СОЖ (не менее 12–15 л/мин), но и величина напора (не менее 12–15 Атм). Смазывающе-охлаждающая жидкость, подаваемая в зону обработки в таком количестве и с таким напором, обеспечивает не только интенсивное охлаждение инструмента, но и эффективный отвод стружки и других отходов сверления.
Сверление с наружной подачей охлаждающей жидкости
Полезные рекомендации
Прежде чем делать отверстие в изделии из металла, используя в том числе твердосплавное сверло, следует выполнить центровку инструмента. Для этого можно использовать такое удобное приспособление, как центрирующий штифт. При этом место на поверхности изделия, на котором будет располагаться центр будущего отверстия, следует предварительно накернить.
Важным параметром при использовании сверл с твердосплавными платинами является скорость, с которой выполняется обработка. При использовании такого инструмента скорость вращения шпинделя станка должна быть не ниже 25% от рекомендованного параметра. Очень важно сильно не занижать и не превышать (более чем на 20%) рекомендованную скорость вращения сверла, так как это может привести к возникновению вибрации инструмента, выкрашиванию и даже выламыванию твердосплавных пластин, которыми он оснащен.
Режимы резания сверлами с СМП
Такой параметр сверления, как подача режущего инструмента, также имеет большое значение. На начальной стадии сверления сверло необходимо подавать со скоростью, которая в два раза ниже рекомендованной, а по мере врезания в обрабатываемый материал данный параметр можно постепенно увеличивать. При этом следует иметь в виду: если сверление выполняется затупившимся инструментом или обрабатываемый материал слишком твердый, увеличить скорость подачи не получится, какое бы сильное давление на сверло вы ни оказывали.
И в заключение небольшое видео о том, как просверлить каленый металл с помощью твердосплавных сверл.
Металлокерамические твердые сплавы и их применение
Твердые сплавы – материала, состоящие из карбидов вольфрама, титана и тантала с добавлением кобальта как связующего вещества, отличающегося прочностью на изгиб. Особенностью этих материалов выступает высокая твердость зерен, от 13 до 25 ГПа для карбида вольфрама.
Изделия из твердых сплавов получают методами порошковой металлургии
Изделия из твердых сплавов получают методами порошковой металлургии. Из-за высокого содержания вольфрама, тантала и других дорогих веществ стоимость твердых сплавов выше, чем инструментальной стали. По этой причине из твердых сплавов производят только пластины, которые устанавливаются на тело режущего инструмента. Твердость пластин доходит до 72-76 HRC, а рабочие температуры до 850-1000°С, благодаря чему они обрабатывают сталь в 3-4 раза быстрее по сравнению с инструментом из быстрорежущих сталей.
Твердые сплавы делят на группы в зависимости от входящих соединений:
- Однокарбидные. Состоят только из карбида вольфрама и кобальта.
- Двухкарбидные. В состав входят карбиды вольфрама и титана и кобальт как связующее вещество.
- Трехкарбидные. Твердая фаза состоит из карбидов вольфрама, титана и тантала, связывающая – из кобальта.
В России стандартом для твердых сплавов выступает ГОСТ 3882-74. Зарубежные компании используют собственные стандарты.
Однокарбидные твердые сплавы
Твердые сплавы, в состав которых входит только карбид вольфрама, обозначают буквами ВК и цифрой, указывающей на содержание кобальта. Так, сплав ВК3 содержит 3% кобальта и 97% вольфрама, ВК8 – 8% и 92% соответственно. В сплаве ВК10-ХОМ присутствует также карбид хрома, но по классификации он относится к однокарбидным.
С увеличением содержания кобальта возрастает предел прочности на поперченный изгиб и прочность во время резки, но снижается износостойкость и твердость. Сплав ВК3 со значительным содержанием карбида вольфрама подходит для чистовой обработки, при которой скорость резки максимальна. Сплавы ВК8 и ВК10-ХОМ используются в черновой обработке и при ударных нагрузках.
Твердые сплавы карбида вольфрама и кобальта используются для работы с материалами, которые образуют стружку, состоящую из отдельных частиц, не связанных друг с другом. К ним относят хрупкие материалы, такие как чугун, цветные сплавы на основе никеля и титана, фарфор, стекло и стеклопластики. К хрупким относятся стали с повышенной стойкостью к коррозии и высоким температурам.
Металлокерамические твердые сплавы и их применение
⇐ ПредыдущаяСтр 2 из 4Следующая ⇒
Металлокерамические твердые сплавы представляют сoбoй композиции, состоящие из особо твердых тугоплавких соединений в сочетании с вязким связующим металлом.
Наибольшее практическое применение для производства металлокерамических твердых сплавов имеют карбиды WC, TiC и ТаС. Связующим металлом в спечённых твердых сплавах является кобальт, а иногда никель и железо.
В зависимости от состава карбидной фазы твердые сплавы разделяют на три основные группы:
· однокарбид-пые сплавы WC — Со (типа ВК),
· дзухкарбидные сплавы WC—Ti С—Со (типа ТК),
· трехкарбидные сплавы WC—TiC—ТаС—Со (типаТТК).
Сплавы первой группы
различаются по содержанию кобальта (2…30%) и по зернистости карбидной фазы. С увеличением содержания кобальта растет вязкость сплава, но снижается твердость и износостойкость. Укрупнение зерен карбида вольфрама повышает вязкость сплава, но снижает твердость.
Однокарбидные сплавы применяют для изготовления режущих инструментов, предназначенных для обработки хрупких материалов: чугуна, цветных металлов и сплавов, неметаллических материалов (резины, фибры, пластмасс), а также нержавеющих и жаропрочных сталей, титана и его сплавов. Сплавы с низким содержание кобальта ВК2, ВКЗ, ВКЗМ, ВК4 применяют для чисто вой и получистовой обработки, а сплавы В Кб, ВК6М, ВК8 — Для черновой обработки. Вязкие сплавы с большим содержанием кобальта (более 20%) используют для оснащения штампового инструмента, работающего при значительных ударных нагрузках. Мелкозернистые твердые сплавы (ВКЗМ, ВК6М) применяют при обработке твердых чугуиов по литейной корке. Если в марке стоит буква В (ВК4В), это значит, что сплавы изготовлены из крупнозернистого карбида вольфрама.
Сплавы второй группы
благодаря высокой твердости и износостойкости применяют преимущественно при высокоскоростной обработке сталей резанием. Свойства сплавов определяются содержанием карбида титана и кобальта. С увеличением содержания TiC повышается износостойкость сплава и уменьшается его прочность, а увеличение содержания кобальта повышает вязкость и снижает твердость.
Наивысшей для двухкарбидных сплавов износостойкостью и допустимой скоростью резания при чистовой обработке обладает сплав Т30К4. Сплавы Т15К6, Т5К.Ю предназначены для получистовой и черновой обработки углеродистых и легированных сталей (поковок, штамповок, отливок). Сплав Т5К12В применяют для тяжелой черновой обработки поковок, штамповок и отливок, а также для строгания углеродистых и легированных сталей.
Сплавы третьей группы
применяют для черновой и чистовой обработки труднообрабатываемых материалов, в том числе жаропрочных сплавов и сталей. Добавка карбида тантала или ниобия оказывает положительное влияние на прочность и режущие свойства сплавов. К этой группе относятся следующие марки: ТТ7К.12, ТТ7К15, ТТ8К6, ТТ20К9 и др.
В связи с дефицитностью твердых сплавов на основе вольфрама применяют сплавы на основе карбидов ванадия, молибдена, хрома. Например, твердый сплав на основе карбида хрома имеет более высокую жаростойкость, чем сплавы ВК и ТК, и обладает хорошей износостойкостью. В последнее время начинают применять безвольфрамовые твердые сплавы группы TiC—Ni—Mo (монитикар), по своим свойствам превосходящие тита-новольфрамовые сплавы. Сплавы группы монитикар предназначены для обработки в условиях безударных нагрузок углеродистых сталей и сплавов. Выпускаются следующие марки сплавов: A3, Б2, БЗ, Б4, Б5, ВЗ, ГЗ и ДЗ (44,3% TiC, 37,4% Ni, 18,3% Mo), имеющие низкий коэффициент трения и высокую износостойкость.
Твердые сплавы получают прессованием порошков карбидов и кобальта в изделия необходимой формы и последующим спеканием при 1250…1450 СС в атмосфере водорода или в вакууме. Твердые сплавы чаще изготовляют в виде стандартных пластин различной формы для оснащения ими резцов, фрез, сверл и других режущих инструментов, а также различных матриц для прессования полуфабрикатов и волочения проволоки. Пластины в режущем инструменте крепят либо медным припоем, либо механическим способом.
Минералокерамические твердые сплавы изготовляют из дешевого и недефицитного материала — окиси алюминия. Минералокерамические твердые сплавы термокорунд и микролит (ЦМ-332) выпускают в виде пластинок. Минералокерамика обладает большой твердостью и красностойкостью, что позволяет использовать ее при высоких скоростях резания для чистовой и получистовой обработки чугуна, стали и других материалов. Однако минералокаремика имеет высокую хрупкость и низкие показатели механической прочности, что ограничивает область ее применения.
29.Твердые и сверхтвердые сплавы
Твердые сплавы и режущая керамика
Твердые сплавы и режущую керамику получают с помощью методов порошковой металлургии. Порошковая металлургия – область техники, охватывающая совокупность методов изготовления металлических порошков из металлоподобных соединений, полуфабрикатов и изделий из них, а также из их смесей с неметаллическими порошками без расплавления основного компонента. Исходные материалы для твердых сплавов и металлокерамики – порошки – получают химическими или механическими способами. Формообразование заготовок (изделий) осуществляют в холодном состоянии либо при нагревании. Холодное формообразование происходит при осевом прессовании на механических и гидравлических прессах или при давлении жидкости на эластичную оболочку, в которую помещают порошки (гидростатический метод). Горячим прессованием в штампах под молотом (динамическое прессование) или газостатическим методом в специальных контейнерах за счет давления (15—400 тыс. Па) горячих газов получают изделия из плохо спекающихся материалов – тугоплавких соединений, которые применяются для изготовления твердых сплавов и металлокерамики. В состав таких спеченных тугоплавких соединений (псевдосплавов) включаются неметаллические компоненты – графит, глинозем, карбиды, придающие им особые свойства.
В инструментальном производстве получили широкое распространение твердые спеченные сплавы и режущая металлокерамика (металлы + неметаллические компоненты) По содержанию основных компонентовпорошков в смеси твердые спеченные сплавы подразделяются на три группы вольфрамовые, титановольфрамовые и титанотанталоволь—фрамовые, по области применения– на сплавы для обработки материалов резанием, оснащения горного инструмента, для наплавки быстро изнашивающихся деталей машин, приборов и приспособлений.
Физико—механические свойства твердых сплавов:предел прочности при изгибе – 1176–2156 МПа (120–220 КГС/мм 2), плотность – 9,5—15,3 г/см 3, твердость – 79–92 HRA.
Твердые сплавы для бесстружковой обработки металлов, наплавки быстро изнашивающихся деталей машин, приборов и приспособлений: ВК3, ВК3–М, ВК4, ВК10–КС, ВК20–КС, ВК20К. В обозначении марок твердых сплавов буква «К» означает – кобальт, «В» – карбид вольфрама, «Т» – карбиды титана и тантала; цифры соответствуют процентному содержанию порошков компонентов, входящих в сплав. Например, сплав ВК3 содержит 3 % кобальта, остальное – карбид вольфрама.
Дефицит вольфрама обусловил необходимость разработки безвольфрамовых твердых сплавов, не уступающих по основным свойствам спеченным сплавам на основе карбидов вольфрама.
Безвольфрамовые и карбидохромовые твердые металлокера—мические сплавыприменяются в машиностроении для изготовления волок, вытяжных матриц, для распыления различных, в том числе абразивных, материалов, деталей трения, работающих при температурах до 900 °C, режущего инструмента для обработки цветных металлов.
Сверхтвердые материалы
Для изготовления различного режущего инструмента в настоящее время в различных отраслях промышленности, в том числе в машиностроительной, применяются три вида сверхтвердых материалов (СТМ): природные алмазы, поликристаллические синтетические алмазы и композиты на основе нитрита бора (эльбора).
Природные и синтетические алмазы обладают такими уникальными свойствами, как самая высокая твердость (HV 10 000 кгс/мм 2), у них весьма малые: коэффициент линейного расширения и коэффициент трения; высокие: теплопроводность, адгезионная стойкость и износостойкость. Недостатками алмазов являются невысокая прочность на изгиб, хрупкость и растворимость в железе при относительно низких температурах (+750 °C), что препятствует использованию их для обработки железоуглеродистых сталей и сплавов на высоких скоростях резания, а также при прерывистом резании и вибрациях.Природные алмазыиспользуются в виде кристаллов, закрепляемых в металлическом корпусе резца Синтетические алмазы марок АСБ (балас) и АСПК (карбонадо) сходны по своей структуре с природными алмазами Они имеют поликристаллическое строение и обладают более высокими прочностными характеристиками.
Природные и синтетические алмазыприменяются широко при обработке медных, алюминиевых и магниевых сплавов, благородных металлов (золота, серебра), титана и его сплавов, неметаллических материалов (пластмасс, текстолита, стеклотекстолита), а также твердых сплавов и керамики.
Синтетические алмазыпо сравнению с природными имеют ряд преимуществ, обусловленных их более высокими прочностными и динамическими характеристиками. Их можно использовать не только для точения, но также и для фрезерования.
Композитпредставляет собой сверхтвердый материал на основе кубического нитрида бора, применяемый для изготовления лезвийного режущего инструмента. По твердости композит приближается к алмазу, значительно превосходит его по теплостойкости, более инертен к черным металлам Это определяет главную область его применения – обработка закаленных сталей и чугунов. Промышленность выпускает следующие основные марки СТМ: композит 01 (эльбор – Р), композит 02 (белбор), композит 05 и 05И и композит 09 (ПТНБ – НК). 88–90), с подачей до 0,15 мм/об и глубиной резания 0,05—0,5 мм. Композиты 01 и 02 могут быть использованы также для фрезерования закаленных сталей и чугунов, несмотря на наличие ударных нагрузок, что объясняется более благоприятной динамикой фрезерной обработки. Композит 05 по твердости занимает среднее положение между композитом 01 и композитом 10, а его прочность примерно такая же, как и композита 01. Композиты 09 и 10 имеют примерно одинаковую прочность на изгиб (70—100 кгс/мм 2).
⇐ Предыдущая2Следующая ⇒
Рекомендуемые страницы:
Двухкарбидные твердые сплавы
Сплавы, содержащие карбиды вольфрама и титана, используют для инструментов, которыми обрабатывают материалы со сливной стружкой. У двухкарбидных сплавов стойкость к окислению, твердость и теплостойкость выше, чем у однокарбидных, но ниже упругость, теплопроводность и электропроводность. Устойчивость к усталостному разрушению у титановольфрамовых сплавов объясняется повышенной температурой схватывания при спекании. Эти сплавы используют при высоких скоростях резания стали.
Двухкарбидные сплавы обозначаются так: Т30К4, где число 30 указывает на процентное содержание карбида титана, а 4 – кобальта. Остальная часть сплава состоит из карбида вольфрама. Как и однокарбидных сплавах, предел прочности на сжатие и изгиб повышается с ростом содержания кобальта. Сплавы Т3ОК4 и Т15К6, используются в чистовой и получистовой обработке, а сплавы Т5К10 и Т5К12 подходят для медленной резки и работе с ударными нагрузками.
Область использования вольфрамсодержащих изделий
Применение сплава ВК8, как и другие схожие виды ТС, распространяется на разные отрасли производства, где требуется бурить скважины в абразивных горных породах, резать мрамор, заготавливать уголь, обрабатывать гранит. Также используются изделия из вольфрама в машиностроении для изготовления пар трения подшипников, штампов, пресс-форм.
На шарошках долот и на лапах устанавливаются специальные твердосплавные элементы (зубки) – одним из часто используемых сплавов и является ВК8
Уже сегодня этот вид металла нашел область применения – особо прочные покрытия, создаваемые технологией напыления. Наиболее известный сплав ВП3325 изготавливается на его основе, он улучшает свойства хрупких соединений такими качествами:
- теплопроводностью, твердостью;
- модулем упругости;
- ударной прочностью;
- устойчивостью к вибрации.
Пластины из сплава ВП3325
Между тем, такой вид обработки малопрочных материалов обретает все большую популярность и находит применение в медицине, оптике, ювелирной промышленности. Такой подход к приборостроению одновременно снижает себестоимость продукции, а также вольфрамовую потребность. Благодаря возможности использования вторсырья, некоторые даже зарубежные предприятия, обеспечиваются ресурсами без дополнительной их добычи из недр земли.
Трехкарбидные твердые сплавы
Добавление в твердые сплавы карбида тантала повышает твердость и прочность на изгиб в широком диапазоне температур. Это соединение увеличивает стойкость к повышенным температурам, окислению и усталостному разрушению при циклических нагрузках. Стандарт содержит четыре сплава — ТТ8К6, ТТ10К8Б, ТТ20К9, ТТ7К12 с содержанием карбида тантала от 2 до 12%.
Твердые сплавы с карбидом тантала используются для особо тяжелых режимов резания, при циклических нагрузках на инструмент. Сплав ТТ7К12 применяется для работы в наиболее неблагоприятных условиях – строгание, прерывистое точение, черновое фрезерование твердых и коррозионностойких сталей.
Применение ВК8
Твердый сплав ВК8 применяется для осуществления черновых работ:
- стачивания неоднородностей на сечениях среза;
- сверления отверстий;
- фрезеровочных работ;
- зенкерования серого чугуна.
С его помощью обрабатываются поверхности сталей всех видов: легированных, чугунных, жаростойких; твердых пород дерева.
Черновое точение при неравномерном сечении среза и прерывистом резании, строгание, черновое фрезерование, сверление, черновое рассверливание, черновое зенкерование серого чугуна, цветных металлов и их сплавов и неметаллических материалов.
Обработка коррозионно-стойких, высокопрочных и жаропрочных труднообрабатываемых сталей и сплавов, в том числе сплавов титана.
Сплав ВК8 ГОСТ 3882-74 установлен еще при СССР – (). При одинаковом процентном содержании вольфрама имеет физические свойства, существенно отличающиеся от аналогичного не лежащего в рамках конкретного ГОСТ.
ГОСТ 3882-74 с информацией о сплаве ВК8 и других марок твердого сплава – нажмите на картинку, чтобы посмотреть ГОСТ
Твердые сплавы без карбида вольфрама
Несмотря на достоинства вольфрама, он считается дорогим и дефицитным веществом. Поэтому ведутся исследовательские работы по созданию твердых сплавов без вольфрама или с минимальным его содержанием. Такие сплавы состоят из карбидов и карбидонитридов титана, а связкой выступает никель и молибден. Эти сплавы имеют хорошую твердость и стойкость к образованию окалины, но уступают по упругости у ударной вязкости. Их характеристики снижаются при повышенных температурах.
Твердые сплавы, не содержащие вольфрам, используют для чистовой и получистовой обработке. Ими обрабатывают углеродистые и легированные стали, титановые сплавы. Безвольфрамовые сплавы работают при средних и высоких скоростях резания.
Применение сплава Т15К6
Начнем, пожалуй, с самого простого. Первое, что вам следует понять, это то, что этот материал предназначен в основном для механической обработки сплавов и металлов. Чаще всего из него изготавливают резцовые плашки для токарных станков по металлу, реже – развертки для доводки выравнивания отверстий в заготовке, зенковки для снятия внутренних фасок тех же отверстий, фрезы для снятия определенного количества металла с поверхности заготовки, а также выборки углублений и формирования отверстий сложной формы. Последние три инструмента чаще всего используются для финальной, более деликатной обработки металлоизделия в то время, как резцами часто проводится грубая обработка детали, то есть придание основной формы.
Аналоги
Конечно же, выплавка стали и ее последующая обработка – явление, можно сказать, распространенное, а значит, и средства для той самой обработки должны быть распространены повсеместно и в больших количествах. И неудивительно, что среди такого множества имеется несколько сплавов, напоминающих наш Т15К6. Расшифровка аббревиатур будет, скорее всего, отличаться, так как система обозначения у каждой страны может разниться, но в целом состав сплавов близок или идентичен российскому аналогу.
Итак, список выглядит примерно так:
- Швеция – МС111;
- Польша – S10 и S10S;
- Германия – HS123, HT01 и HT02;
- Чехия – S1, T2.
Зная эти наименования, вы без труда сможете найти резец из необходимого вам сплава.
Структурно-фазовые состояния и механические свойства сплава ВК8 после гамма-квантового облучения
[1]
В.И. Третьяков, Основы металлов и технология изготовления спеченных твердых сплавов, Металлургия, Москва, (1976).
[2] Ю.М. Лахтин, В. Леонтьев, Материаловедение. Металлургия, Москва, (1980).
[3] ПРОТИВ. Панов, А. Чувилин, Технология и свойства спеченных сплавов и изделий из них.МИСиС, Москва, (2001).
[4]
В. Чернов, А. Мамонтов, А.Ботаки А. А. Аномальное воздействие малых доз ионизирующего излучения на металлы и сплавы. Атомная энергия, 57 (1984) 47-57.
[5] Ю.Тимошников А.А., Демиденко В.С., Кушнаренко В.М., Клопотов А.А. Влияние малых доз облучения на упорядоченный сплав Ni3Fe // Изв. Вузов. Физика, 3 (1993) 89-92.
[6]
А. Шалаев М. Радиационно-стимулированные процессы в металлах // Энергоатомиздат. Москва, (1988).
[7] Б.Конозенко А., Круликовская М. П., Данильченко Б. А. Структурные и фазовые изменения в металлах и сплавах, кристаллизованных в потоке гамма-квантов. Физика металлов и металлография, 161 (1991) 249-269.
[8]
С. Б. Кислицин, А.А. Клопотов, А. Потекаев, Ю.А. Тимошников. Влияние гамма-излучения на структурно-фазовые изменения в закаленной конструкционной стали // Изв. Вузов. Физика. 4 (2008) 74-83.
DOI: 10.1007 / s11182-008-9064-8
[9] Э.А. Борисова, Г. А. Бозвор и др., Металлография титановых сплавов, Металлургия. Москва, (1980).
[10]
К. Дж. Смитлз, Металлы. Справочник по металлургии, Москва (1980).
[11] Я.Малиенко А.А., Шиврин О.Н. // Изв. Вузов. Физика, 47 (1969) 7-13.
[12]
С. С. Горелик, Л. Расторгуев, Ю.А. Скаков, Рентгенографический и электронно-оптический анализ. Металлургия, Москва (1970).
[13] Н.Агеев В. Диаграммы состояния металлических систем. М .: ВИНИТИ, 1970.
Получение многослойных покрытий из газовой фазы с участием соединений TiC и TiN на твердом сплаве ВК8
Ворошнин Л.Г., Менделеева О.Л., Сметкин В.А., Теория и технология химико-термической обработки , М . : Новое знание, 2010.
Google ученый
Лоскутов В.Ф., Хижняк В.Г., Куницкий Ю.А., Киндрачук М.В. Диффузные карбидные покрытия , Киев, Техника, 1991.
Google ученый
Верещака А.С., Эффективность режущего инструмента с износостойкими покрытиями , М .: Машиностроение, 1993.
Google ученый
Лин Н.–М., Се Ф.–Г., Чжоу Дж., Чжун Т., Ву X – G., Тиан В. Микроструктура и износостойкость хромовых покрытий на стали P110. изготовить методом пакетной цементации, J. Cent. Южный технологический университет , 2010, т. 17, нет. 6. С. 1155–1162.
Артикул CAS Google ученый
Луо, Й., Ге, Ш., Джин, З., и Фишер, Дж., Формирование покрытия из карбида титана с микропористой структурой, Прил.Физ А .2010. 98. С. 765–768.
Артикул CAS Google ученый
Блинков И.В., Волхонский А.О., Аникин В.Н., Петраник М.И., Деревцова Д.Е. Фазовый состав и свойства износостойких покрытий Ti – Al – Cr – Zr – N – N производства метод физического осаждения из газовой фазы, Физика и химия обработки материалов , 2010, №1. 4. С. 37–43.
Google ученый
Chang, H.–W., Huang, P.K., Jeh, J.–W., Davison, A., Tsau, Ch.–H., and Yang, Ch. Ч., Влияние смещения подложки, температуры осаждения и отжига после осаждения на структуру и свойства многокомпонентных покрытий (Al, Cr, Mo, Si, Ti) N, Surf. Пальто. , 2008, вып. 202, стр. 3360–3366.
Артикул CAS Google ученый
Жуно-Силва, Дж., Ортисп-Доминкес, М., Кеддам, М., Этлиас-Эспиноса, М., Дамиан-Мехиа, О., Кардоса-Лагоретта, Э., Абруэ Обуйджано, М., Кинетика борирования слоев Fe2B, сформированных на стали AISI 1045, J. Min. Металл. Разд. Б, Металл. Б. , 2014, т. 50 (2), стр. 101–107.
Артикул Google ученый
Кампос-Сильва, И., Процесс борирования: кинетика роста и механические характеристики боридных слоев, JESTECH , 2012, т. 15 (2), стр. 53–61.
Google ученый
Хижняк В.Г., Калашников Г.Ю., Харченко Н.А., Говорун Т.П., Хижняк О.В., Долгых В.Ю., Голышевский О.О., Структура, состав и свойства азотированных сплавов после диффузной металлизации, Журнал нано- и электронной физики , 2015, т. 7, вып. 4, 04033 (6).
Google ученый
Дегула А.И., Говорун Т.П., Харченко Н.А., Хижняк В.Г., Карпец М.В., Мысливченко О.М., Степанин Р.С., Исследования фазового и химического состава сложных карбидных покрытий, Металлофизика и новейшие технологии , 2015, т. 37, нет. 11. С. 1461–1476.
CAS Google ученый

Boring, H.I. и Хинтерман, H.E., Дизайн с новыми материалами, JPAT Worckshop: износостойкое покрытие , Амстердам, 26–27 мая 1988 г., Эдинбург, стр. 85–106.
Google ученый
Бхат, Г., Вурмер, П., Покрытия для режущих инструментов, J. Metals , 1986, т. 38. С. 68–69.
CAS Google ученый
Йе, Дж. У., Чен, Й.-Л., Лин, С.-Дж., и Чен, С.-К., Высокоэнтропийные сплавы – новая эра эксплуатации, Матер. Sci. Форум , 2007, т. 560, стр. 1–9.
Артикул CAS Google ученый
Харченко, Н.А., Хыжяк В. Г., Сигова В. И., Супердисперсное и диффузное покрытие на сталях и твердых сплавах , Сумы: СОИППО, 2011.
Google ученый
Хижняк В.Г. Механизм формирования и некоторые характеристики двухкомпонентных карбидных покрытий на сталях и твердых сплавах // Металлургия и металлообработка , 1997, № 4, с. 2. С. 38–40.
Google ученый
Хижняк О.В., Курдыбайло П.А., Хижняк В.Г. Износостойкие многокомпонентные карбидные покрытия Ti, V, Cr на стали У10А и твердом сплаве Т15К6, Проблемы трения и износа. 2 (67), стр. 34–41.
Google ученый
Борисенок О.В., Васильев Л.А., Ворошнин Л.Г. Химико-термическая обработка металлов и сплавов , М .: Металлургия, 1981.
Google ученый
Кайдаш Н.Г., Структура и состав термостойких диффузных покрытий на стали . В кн .: Неорганические и силикатные покрытия. Ленинград, Наука, 1975. С. 184–189.
Google ученый
Коняшин И.Ю., Костяков В.И., Нарамовский И.В. Структура и свойства твердых сплавов после газового азотирования, Защитные покрытия на металлах , Киев: Наук. Думка, 1976, вып. 22, с. 69–73.
Google ученый
Хансен М., Андерко К., Структуры бинарных сплавов , Москва: Государственное научно-техническое издательство по черной и цветной металлургии, 1962.
Google ученый
Бондарь В.Т. Азотирование спеченных твердых сплавов // Порошковая металлургия , 1975, №2. 2. С. 38–43.
Google ученый
Ковальчук Т.Н., Шаповалов В.П., Горбунов Н.С., Применение титанонитридных покрытий для повышения стойкости твердосплавного инструмента, Защитные покрытия на металлах, , Киев: Наук. Думка, 1976, вып. 10. С. 107–108.
Google ученый
Оценка триботехнических характеристик и сигналов акустической эмиссии для пары трения из стали 30ХГСА и дюралюминия Д16, модифицированной сплавом ВК8
- О.А. Микосянчик
- В.
В. Токарук
- R.G. Мнацаканов
Ключевые слова: Акустическая эмиссия, износ, дюралюминий Д16, сплавы ВК8, электрораспылительное легирование, конструктивная адаптивность.
Аннотация
Применение метода акустической эмиссии для исследования процессов структурной приспособляемости при трении в условиях скольжения для трибосистемы из стали 30ХГСА и дюралюминия Д16, на поверхность которой методом электроскопического легирования нанесен сплав ВК8 с последующей обработкой поверхности. поверхностной пластической деформацией.Установлено формирование износостойких вторичных структур за счет увеличения интенсивности теплоотдачи в фрикционном контакте, что приводит к усилению механохимической активации поверхностных слоев металла. Модификация дюралюминия Д16 электрораспылением ВК8 обеспечивает снижение средней мощности акустической эмиссии в 2 раза на стадии приработки за счет снижения напряженно-деформированного состояния поверхностных слоев и снижения способности материала ВК8 поглощать механическая энергия при деформации. Установлена корреляционная зависимость общего массового износа пар трения и средней мощности акустической эмиссии
использованная литература
1. Фан Ю., Гу Ф., Болл А. Моделирование акустической эмиссии, создаваемой трением скольжения / Ю. Фан, Ф. Гу, А. Болл // Wear, 2010, Vol. 268, Ис. 5–6, С. 811-815.
2. Лингард С., Нг К.К. Исследование акустической эмиссии при трении скольжения и износе металлов / С.Лингард, К. Нг // Wear, 1989, Vol. 130, Ис. 2. С. 367-379.
3. Бенабдалла Х. С., Агилар Д. А. Акустическая эмиссия и ее взаимосвязь с трением и износом при скользящем контакте / Х. С. Бенабдаллах, Д. А. Агилар // Трибологические исследования. – 2008. – Т. 51, Ис. 6. С. 738-747.
4. Альюминиевые сплавы. В кн .: Aviacija: Jenciklopedija / Gl. красный. Г. П. Свищев. – М .: Науч. изд-во «Большая роза. jencikl. »: Центр. аджерогидродинам. institut im. Жуковского Н.Е., 1994, 736 с.
5. Александров В. Д. Поверхностное упрочнение алюминиевых сплавов / В. Д. Александров: дис. … Докт. техн. наук: 05.02.01 / Александров В.Д., Москва, 2002, 410 с.
6. Юрченко Е.В., Юрченко В.И., Дикусар А.И. Наноструктурирование поверхности из алюминиевых спла-вов в условиях электроискрового легирования / Е.В. Юрченко, В. Юрченко, А. Дикусар // Наноинженерия, 2013, № 2, стр. 12-24.
7. Альюминий и его сплавы: Учебное пособие / Сост. А.Р. Люк, А.А. Суслина. – Самара: Самар. гос. техн. ун-т, 2013, 81 с.
8. Упрочнение поверхностного слоя алюминиевого сплава АМг6 с помощью комбинированной елек-троискровой и ультразвуковой ударной обработки / Г.И. Прокопенко, Б.Н. Мордюк, В.Ф. Мазанко, Н.А. 35, № 10, рр. 1391–1406.
9. Стадниченко В.Н. Автоматизированная система трибодиагностики / В.Н. Стадниченко // Проблемы трети та зношування, 2006, № 46, рр.51-63.
10. Филоненко С.Ф., Стадниченко В.М. Определение контактных напряжений в узлах трения на основе метода акустической эмиссии / С.Ф. Филоненко, В.М. Соловьев. Стадниченко // Авиация, 2009, Том 13, № 3, стр. 72-77.
11. Экономичность триботехнических параметров сигнала акустической эмиссии для части 30ХГСА – D16 / V.V. Токарук, О. Мікосянчик, Р. Мначаканов, А.П. Кудрин // Проблемы трети та зношування, 2019, No 2 (83), стр. 19-28.
12. Поверхностная прочность материалов при тренировке / Б.Костецкий И. Носовский, А. Караулов и др. / под. общ. пед. d.t.n. Костецкий Б.И. – К .: Техника, 1976, 296 с.
Данные о влиянии градиента структуры, элементного и фазового состава нитридных многослойных покрытий на защиту от коррозии различных подложек в 3% -ном растворе NaCl и 5% -ном растворе NaOH
1.1. Характеристики процесса нанесения однослойных покрытий
Приведены материалы подложек, однослойных покрытий и способ их нанесения.Материал и способ нанесения подслоев и покрытий были выбраны одинаковыми. Представленные в статье данные иллюстрируют оптимизацию технологических параметров магнетронного распыления на постоянном токе (MS), катодно-дугового испарения (CAE), импульсного магнетронного распыления (PMS) и комбинированных методов (CAE + MS и CAE + PMS). К технологическим параметрам относятся ток дуги испарителя ( I arc ), мощность разряда магнетрона ( N ), напряжение смещения на подложке ( U смещение ), парциальное давление газовой смеси азота и азота. аргона ( P ), содержания азота в газовой смеси (N 2 ) и продолжительности нанесения покрытия ( T с ).Для установления фазового и элементного состава однослойных покрытий с максимальным защитным эффектом в растворах 5% NaOH и 3% NaCl изменены значения технологических параметров нанесения покрытий, приведенные в. Жирным шрифтом выделены оптимальные значения технологических параметров.
Таблица 1
Материал подложек, однослойных покрытий и способ их нанесения.
No покрытия | Подложка | Покрытие | Метод нанесения | ||||||||||||||||||||||||||||||||||||||||||||||||||||||||||||||||||||||||||||||||||||||||||||||||||||||||||||||||||||||||||||||||||||||||||||||||||||||||||||||||||||||||||||||||||||||||||||||||||||||||||||||||||||||||||||||||||||||||||||||||||||||||||||||||||||||||||||||||||||||||||||||||||||||||||||||||||||||||||||||||||||||||||||||||||||||||||||||||||||||||||||||||||||||||||||||||||||||||||||||||||||||||||||||||||||||||||||||||||||||||||||||||||||||||||||||||||||||||||||||||||||||||||||||||||||||||||||||||||||||||||||||||||||||||||||||||||||||||||||||||||||||||||||||||||||||||||||||||||||||||||||||||||||||||||||||||||||||||||||||||||||
---|---|---|---|---|---|---|---|---|---|---|---|---|---|---|---|---|---|---|---|---|---|---|---|---|---|---|---|---|---|---|---|---|---|---|---|---|---|---|---|---|---|---|---|---|---|---|---|---|---|---|---|---|---|---|---|---|---|---|---|---|---|---|---|---|---|---|---|---|---|---|---|---|---|---|---|---|---|---|---|---|---|---|---|---|---|---|---|---|---|---|---|---|---|---|---|---|---|---|---|---|---|---|---|---|---|---|---|---|---|---|---|---|---|---|---|---|---|---|---|---|---|---|---|---|---|---|---|---|---|---|---|---|---|---|---|---|---|---|---|---|---|---|---|---|---|---|---|---|---|---|---|---|---|---|---|---|---|---|---|---|---|---|---|---|---|---|---|---|---|---|---|---|---|---|---|---|---|---|---|---|---|---|---|---|---|---|---|---|---|---|---|---|---|---|---|---|---|---|---|---|---|---|---|---|---|---|---|---|---|---|---|---|---|---|---|---|---|---|---|---|---|---|---|---|---|---|---|---|---|---|---|---|---|---|---|---|---|---|---|---|---|---|---|---|---|---|---|---|---|---|---|---|---|---|---|---|---|---|---|---|---|---|---|---|---|---|---|---|---|---|---|---|---|---|---|---|---|---|---|---|---|---|---|---|---|---|---|---|---|---|---|---|---|---|---|---|---|---|---|---|---|---|---|---|---|---|---|---|---|---|---|---|---|---|---|---|---|---|---|---|---|---|---|---|---|---|---|---|---|---|---|---|---|---|---|---|---|---|---|---|---|---|---|---|---|---|---|---|---|---|---|---|---|---|---|---|---|---|---|---|---|---|---|---|---|---|---|---|---|---|---|---|---|---|---|---|---|---|---|---|---|---|---|---|---|---|---|---|---|---|---|---|---|---|---|---|---|---|---|---|---|---|---|---|---|---|---|---|---|---|---|---|---|---|---|---|---|---|---|---|---|---|---|---|---|---|---|---|---|---|---|---|---|---|---|---|---|---|---|---|---|---|---|---|---|---|---|---|---|---|---|---|---|---|---|---|---|---|---|---|---|---|---|---|---|---|---|---|---|---|---|---|---|---|---|---|---|---|---|---|---|---|---|---|---|---|---|---|---|---|---|---|---|---|---|---|---|---|---|---|---|---|---|---|---|---|---|---|---|---|---|---|---|---|---|---|---|---|---|---|---|---|---|---|---|---|---|---|---|---|---|---|---|---|---|---|---|---|---|---|---|---|---|---|---|---|---|---|---|---|---|---|---|---|---|---|---|---|---|---|---|---|---|---|---|---|---|---|---|---|---|---|---|---|---|---|---|---|---|---|---|---|---|---|---|---|---|---|---|---|---|---|---|---|---|---|---|---|---|---|---|---|---|---|---|---|---|---|---|---|---|---|---|---|---|---|---|---|---|---|---|---|---|---|---|---|---|---|---|---|---|---|---|---|---|---|---|---|---|---|---|---|---|---|---|---|---|
1 | HG30 | TiN | CAE | ||||||||||||||||||||||||||||||||||||||||||||||||||||||||||||||||||||||||||||||||||||||||||||||||||||||||||||||||||||||||||||||||||||||||||||||||||||||||||||||||||||||||||||||||||||||||||||||||||||||||||||||||||||||||||||||||||||||||||||||||||||||||||||||||||||||||||||||||||||||||||||||||||||||||||||||||||||||||||||||||||||||||||||||||||||||||||||||||||||||||||||||||||||||||||||||||||||||||||||||||||||||||||||||||||||||||||||||||||||||||||||||||||||||||||||||||||||||||||||||||||||||||||||||||||||||||||||||||||||||||||||||||||||||||||||||||||||||||||||||||||||||||||||||||||||||||||||||||||||||||||||||||||||||||||||||||||||||||||||||||||||
2 | MSCAE | 4 | MS | ||||||||||||||||||||||||||||||||||||||||||||||||||||||||||||||||||||||||||||||||||||||||||||||||||||||||||||||||||||||||||||||||||||||||||||||||||||||||||||||||||||||||||||||||||||||||||||||||||||||||||||||||||||||||||||||||||||||||||||||||||||||||||||||||||||||||||||||||||||||||||||||||||||||||||||||||||||||||||||||||||||||||||||||||||||||||||||||||||||||||||||||||||||||||||||||||||||||||||||||||||||||||||||||||||||||||||||||||||||||||||||||||||||||||||||||||||||||||||||||||||||||||||||||||||||||||||||||||||||||||||||||||||||||||||||||||||||||||||||||||||||||||||||||||||||||||||||||||||||||||||||||||||||||||||||||||||||||||||||||||||||
5 | (Ti, Zr) N | CAE | |||||||||||||||||||||||||||||||||||||||||||||||||||||||||||||||||||||||||||||||||||||||||||||||||||||||||||||||||||||||||||||||||||||||||||||||||||||||||||||||||||||||||||||||||||||||||||||||||||||||||||||||||||||||||||||||||||||||||||||||||||||||||||||||||||||||||||||||||||||||||||||||||||||||||||||||||||||||||||||||||||||||||||||||||||||||||||||||||||||||||||||||||||||||||||||||||||||||||||||||||||||||||||||||||||||||||||||||||||||||||||||||||||||||||||||||||||||||||||||||||||||||||||||||||||||||||||||||||||||||||||||||||||||||||||||||||||||||||||||||||||||||||||||||||||||||||||||||||||||||||||||||||||||||||||||||||||||||||||||||||||||
6 | MS | ||||||||||||||||||||||||||||||||||||||||||||||||||||||||||||||||||||||||||||||||||||||||||||||||||||||||||||||||||||||||||||||||||||||||||||||||||||||||||||||||||||||||||||||||||||||||||||||||||||||||||||||||||||||||||||||||||||||||||||||||||||||||||||||||||||||||||||||||||||||||||||||||||||||||||||||||||||||||||||||||||||||||||||||||||||||||||||||||||||||||||||||||||||||||||||||||||||||||||||||||||||||||||||||||||||||||||||||||||||||||||||||||||||||||||||||||||||||||||||||||||||||||||||||||||||||||||||||||||||||||||||||||||||||||||||||||||||||||||||||||||||||||||||||||||||||||||||||||||||||||||||||||||||||||||||||||||||||||||||||||||||||
7 | CAE + MS | 9029C 9029C (Ti, Al) N | PMS | ||||||||||||||||||||||||||||||||||||||||||||||||||||||||||||||||||||||||||||||||||||||||||||||||||||||||||||||||||||||||||||||||||||||||||||||||||||||||||||||||||||||||||||||||||||||||||||||||||||||||||||||||||||||||||||||||||||||||||||||||||||||||||||||||||||||||||||||||||||||||||||||||||||||||||||||||||||||||||||||||||||||||||||||||||||||||||||||||||||||||||||||||||||||||||||||||||||||||||||||||||||||||||||||||||||||||||||||||||||||||||||||||||||||||||||||||||||||||||||||||||||||||||||||||||||||||||||||||||||||||||||||||||||||||||||||||||||||||||||||||||||||||||||||||||||||||||||||||||||||||||||||||||||||||||||||||||||||||||||||||||||
9 | TiN | PMS | |||||||||||||||||||||||||||||||||||||||||||||||||||||||||||||||||||||||||||||||||||||||||||||||||||||||||||||||||||||||||||||||||||||||||||||||||||||||||||||||||||||||||||||||||||||||||||||||||||||||||||||||||||||||||||||||||||||||||||||||||||||||||||||||||||||||||||||||||||||||||||||||||||||||||||||||||||||||||||||||||||||||||||||||||||||||||||||||||||||||||||||||||||||||||||||||||||||||||||||||||||||||||||||||||||||||||||||||||||||||||||||||||||||||||||||||||||||||||||||||||||||||||||||||||||||||||||||||||||||||||||||||||||||||||||||||||||||||||||||||||||||||||||||||||||||||||||||||||||||||||||||||||||||||||||||||||||||||||||||||||||||
10 | USt 37-2 | (Ti, Zr, Al) N | CAE + MS | 9028
No покрытия | P , Па | I дуга , A | N , кВт | U смещение 2 , 9025 N | |||||||||||||||||||||||||||||||||||||||||
---|---|---|---|---|---|---|---|---|---|---|---|---|---|---|---|---|---|---|---|---|---|---|---|---|---|---|---|---|---|---|---|---|---|---|---|---|---|---|---|---|---|---|---|---|---|
Ti | Zr | Ti | Zr | Al | |||||||||||||||||||||||||||||||||||||||||
0 | 1.0 | – | 75 | – | 2.5 | – | 80, 200 | Ar | |||||||||||||||||||||||||||||||||||||
00 | 75 | – | 2,5 | – | – | ||||||||||||||||||||||||||||||||||||||||
000 | 75 | – | |||||||||||||||||||||||||||||||||||||||||||
1 | 0,8; 1,0 ; 1,2 | 80 | – | – | – | 80 | 40 | ||||||||||||||||||||||||||||||||||||||
2 | – | – | 2.![]() | – | – | 80, 150, 200 | 100 | ||||||||||||||||||||||||||||||||||||||
3 | 0,8; 1,0 ; 1,2 | – | – | 5,1; 5,5 ; 6,8 | – | 60 | 90 | ||||||||||||||||||||||||||||||||||||||
4 | – | 80 | – | – | – | 80 | 40 | – | 1.![]() | – | 200 | 100 | |||||||||||||||||||||||||||||||||
6 | 75 | 75 | – | – | – | 40, 60, 80 | |||||||||||||||||||||||||||||||||||||||
7 | – | – | 2,0 | 2,0 | 200 | 100 | |||||||||||||||||||||||||||||||||||||||
8 | 0,24; 0,26; 0,28 | 80 | – | 2.![]() | 2,0 | – | 40, 90 | 50 | |||||||||||||||||||||||||||||||||||||
9 | 0,28; 0,5 ; 0,8 | – | – | 7,0 , 9,0 | – | 7,0 | 50 , 55 | 12 , 19 | |||||||||||||||||||||||||||||||||||||
10 | – | 2,1 | 1,6 | 70 | 40 |
1.
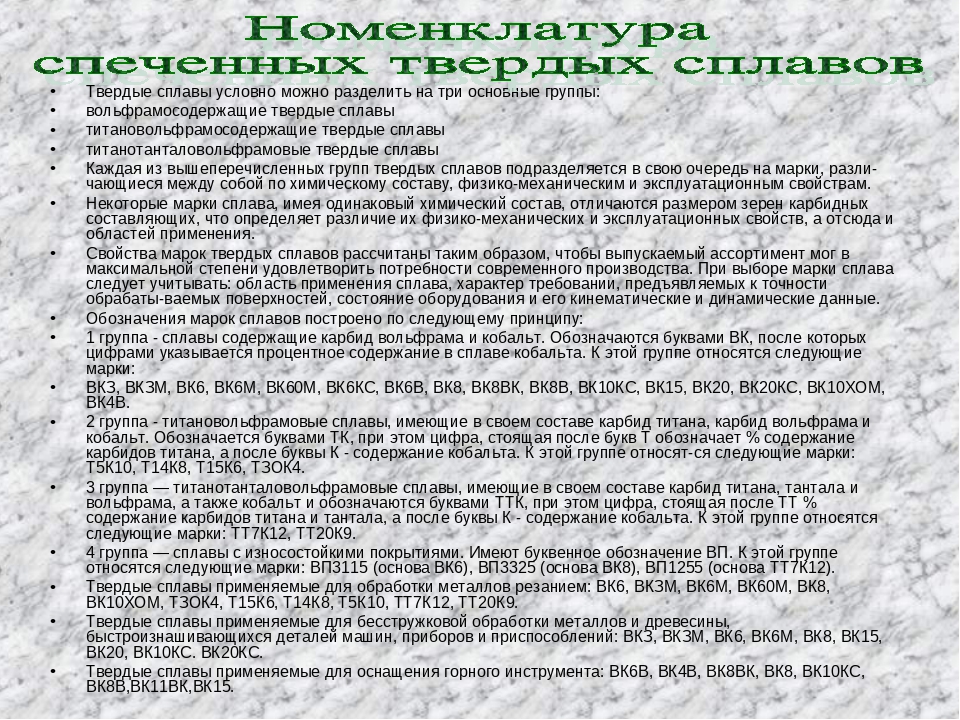
Данные фазового анализа построены в виде совмещенных фрагментов рентгеновской дифрактограммы покрытий, полученных при различных технологических параметрах. иллюстрирует фазовый состав однослойных покрытий из TiN и ZrN, полученных катодно-дуговым испарением при различном давлении газовой смеси. Фазовый состав покрытий 1–10 с максимальным объемным содержанием фаз c-TiN, c-ZrN, δ-Zr 3 N 4 , c-TiZrN 2 , h-Ti 3 Al 2 N 2 показаны в.Элементный состав определен только для покрытий, в которых проявляется фазовый состав. Средние значения элементного состава покрытий, определенные в трех различных спектрах, показаны на и.
Объединенные фрагменты рентгеновской дифрактограммы покрытий, полученных катодно-дуговым испарением при различных давлениях газовой смеси: TiN (а) и ZrN (б).
Таблица 3
Фазовый и элементный состав однослойных покрытий. Остальные фазы – AlN, TiN 0.3 , ZrN 0,28 , V Zr2N , Ti 2 AlN.
No покрытия | V – Объемное содержание фазы покрытия (%) | Содержание металла покрытия (ат.%) | |||||||||||||||||||||||||||||||||||||||||||||||||||||||||||||||||||||||||||||||||||||||||||||||||||||||||||||||||||||||||||||||||||||||||||||||||||||||||||||||||||||||||||||||||||||||||||||||||||||||||||||||||||||||||||||||||||||||||||||||||||||||||||||||||||||||||||||||||||||||||||||||||||||||||||||||||||||||||||||||||||||||||||||||||||||||||||||||||||||||
---|---|---|---|---|---|---|---|---|---|---|---|---|---|---|---|---|---|---|---|---|---|---|---|---|---|---|---|---|---|---|---|---|---|---|---|---|---|---|---|---|---|---|---|---|---|---|---|---|---|---|---|---|---|---|---|---|---|---|---|---|---|---|---|---|---|---|---|---|---|---|---|---|---|---|---|---|---|---|---|---|---|---|---|---|---|---|---|---|---|---|---|---|---|---|---|---|---|---|---|---|---|---|---|---|---|---|---|---|---|---|---|---|---|---|---|---|---|---|---|---|---|---|---|---|---|---|---|---|---|---|---|---|---|---|---|---|---|---|---|---|---|---|---|---|---|---|---|---|---|---|---|---|---|---|---|---|---|---|---|---|---|---|---|---|---|---|---|---|---|---|---|---|---|---|---|---|---|---|---|---|---|---|---|---|---|---|---|---|---|---|---|---|---|---|---|---|---|---|---|---|---|---|---|---|---|---|---|---|---|---|---|---|---|---|---|---|---|---|---|---|---|---|---|---|---|---|---|---|---|---|---|---|---|---|---|---|---|---|---|---|---|---|---|---|---|---|---|---|---|---|---|---|---|---|---|---|---|---|---|---|---|---|---|---|---|---|---|---|---|---|---|---|---|---|---|---|---|---|---|---|---|---|---|---|---|---|---|---|---|---|---|---|---|---|---|---|---|---|---|---|---|---|---|---|---|---|---|---|---|---|---|---|---|---|---|---|---|---|---|---|---|---|---|---|---|---|---|---|---|---|---|---|---|---|---|---|---|---|---|---|---|---|---|---|---|---|---|---|---|---|---|---|---|---|---|---|---|---|---|---|---|
TiN | ZrN | Zr 3 N 4 | TiZ | Ti 3 Al 2 N 2 | Другие фазы | Ti | Zr | Al | |||||||||||||||||||||||||||||||||||||||||||||||||||||||||||||||||||||||||||||||||||||||||||||||||||||||||||||||||||||||||||||||||||||||||||||||||||||||||||||||||||||||||||||||||||||||||||||||||||||||||||||||||||||||||||||||||||||||||||||||||||||||||||||||||||||||||||||||||||||||||||||||||||||||||||||||||||||||||||||||||||||||||||||||||||||||||||||||||
1 | 96.8 | – | – | – | – | 3,2 | 100 | – | – | ||||||||||||||||||||||||||||||||||||||||||||||||||||||||||||||||||||||||||||||||||||||||||||||||||||||||||||||||||||||||||||||||||||||||||||||||||||||||||||||||||||||||||||||||||||||||||||||||||||||||||||||||||||||||||||||||||||||||||||||||||||||||||||||||||||||||||||||||||||||||||||||||||||||||||||||||||||||||||||||||||||||||||||||||||||||||||||||||
2 | 99,2 | – | –0,8 | 100 | – | – | |||||||||||||||||||||||||||||||||||||||||||||||||||||||||||||||||||||||||||||||||||||||||||||||||||||||||||||||||||||||||||||||||||||||||||||||||||||||||||||||||||||||||||||||||||||||||||||||||||||||||||||||||||||||||||||||||||||||||||||||||||||||||||||||||||||||||||||||||||||||||||||||||||||||||||||||||||||||||||||||||||||||||||||||||||||||||||||||||||
3 | – | 91,7 | – | – | – | 8,3 | 100 – | 100 – | 100 – | – | 100 | – | – | – | – | – | 100 | – | |||||||||||||||||||||||||||||||||||||||||||||||||||||||||||||||||||||||||||||||||||||||||||||||||||||||||||||||||||||||||||||||||||||||||||||||||||||||||||||||||||||||||||||||||||||||||||||||||||||||||||||||||||||||||||||||||||||||||||||||||||||||||||||||||||||||||||||||||||||||||||||||||||||||||||||||||||||||||||||||||||||||||||||||||||||||
5 | 99.![]() | – | 0,6 | 0,4 | – | – | 84,9 | 15,1 | – | ||||||||||||||||||||||||||||||||||||||||||||||||||||||||||||||||||||||||||||||||||||||||||||||||||||||||||||||||||||||||||||||||||||||||||||||||||||||||||||||||||||||||||||||||||||||||||||||||||||||||||||||||||||||||||||||||||||||||||||||||||||||||||||||||||||||||||||||||||||||||||||||||||||||||||||||||||||||||||||||||||||||||||||||||||||||||||||||||
6 | 15,1 | – | 13,4 71 27,3 | 72,7 | – | ||||||||||||||||||||||||||||||||||||||||||||||||||||||||||||||||||||||||||||||||||||||||||||||||||||||||||||||||||||||||||||||||||||||||||||||||||||||||||||||||||||||||||||||||||||||||||||||||||||||||||||||||||||||||||||||||||||||||||||||||||||||||||||||||||||||||||||||||||||||||||||||||||||||||||||||||||||||||||||||||||||||||||||||||||||||||||||||||||||
7 | 18,4 | – | 51,6 | 30,0 | – | – | 69,1 | 30,9 – | 30,9 – | 0 | – | – | – | 86,0 | 4,0 | 53,1 | – | 45,7 | |||||||||||||||||||||||||||||||||||||||||||||||||||||||||||||||||||||||||||||||||||||||||||||||||||||||||||||||||||||||||||||||||||||||||||||||||||||||||||||||||||||||||||||||||||||||||||||||||||||||||||||||||||||||||||||||||||||||||||||||||||||||||||||||||||||||||||||||||||||||||||||||||||||||||||||||||||||||||||||||||||||||||||||||||||||||
9 | 84,5 | – | 100 | – | – | ||||||||||||||||||||||||||||||||||||||||||||||||||||||||||||||||||||||||||||||||||||||||||||||||||||||||||||||||||||||||||||||||||||||||||||||||||||||||||||||||||||||||||||||||||||||||||||||||||||||||||||||||||||||||||||||||||||||||||||||||||||||||||||||||||||||||||||||||||||||||||||||||||||||||||||||||||||||||||||||||||||||||||||||||||||||||||||||||||||
10 | 13,8 | – | 57,6 | – | 28,6 | 38,0 | 53000 | 38,0 | : TiN (а) и ZrN (б).1.3. Оптимизация коррозионных свойств по фазовому и элементному составу, структуре, размеру зерна и толщине однослойных нитридных покрытийМетод нанесения покрытия оптимизирован на основе данных о коррозионных свойствах (). Коррозионные свойства подложки и однослойных покрытий с оптимальным фазовым и элементным составом представлены в. Здесь E corr – потенциал коррозии, R p – сопротивление поляризации, i corr – плотность тока коррозии, i p – плотность пассивного тока; индексы s и c обозначают подложку и покрытие соответственно.Покрытия на основе фаз c-TiN и c-ZrN обладают максимальной эффективностью защиты. Данные по оптимизации объемно-металлоемкости, крупности и толщины этих покрытий представлены в. Наибольшее значение Rp, icorr, s / icorr.c и ip, s / ip, c всегда соответствует минимальному размеру зерна, максимальному объемному содержанию фаз c-ZrN и c-TiN, оптимальной толщине и составу, близкому к стехиометрическому. (). Таблица 4Коррозионные свойства подложки и однослойного покрытия.
Зависимость эффективности покрытия в 5% NaOH и 3% NaCl от фазового и элементного состава однослойных покрытий ZrN CAE (а), TiN CAE (б), TiN PMS (в). Стехиометрическое наноструктурированное покрытие ZrN с максимальным объемным содержанием фазы c-ZrN и концентрацией циркония, оптимальной толщиной 5,5 мкм и размером зерна 20… 70 нм замедляет коррозию в 5% NaOH более чем в 3000 раз, а пассивный ток – в 2000 раз (а). Увеличение фазового объема h-ZrN 0,28 до 8% снижает отношения i corr, s / i corr, c и i p, s / i p, c до 208 и 240 раз соответственно. Оптимальный фазовый состав покрытия TiN: V c-TiN = 99,2% и V h-TiN0.3 = 0,8%, оптимальная толщина 5 мкм, размер зерна ∼20… 35 нм . Отношение i corr, s / i corr, c для этого покрытия больше 650, а отношение i p, s / i p, c равно 640 .При увеличении содержания фазы h-TiN 0,3 отношения i corr, s / i corr, c и i p, s / i p, c уменьшаются. до 20 и 360 соответственно (б). По значениям соотношений i corr, s / i corr, c и i p, s / i p, c , однослойное покрытие TiN, нанесенное методом PMS имеет лучшую коррозионную стойкость в 3% NaCl. Это покрытие на подложке HG30 с предпочтительной ориентацией кристаллов (111), толщиной более 1 мкм, объемным содержанием фаз V c-TiN = 84,5% и V h-TiN0,3 = 15,5%, а минимальный размер зерна ∼20 нм показывает более высокую склонность к анодной пассивации в 3% NaCl и наиболее эффективно замедляет процесс коррозии.Коэффициенты, характеризующие эффективность защиты покрытия: i corr, s / i corr.c ≈ 2500, i p, s / i p, c = 2500. Наноструктурированный плотнее покрытия, нанесенные методом PMS, менее чувствительны к толщине покрытия и концентрации фазы с низким содержанием азота h-TiN 0,3 (c). Картина излома однослойного покрытия и морфология его поверхности, полученные с помощью автоэмиссионного электронного микроскопа Ultra 55, показаны на рисунке а. Наноструктурированные покрытия на твердом сплаве HG30: однослойные (а), многослойные (б). 1,4. Коррозионное поведение многослойных покрытий с чередованием слоев и градиентной структурой, фазовым и элементным составомМногослойные покрытия () разработаны на основе однослойных наноструктурированных нитридов ZrN, TiN и (Ti, Zr) N с максимальным защитным эффектом в 5% NaOH и 3% NaCl. В частности, в качестве чередующихся слоев для многослойных покрытий No.11 и № 12. Методы нанесения слоев для этих покрытий были изменены, чтобы получить их с различной структурой, фазовым и элементным составом. Фазовый и элементный состав многослойных покрытий, их коррозионные свойства приведены в. Слои многослойных покрытий наносились при оптимальных значениях параметров процесса. Толщина слоев составляла от 100 нм до 500 нм, а общая толщина многослойного покрытия составляла от 0,5 до 5,0 мкм. Таблица 5Лакокрасочные материалы и методы нанесения (материал подложки – HG30, подслой – TiN).
Таблица 6Потенциалы коррозии, устойчивость к коррозии и поляризационная стойкость плотность тока.соотношения для многослойных покрытий. Покрытия 11, 13–15 испытывались в 5% NaOH, покрытие 12 – в 0,3% NaCl.
На основе значений E i corr, s / i corr, c и i p, s / i p, c , многослойные покрытия TiN – ZrN (№11 и № 12) обладают высокой коррозионной стойкостью как в 5% NaOH, так и в 3% NaCl. Эффект ингибирования коррозии i corr, s / i corr, c и степень пассивации поверхности i p, s / i p, c для этих покрытий в 5% NaOH составляют 750 и 800, а в 3% NaCl – 136 и 229 соответственно. Картина излома многослойных покрытий, полученных с помощью автоэмиссионного электронного микроскопа Ultra 55, показана на б. Морфология поверхности твердого сплава HG30 перед электрохимическими испытаниями показана на a. Морфология поверхности твердого сплава HG30 после электрохимических испытаний в 5% растворе NaOH показана на b-d. После 5 минут травления в 5% растворе NaOH кобальтовая связка слегка протравливается, обнажаются границы зерен карбида вольфрама и выявляются кристаллографические ямки травления, самые большие из которых имеют диаметр не более 1,5 мкм (б) . После анодного растворения в 5% растворе NaOH на поверхности ВК8 практически исчезает кристаллографическая огранка зерен и наблюдаются темные протравленные участки, занимающие значительную часть поверхности исследуемого образца (в).После анодного растворения в 5% растворе NaOH наблюдаются участки золотого многослойного покрытия. Кристаллографических ямок не наблюдалось (г). Поляризационные кривые сплава HG30 в 5% -ном растворе NaOH приведены при. Скорость растворения при потенциале −0,2 В снижается в ∼18 раз. Морфология поверхности твердого сплава HG30 до электрохимических испытаний (а), HG30 после травления в 5% растворе NaOH (б), HG30 после анодной поляризации в 5% растворе NaOH (в), HG30 с многослойным покрытием TiN – ZrN после анодной поляризации 5% -ного раствора NaOH (г). Анодные поляризационные кривые в 3% растворе NaCl: 1 – твердый сплав HG30 без покрытия, 2 – HG30 с многослойным покрытием TiN – ZrN. GN 115 Защелки из нержавеющей стали, работа с торцевым ключомОпции деталей / ТаблицаТип
Комбинация фильтров не дает результата. Метрическая
Комбинация фильтров не дает результата. постройки и ценаКонфигуратор продуктов 3D Тип Расстояние фиксации A Материал Тип Расстояние фиксации A МатериалИзбранная частьномер части Всего долларов США (нетто) 33 доллара США.29 Звоните / Электронная почта, чтобы узнать время доставкиКоличество Обратите внимание на наши оптовые скидки (в долларах США).
Prop 65: Не соответствует RoHS: Соответствует Эта статья соответствует требованиям RoHS в применении Приложения III, что означает, что она соответствует Директиве ЕС 2011/65 / EU, включая расширение (2015/863 / ЕС) для ограничения использования определенных опасных веществ в электрических и электронных устройствах. Директива регулирует использование опасных веществ в устройствах и компонентах. Реализация в национальном законодательстве вкратце описывается в RoHS ( R estriction o f (использование определенных) h azardous s ubstances)). Вес: 0,176 фунта Если вес не указан, пожалуйста, свяжитесь с нашим отделом продаж для получения дополнительной информации о весе. Все цены указаны в долларах США. Налоги не включены. CAD СкачатьДанные CADДругие форматы данных – Выбор формата данных САПР -PART2cad Creo Elements / Прямое моделирование (PART2cad Inventor PART2cad Solid Edge PART2cad SolidWorks PART2cad Unigraphics NX glTF (GLB) USDZ 3D Studio MAX AutoCAD> = V14Catia (Macro)> = V5Catia> = V5Catia IUA V4Creo Elements / Direct Modeling > = 17.0Creo Parametric 2Creo Parametric 4Creo Parametric 5DWG AUTOCAD VERSION 2004-2006 VERSION DWG AUTOCAD 2007-2009DWG AUTOCAD VERSION 2010-2012DWG AUTOCAD VERSION 2013IGES Inventor 2017Inventor 2018Inventor 2020Inventor 2021s Inventor 2017Inventor 2018Inventor 2020Inventor 2021sMechanical Desktop Mode PDF-файл SAT 7.0Solid Edge 2019Solid Edge 2020Solid Edge ST10Solid Edge ST8Solid Edge ST9SolidWorks (Macro)> = 2001 + SolidWorks> = 2006STEP AP203STEP AP214STL BMP (2D View) DWG AUTOCAD VERSION 2007 – 2009DWG AUTOCAD VERSION 2010 – 2012DWG AUTOCAD VERSION 2010 – 2012DWG – 2006DXF AUTOCAD VERSION 2010 – 2012DXF AUTOCAD VERSION 2013SVG TIFF (2D View) Учебное пособие по загрузке САПРО загрузках САПР GN 115-DK-24-NIGN 115-DK-28-NIGN 115-VK7-24-NIGN 115-DK-20-NIGN 115-VK7-6-NIGN 115-VDE-20-NIGN 115-SCH-34-NIGN 115-VK7-38-NIGN 115-VK7-10-NIGN 115-DK-6-NIGN 115-DK-18-NIGN 115-SCH-18-NIGN 115-VK7-28-NIGN 115-VDE-26-NIGN 115 -DK-40-NIGN 115-SCH-14-NIGN 115-VK8-24-NIGN 115-SCH-50-NIGN 115-DK-50-NIGN 115-VK8-28-NIGN 115-VDE-10-NIGN 115- DK-14-NIGN 115-VDE-14-NIGN 115-VK7-50-NIGN 115-VK8-38-NIGN 115-VK7-18-NIGN 115-VDE-28-NIGN 115-SCH-40-NIGN 115-VDE -18-NIGN 115-VDE-30-NIGN 115-VK8-14-NIGN 115-VK7-40-NIGN 115-DK-30-NIGN 115-VK8-20-NIGN 115-VK8-10-NIGN 115-VK8- 22-NIGN 115-SCH-6-NIGN 115-VK8-18-NIGN 115-VDE-24-NIGN 115-VK7-14-NIGN 115-DK-34-NIGN 115-VK7-26-NIGN 115-DK-26 -NIGN 115-VK8-26-NIGN 115-VDE-50-NIGN 115-DK-10-NIGN 115-SCH-26-NIGN 115-SCH-10-NIGN 115-DK-38-NIGN 115-VDE-34- NIGN 115-VK8-50-NIGN 115-SCH-30-NIGN 115-VDE-6-NIGN 115-SCH-24-NIGN 115-SCH-28-NIGN 115-VDE-38-NIGN 115-VDE-22-NIGN 115-SCH-20-NIGN 115-SCH-22-NIGN 115-VK7-30-NIGN 115-VK7-34-NIGN 115-VK7-22-NIGN 115-VDE-40-NIGN 115-VK 8-30-NIGN 115-VK8-34-NIGN 115-VK8-6-NIGN 115-SCH-38-NIGN 115-DK-22-NIGN 115-VK7-20-NIGN 115-VK8-40-NI % PDF-1.4 % 1 0 объект > / OCGs [6 0 R 7 0 R] >> / Тип / Каталог / AcroForm 8 0 R / Метаданные 9 0 R / Страницы 10 0 R >> эндобдж 11 0 объект ) / ModDate (D: 20160721111741 + 01’00 ‘) / Автор (ПОЛЬЗОВАТЕЛЬ) / CreationDate (D: 20160701104656 + 07’00 ‘) >> эндобдж 2 0 obj > эндобдж 3 0 obj > эндобдж 4 0 объект > эндобдж 5 0 объект > эндобдж 6 0 объект > / Просмотр> / PageElement> / Печать> >> / Тип / OCG / Имя (Водяной знак) >> эндобдж 7 0 объект > >> / Тип / OCG / Имя (верхние / нижние колонтитулы) >> эндобдж 8 0 объект > / Шрифт> >> / DA (/ Helv 0 Tf 0 г) >> эндобдж 9 0 объект > транслировать application / pdf Повышение качества шероховатости поверхности листа из нержавеющей стали 420 с использованием метода магнитно-абразивной обработкииспользованная литература [1] С.С. Джейсвал, В.К. Джайн и П. Диксит, «Моделирование процесса магнитно-абразивной чистовой обработки», Международный журнал передовых производственных технологий, Vol.26 (2005), стр. 477–490. |