Токарная обработка металла: технология, виды, методы, видео
На протяжении многих десятилетий проводится токарная обработка металла и за столь длительный срок, как технология обработки, так и виды станков значительно изменились. Несмотря на это, общие черты, которые свойственны токарным станкам по металлу, сохранились.
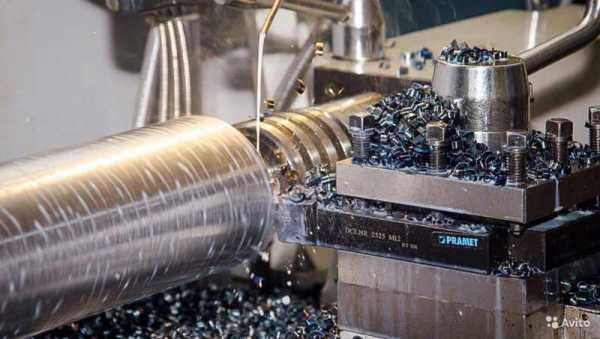
Особенности процесса
Токарная обработка металла проходит следующим образом:
- установленные в шпиндель заготовки вращаются вокруг своей оси;
- точение проводится путем подвода резца. подобные инструменты имеют различную форму, могут быть изготовлены из инструментальной стали или иметь твердосплавные режущие кромки;
- точение происходит путем создания поперечного усилия суппортом, в котором закреплены резцы: из-за большой силы трения и разного показателя твердости, которой обладают резцы и заготовка, происходит снятие с поверхности металла обрабатываемой заготовки;
- технология, по которое проводится точение, может быть самой разной: совмещение продольной и поперечное подачи или использование только одной.
Учитывая то, как происходит резание на токарном станке по металлу, все они имеют схожую конструкцию.
Особенности токарных станков по металлу
Способ придания необходимых размеров и формы заготовке определяет также особенности станков токарной группы. Несмотря на то, что разные виды станков отличаются между собой, можно выделить несколько схожих признаков, которые свойственные всей токарной группе:
- обработки поверхности проводится резанием. инструменты, которые используются в большинстве случаев – резцы, виды которых зависят от многих показателей;
- имеется шпиндель с кулачковым патроном, в котором закрепляются заготовки. основное движение – вращательное, передается шпинделю;
- резцы закрепляют в суппорте, которому предается возвратно-поступательное движение. особенности конструкции суппорта позволяют использовать разные методы обработки поверхности;
- крепление изделия в некоторых случаях может проводиться по двум сторонам, для чего используют заднюю бабку;
- станок токарного типа можно использовать для растачивания отверстий, которые расположены вдоль оси изделия;
- скорость и подача, при которых проводится резание, могут устанавливаться в зависимости от типа поверхности заготовки, необходимых показателей точности снятия металла и шероховатости получаемой поверхности. для этого конструкция токарных станков имеет сложную схему передач.
Резание на токарных станках выполняется только при условии использования средств индивидуальной защиты, а также при установке защитного экрана.
Виды токарных станков
В зависимости от того, какие изделия нужно получить с какой точностью, можно выделить следующие группы токарных станков:
- токарно-винторезные – наиболее распространенная группа. при использовании токарных станков из этой группы можно получить цилиндрические поверхности различного диаметра. есть возможность придать заготовки конусность, нарезать на поверхности резьбу. можно проводить обработку черных и цветных металлов;
- токарно-карусельные – используются для получения изделия большого диаметра. также применяется для обработки цветных и черных металлов;
- лоботокарная группа отличается тем, что заготовки устанавливаются по горизонтали и есть возможность получения конической или цилиндрической поверхности;
- токарно-револьверная группа используется для обработки заготовки, которая представлена калиброванным прудком.
Существуют и другие, узкоспециализированные виды станков, которые условно относят к токарной группе из-за особенностей резания, когда используются резцы.
Внедрение ЧПУ
Существенным прорывом в области станкостроения стало использование системы Числового Программного Управления. Изделия с появление системы ЧПУ стало можно получить с меньшими затратами, чистота обработки, как и точность находятся на самом высоком уровне.
Наличие системы ЧПУ определяет следующее:
- повышение показателя производительности при условии, когда резцы используются с твердосплавной режущей кромкой;
- обработка возможна как черных и цветных, так и инструментальных сплавов при соответствующей оснастке;
- вмешательство мастера в процесс минимальное. резание происходит в автоматическом режиме;
- система ЧПУ позволяет указать все режимы резания. программа для ЧПУ составляется с указанием скорости, при которой проводится резание, а также подачи;
- зачастую вся зона, в которой происходит резание, закрыта защитным кожухом, так как система ЧПУ не позволит начать работу без защиты окружающих;
- высокая точность работы ЧПУ, которая получается резанием с правильным указанием скорости, позволяет получать детали с меньшим показателем брака для ответственных элементов различных конструкций.
Система ЧПУ широко используется при производстве токарных станков в Китае и США. Возможность внедрения ЧПУ определяется точность позиционирования элементов конструкции станка.
Режимы работы
Важным показателем можно назвать то, какой режим обработки используется. К основным показателям можно отнести:
- Скорость вращения шпинделя, в котором закрепляют заготовки. Скорость устанавливается исходя из того, какое резание проводится: чистовое или черновое. Скорость чернового резания меньше, чем скорость чистового резания. Это связано с взаимосвязью: чем больше скорость вращения шпинделя, тем меньше подача. В противном случае возникает ситуация, когда резцы деформируются или начинает «гореть» металл. Чрезмерная нагрузка оказывает плохое влияние на состояние станка.
- Подача выбирается с учетом скорости. При черновой обработке она больше, что ускоряет процесс снятия большей части металла, при чистовой – меньше, что необходимо для достижения необходимой точности.
В зависимости от режима обработки также выбираются резцы. Их виды зависят от формы режущей кромки, головки и стержня.
Точение заготовок из металла путем использования станков токарной группы – наиболее популярный метод обработки, несмотря на появление современного лазерного и другого оборудования. Столь высокая популярность связана с надежность станков и их относительно небольшой стоимость, долгим сроком службы. Некоторые модели из токарно-винторезной группы служат на протяжении нескольких десятилетий при надлежащем уходе и периодическом ремонте.
Если вы нашли ошибку, пожалуйста, выделите фрагмент текста и нажмите Ctrl+Enter.
stankiexpert.ru
Точение для получения идеально ровной поверхности детали + видео
Чтобы получить из металлической болванки черновую заготовку, а затем и необходимую деталь, используется такой тип обработки, как точение, наряду с некоторыми другими видами токарных операций.
1 Что такое точение – черновое и чистовое
Деревянные резные балясины, ножки столиков и стульев, металлические детали в узлах механизмов – все эти изделия сложной формы почти наверняка были изготовлены на токарном станке. Конечно, многие виды продукции из стали и других сплавов можно получить литьем, ковкой, штамповкой и фрезерованием, однако в большинстве случаев нужный результат обеспечивают при помощи простейшей операции, а именно – точения. Так называют любой вид обработки внешней торцевой или вращающейся поверхности посредством воздействия на нее лезвием резца. Применение режущего инструмента для внутренних поверхностей осуществляется в процессе растачивания.
Рекомендуем ознакомиться
Операции точения возможны только при вращении детали, закрепленной в кулачковом или цанговом механизме фиксирующего патрона и при значительной длине прижатой центром задней бабки
Черновое точение отличается от тонкого чистового силой воздействия лезвия резца на торцевую или цилиндрическую поверхность, а также скоростью вращения детали, что в итоге дает очень малое сечение образующейся стружки. Иными словами, обтачивание применяется для удаления мельчайших шероховатостей, а точение – для придания необходимой формы металлической или деревянной заготовке. При этом тонкая обработка осуществляется с минимальной глубиной погружения резца: до 0,3 миллиметра при первых проходах и до 0,05 миллиметров при завершающих.
2 Как происходит растачивание отверстий?
В токарных работах используется огромное количество разнообразных резцов, ряд которых необходим для расточных операций. При этом выбор инструмента для черновых проходов зависит от того, сквозное отверстие нужно обрабатывать или глухое. Отдельные резцы применяются для чистового растачивания, независимо от типа отверстия. Рассматриваемый вид токарной обработки деревянной или металлической заготовки осуществляется при закреплении последней в кулачковом патроне, без упора в центр задней бабки. Инструмент, зажатый в держателе, располагается по оси вращения заготовки, ею выполняют поступательное движение с постепенным отклонением от центра.
Как правило, растачивание отверстий осуществляется после сверления, однако в некоторых случаях необходимо произвести внутреннюю обработку канавок или пазов, сделанных на фрезерном станке. Каждый раз при этом происходит увеличение диаметра по всей глубине отверстия или на определенном его отрезке. Первый тип работ осуществляется проходным инструментом, а второй вариант имеет место при необходимости вытачивания внутренней канавки с помощью прорезного лезвия. Также с помощью расточного инструмента может быть выполнена обработка внутреннего торца глухого углубления, для чего используются подрезной резец.
Все инструменты, использующиеся при растачивании, имеют меньшую жесткость, чем резцы для наружных операций, вследствие чего скорость вращения детали следует понижать на 10-20 % в сравнении с внешними токарными работами. Также при обработке углублений существуют и другие подводные камни, требующие удвоенного внимания. В частности, очень трудно наблюдать за протеканием процесса, так как стружка снимается внутри отверстия. Еще одна сложность – необходимость выдвигать резец из держателя несколько дальше, чем требует глубина глухого отверстия, из-за чего обработка удаленных отрезков внутренней стенки может быть нарушена пружинящим инструментом.
3 Подрезание металла – поэтапный обзор операции
Выше уже упоминался специальный подрезной инструмент для токарных работ, необходимый для обработки торцевых поверхностей, а также уступов, как внешних, так и внутренних, расположенных в углублении. Перечисленные операции выполняются движением резца вдоль оси вращения, от центра к краю торца. Лезвие подрезного инструмента обычно имеет две заточенные кромки: длинную, которая располагается под небольшим углом к обрабатываемой поверхности, и короткую, отклоненную на 15-20 градусов от оси вращения заготовки.
Однако помимо вышеназванного резца существуют и другие, например, упорный и отогнутый, причем второй бывает проходным. Заточка обоих вариантов несколько отличается от описанной ранее. Упорный тип удобен тем, что им можно выполнять операции с продольной и поперечной подачей. В тех же случаях, когда подрезание выполняется в непосредственной близости от патрона, а также при обработке труднодоступных уступов в отверстиях, возникает необходимость в отогнутых резцах, в том числе и проходных. Последними обычно работают с поперечной подачей.
Примечательно, что все операции на торцах можно выполнять не только зажатием в кулачках, но и при фиксации заготовки с упором в центр задней бабки. Правда, в этом случае рекомендуется применять так называемый “полуцентр”, на треть толщины которого по всей длине отсутствует сегмент. Таким образом, обеспечивается возможность обрабатывать весь торец от края к центру подрезным лезвием. При работе с торцом зажатой в патроне детали лучше действовать проходным отогнутым инструментом.
4 Тонкое обтачивание различных поверхностей
Процесс обтачивания, по сути, является аналогом тонкого чистового точения, о котором говорилось выше. Выполняется эта операция при высокой частоте вращения заготовки, от 1500 до 2000 оборотов в минуту. При этом подача резца выполняется на шаг, не превышающий 0,6 ширины режущей кромки на один оборот детали. Следует отметить, что лезвие инструмента обычно применяется широкое, располагается оно параллельно обрабатываемой поверхности. При минимальной глубине резания после обтачивания не требуется шлифование металла, поскольку все шероховатости снимаются при чистовых проходах.
Режущая кромка инструмента должна обладать высокой прочностью, лезвия выполняются из твердых сплавов, а также снабжаются алмазными и эльборовыми вставками.
Как правило, операции обтачивания применяются для цветных металлов, а также их сплавов, значительно реже им подвергаются заготовки из стали и чугуна. Скорости вращения для каждого вида металла выбираются разные. В частности, для чугуна необходима скорость 100-150 метров в минуту, стальные детали обтачиваются при частоте оборотов 150-250 метров в минуту, а цветные металлы и их сплавы обрабатываются при вращении кулачкового патрона от 1000 метров в минуту.
tutmet.ru
Московский Государственный Университет
Приборостроения и Информатики
Кафедра Технологической информатики
Контрольная работа “Точение цилиндрической поверхности на проход” по дисциплине:
«Физические основы резания материалов»
Вариант 5
Выполнила:
Медведева Светлана Игоревна
ТИ-1 2 курс 151900
Принял: доцент Владимир Александрович Панайоти
__________________
Дата:
Москва, 2013
Содержание:
Реферат на тему: «Точение»
Расчет режимов резания
Список литературы
Реферат на тему: «Точение»
Сущность метода обработки точением.
Токарная обработка— один из возможных способов обработки изделий путем срезания с заготовки лишнего слоя металла до получения детали требуемой формы, размеров и шероховатости поверхности. Она осуществляется на металлорежущих станках, называемых токарными. На токарных станках обрабатываются детали типа тел вращения: валы, зубчатые колеса, шкивы, втулки, кольца, муфты, гайки и т.д.
Точение является одним из основных видов обработки металла резанием. Точение применяют, чтобы получить детали, представляющие собою тела вращения. Точение производят на токарных станках – простых и винторезных. Инструментом для работы на токарных станках являются резцы. Главным движением при точении является вращательное движение детали. Движение подачи придается режущему инструменту. Прямолинейное движение подачи может быть направлено вдоль или поперек оси вращения изделия, соответственно и подача называется продольной или поперечной. Точение осуществляется на токарных станках. Характерным признаком его является непрерывность резания.
Методом точения можно выполнять следующие виды работ: обтачивание наружных и растачивание внутренних поверхностей, подрезание торцовой поверхности, фасонное точение фасонным резцом и копировальное точение по копиру.
Все способы обработки металлов, основанные на удалении припуска и превращении его в стружку, определяются понятием резание металла. Для успешной работы необходимо, чтобы процесс резания протекал непрерывно и быстро. Форма обрабатываемой детали обеспечивается, с одной стороны, относительным движением заготовки и инструмента, с другой, — геометрией инструмента.
На обрабатываемой заготовке выделяются следующие поверхности; обрабатываемая, обработанная и поверхность резания. При срезании припуска образуется элемент, называемый стружкой.
Выделяются следующие виды стружки (рис. 1):
Рис.1 Виды стружки.
Элементная стружка(стружка скалывания) образуется при обработке твердых и маловязких материалов с низкой скоростью резания (например, при обработке твердых сталей). Отдельные элементы такой стружки слабо связаны между собой или совсем не связаны;
Ступенчатая стружкаобразуется при обработке стали средней твердости, алюминия и его сплавов со средней скоростью резания. Она представляет собой ленту — гладкую со стороны резца и зазубренную с внутренней стороны;
Слитая стружкаобразуется при обработке мягкой стали «меди, свинца, олова и некоторых пластмасс при высокой скорости резания. Эта стружка имеет вид спирали или длинной (часто путаной) ленты;
Стружка надломаобразуется при резании мало-пластичных материалов (чугуна, бронзы) и состоит из отдельных кусочков.
Оборудования для обработки
Токарная обработка выполняется на токарных станках разных типов, различающихся по назначению, компоновке, степени автоматизации и другим признакам. К станкам токарной группы относятся: токарно-винторезные, токарно-револьверные, лоботокарные, токарно-карусельные (рис. 2), токарные автоматы и полуавтоматы, токарные станки с программным управлением.
Точение производят на токарных станках – простых и винторезных. Простой токарный станок отличается от винторезного тем, что нарезка резьбы на винторезном станке может производиться специальным резцом при автоматической продольной подаче.
При изготовлении деталей моделей применяют токарно-винторезные станки, а также настольные прецизионные, винторезные и часовые станки.
Токарный станок необходим для каждой лаборатории и мастерской.
Устройство токарно-винторезных станков.
Токарный станок, оснащенный специальным устройством для нарезания резьбы, называется токарно-винторезным. Станок состоит из следующих основных частей и узлов (сборочных единиц) (рис. 3).
Станина 7— массивное чугунное основание, на котором смонтированы основные узлы станка. Верхняя часть станины имеет две плоские и две призматические направляющие, по которым перемещаются суппорт и задняя бабка. Передняя бабка 2 — чугунная коробка, внутри которой расположены главный рабочий орган станка — шпиндель и коробка скоростей.
Рис. 2 Токарные станки: а — токарно-винторезный, б — токарно-револьверный,
в — лоботокарный, г — токарно-карусельный.
Рис. 3 Токарно-винторезный станок: 1- коробка подач, 2 — передняя бабка, 3 — поперечные салазки, 4 — верхние салазки суппорта, 5 — задняя бабка, 6 — продольные салазки, 7 — станина, 8 — ходовой винт, 9- ходовой вал, 10 — фартук, 11 — гитара сменных зубчатых колес, 12 — маховики управления продольным и поперечным перемещениями, 13 — электрошкаф.
Шпиндель представляет собой полый вал. На правом конце шпинделя крепится приспособление (например, патрон), зажимающее заготовку. Коробка скоростей служит для изменения частот вращения Суппорт — устройство для закрепления резца и обеспечения движения подачи, т.е. перемещения резца в продольном и поперечном направлениях. Движение подачи может осуществляться вручную или механически.
Механическое (автоматическое) движение подачи суппорт получает от ходового вала 9 или ходового винта 8 (при нарезании резьбы).
Суппорт состоит из следующих сборочных единиц; продольных салазок 6, фартука 10, поперечных салазок 3, верхних (резцовых) салазок 4, рез резцедержателя. Коробка подач представляет собой механизм, передающий вращение от шпинделя к ходовому валу или ходовому винту. Коробка подач служит для изменения скорости движения подачи суппорта (величины подачи). Вращательное движение к коробке подач передается от шпинделя через реверсивный механизм (трензель) и гитару со смежными зубчатыми колесами.
Гитара 11 предназначена для настройки станка на различные виды нарезаемых резьб.
Задняя бабка 5 предназначена для поджатия с помощью центра длинных заготовок в процессе обработки, а также для закрепления и подачи стержневых инструментов (сверл, зенкеров, разверток).
Электрооборудование станка размещено в шкафу 13.
Включение и выключение электродвигателя, пуск и останов станка, управление коробкой скоростей, коробкой подач, механизмом фартука и т.д. производится соответствующими органами управления (рукоятками, кнопками, маховичками). Для наиболее ясного представления о работе и взаимосвязях деталей в станках применяют кинематические схемы, в которых детали и передачи изображены условными упрощенными обозначениями. На этих схемах указываются числа зубьев зубчатых колес, диаметры шкивов, число заходов червяков и число зубьев червячных колес, шаг винтовых передач, мощность и частота вращения вала электродвигателя, порядковая нумерация валов, муфт и т.д. На этих схемах четко просматриваются кинематические цепи, связывающие источник движения и исполнительные органы станка, с помощью которых обеспечиваются передача движения, изменение скорости и направление движения.
Режущие инструменты
Точение производится резцами, закрепляемыми на суппорте в резцедержателе. При помощи подкладок резец устанавливают режущей кромкой точно против центра вращения детали. При подаче суппортом к центру резец снимает стружку, которая сходит по передней поверхности резца. При движении суппорта вдоль детали стружка снимается последовательно по длине обтачиваемой детали.
Заточку резцов производят на заточном станке. От правильной заточки резцов зависит производительность работы и чистота обрабатываемой поверхности.
Углы заострения резца, которые должны быть различны для каждого материала, проверяют шаблоном для заточки резцов. Инструменты, применяемые для выполнения процессов токарной обработки, называются режущими. При работе на токарных станках используются различные режущие инструменты: резцы, сверла, зенкеры, развертки, метчики, плашки, резьбонарезные головки и др. Процесс резания подобен процессу расклинивания, а рабочая часть режущих инструментов — клину (рис. 4).
При действии усилия Р на резец его режущая кромка врезается в заготовку, а передняя поверхность, непрерывно сжимая лежащий впереди слой металла и преодолевая силы сцепления его частиц, отделяет их от основной массы в виде стружки. Слой металла, срезаемый при обработке, называется припуском.
Рис. 4 Схемы работы клина (а) и резца (6): 1 — стружка; 2 — резец; 3 — заготовка; 4 — снимаемый слой металла; Р сила, действующая на резей и клин при работе;(5 — угол заострения.)
Процесс резания возможен при наличии основных движений: главного движения — вращения заготовки и поступательного движения резца, называемого движением подачи, которое может совершаться вдоль или поперек изделия, а также под постоянным или изменяющимся углом к оси вращения изделия. Вращение заготовки называется главным движением, так как оно выполняется с большей скоростью.
Скорость резания равна окружной скорости точек, лежащих на поверхности детали, и зависит от диаметра обрабатываемой детали и числа оборотов шпинделя станка. Подсчитывается она по формуле:
где V – скорость резания, м/мин;
D – диаметр изделия, мм;
n – частота вращения шпинделя, мин^-1.
Выбор скорости резания зависит от обрабатываемого материала и стойкости резца.
Форма резцов, применяемых при точении, зависит от вида работы. Название резца указывает на его применение. Кроме резцов, предназначенных для работы на суппорте, в моделировании часто применяются ручные резцы, которыми работают на подручнике.
Ручные резцы представляют собой стальные стержни, обычно круглого сечения, вставленные в ручку. Этими резцами можно выполнить почти все работы в моделировании.
Ручными резцами гораздо проще и легче придавать сложные формы мелким деталям из цветных металлов, пластмасс и древесины. Недостатком ручных резцов является меньшая их стойкость при обработке стали.
Материалом для изготовления резцов служат лучшие сорта инструментальной быстрорежущей стали, самокальные и высоко-углеродистые стали, а также пластинки сверхтвердых сплавов.
Для изготовления ручных резцов чаще всего применяют калиброванную сталь 48, называемую также серебрянкой.
Детали устанавливают на станке одним из приведенных ниже способов:
в трехкулачковом патроне (планшайбе) при обработке сложных детален;
в центрах с поводковым хомутиком при изготовлении валов;
в цангах, которыми, как правило, зажимают мелкие детали.
Приспособления и технологическая оснастка
Универсальность металлорежущего станка расширяется применением принадлежностей и приспособлений. На токарном станке основными из них являются: патроны, центры (рис.5), люнеты. Применяются и вспомогательные приспособления: сверлильный патрон, переходные втулки, хомутики.
Рис. 5 Вращающийся центр | Рис. 6 Самоцентрирующийся трех кулачковый патрон |
Из патронов наибольшее распространение получил самоцентрирующийся трех кулачковый патрон (рис.6). Его конструкция обеспечивает одновременное перемещение трех кулачков в радиальном направлении, благодаря чему заготовка устанавливается по оси шпинделя.
При несимметричном сечении заготовок, когда правильное ее закрепление в трех кулачковом патроне невозможно, применяют четырех кулачковый патрон с раздельным зажимом кулачков или планшайбу (рис.7).
Рис.7 Планшайба
При обработке в центрах, для придания вращения заготовке, применяют поводковые патроны (рис.8). При наружной обработке длинномерных заготовок малого диаметра с целью предотвращения прогиба используют неподвижный (рис.9, а) или подвижный (рис.9, б) люнеты.
Рис.8 Обработка в центрах: 1 — поводковый патрон, 2 — передний центр, 3 — хомутик, 4 — задний патрон, 5 — пиноль задней бабки
Рис.9 Обработка длиномерных заготовок с использованием неподвижного (а) и подвижного (б) люнетов
Конические поверхности на токарном станке обрабатывают следующим способами: широким, токарным резцом, поворотом верхних салазок, смещением корпуса задней бабки в поперечном направлении и с помощью копирной или конусной линейки.
Схема токарной обработки – точение цилиндрической поверхности
Расчет режимов резания.
№ | Вид обработки | Деталь | Заготовка | |||||
D или B, мм | L, мм | t, мм | Ra, мкм | Материал | Твердость | |||
5 | Точение цилиндрической поверхности на проход | 40 | 60 | 0,5 | 0,8 | Сталь 40X | 42 HRC |
studfiles.net
Принцип токарной обработки металла: история и современность
Сегодня металлические детали, узлы и механизмы самой разнообразной конфигурации и самого разного назначения применяются во множестве отраслей. Это и строительство, и машиностроение, и приборостроение, и множество других сфер. Для придания деталям нужной геометрической формы, точных размеров и необходимого функционала используется токарная обработка металла или какого-либо другого материала посредством сложных высокоточных и высокотехнологичных станков и оборудования.
У истоков
Идея о том, что заготовке можно придать необходимые размеры и форму при помощи снятия стружки зародилась в незапамятные времена. Самый первый примитивный токарный станок, известный ученым, датируется еще VII веком до нашей эры. В импровизированные тиски, установленные на вращающейся основе, зажималась деревянная, костяная или роговая заготовка. Подмастерье или раб вращали конструкцию в разные стороны, а мастер при помощи резца придавал детали желаемые размеры и конфигурацию, прикасаясь режущим инструментом ко вращающейся заготовке.
Разумеется, подобный станок был крайне несовершенен. Он не позволял добиваться приемлемой точности, а физическая сила человеческих рук существенно затрудняла обработку, делая ее долгой, трудоемкой и недостаточно точной.
Эволюция
Как ни странно, человечество шло по пути модернизации токарных станков очень медленно. Только к середине XVI века появились машины для обработки металла с ножным приводом, а несколько позже — и с водяным. Но резец все еще держала быстро слабеющая рука мастера. Настоящей проблемой становилось решение следующих задач:
- изготовление металлических деталей сложной геометрической формы;
- нанесение резьбы, как внешней, так и особенно внутренней;
- создание зубчатых колес, столь необходимых в те времена в самых разных отраслях.
К настоящему прорыву в эволюции токарной обработки металла привела промышленно-техническая революция, произошедшая в Европе (главным образом в Великобритании) во второй половине XVIII века. Металлических деталей самого разнообразного назначения требовалось все больше, спрос на них увеличивался в геометрической прогрессии, промышленность развивалась ударными темпами.
Тогда-то и были созданы гораздо более совершенные станки, где режущий инструмент мог перемещаться механически, независимо от физических возможностей оператора. А изобретение парового двигателя позволило создавать токарные станки способные обрабатывать крупные детали и достаточно быстро удалять с тела заготовки толстые слои материала, делать глубокие бороздки, нарезать резьбу с различным шагом и значениями глубины.
Первый прообраз современного токарного станка, содержащий все компоненты, которые мы привыкли видеть в нем сегодня, был окончательно доработан своим изобретателем — англичанином Генри Модсли — ровно в 1800 году. После чего за дело взялись американцы, добившиеся полной механизации процесса токарной обработки и существенно модернизировав конструкцию станка, сделав ее универсальной для производства различных видов работ.
Токарная обработка сегодня
В наши дни потребность в металлических деталях с заданными геометрическими параметрами многократно возросла даже по сравнению с ХХ веком. Помимо сложности форм, к изделиям предъявляются все более и более высокие требования, касающиеся точности, измеряющиеся порой микронами и даже их долями. Несмотря на засилье пластика и некоторых других материалов, детали, выполненные из различных видов металлов, продолжают лидировать в подавляющем большинстве отраслей, где требуется прочность, надежность и долговечность.
Принцип токарной обработки остался неизменным. Посредством резца, фрезы, другого режущего инструмента, с заготовки, жестко закрепленной в специальном вращающемся патроне станка, снимаются лишние слои материала, придавая детали необходимую конфигурацию, геометрические параметры и функциональные характеристики.
Сегодня токарные работы выполняют совершенные, высокотехнологичные станки под управлением мощных компьютерных систем, за которыми осуществляет контроль высококвалифицированный оператор.
В результате удается добиться филигранной точности, обеспечить изготовление деталей сложнейшей конфигурации, самого разнообразного функционала и назначения:
- шестеренки и зубчатые колеса;
- разнообразные валы и втулки;
- гайки, муфты, кольца;
- шкивы и приводы;
- болты, винты, гайки, шайбы;
- другие детали сложных геометрических форм.
Современное токарное оборудование, помимо безупречной точности, обеспечивает высокую скорость обработки и практически полное отсутствие брака и простоев в работе.
Виды токарных работ
Комплекс токарной обработки включает в себя обширный список разнообразных операций. Среди основных из них можно выделить следующие:
нарезка на внешней или внутренней поверхности детали разнообразных видов резьбы;
- сверление, растачивание отверстий, зенкерование, развертывание и так далее;
- отрез частей заготовки, ее доводка до необходимой конфигурации и формы;
- вытачивание различных канавок, углублений и технологических швов;
- обработка наружных поверхностей, торцов и уступов.
Помимо этого, токарная обработка металлов позволяет придать поверхности детали нужную степень шероховатости и необходимую фактуру.
Применяемый режущий инструмент
Сегодня на большинстве производственных и ремонтных предприятий применяются так называемые токарно-винторезные станки с числовым программным управлением (ЧПУ). Они обладают достаточной степенью универсальности, позволяют успешно решать большинство задач. При этом их размеры и стоимость относительно невелики. В последнее время все чаще можно встретить оборудование, оснащенное современными мощными компьютерными системами управления.
Что же касается режущего инструмента, то он отличается весьма широким разнообразием. Резцы, хотя и с большой долей условности, принято подразделять на несколько больших основных групп.
По форме:
- прямые;
- отогнутые;
- лезвия с оттянутой рабочей поверхностью.
Такие резцы могут иметь различную форму и калибр, а также могут быть правыми (двигающимися от задней бабки к передней) и левыми (перемещающимися в обратном направлении).
По назначению:
- проходные, предназначенные для обработки плоских торцевых участков;
- подрезные, обеспечивающие точение поверхностей, расположенных перпендикулярно оси вращения заготовки;
- фасонные, для получения заданного профиля детали;
- расточные для отверстий;
- резьбовые;
- отрезные;
- канавочные.
Резец тщательно подбирается в соответствии со сложностью работ, размером детали, поставленными задачами и сложностью обработки конкретной детали. Именно от выбора режущего инструмента зависит точность исполнения, скорость проведения обработки, скорость вращения шпинделя станка и многие другие аспекты.
Какими бы ни были современные технологии, какие бы ни появлялись инновационные материалы, применяемые в различных отраслях и сферах, токарная обработка изделий из металла, дерева, пластика, композитов продолжает сохранять свое важнейшее значение при осуществлении самых разнообразных строительных, производственных или ремонтных процессов.
Требования к различным деталям и раньше достаточно строго регламентировались разнообразными ГОСТами, ТУ, другими нормативами и лекалами. В наши дни эти требования продолжают ужесточаться, как в плане сложности конфигурации и параметров, так и в части требований идеальной точности.
Нет никаких сомнений в том, что еще очень долгое время профессия токаря будет одной из самых востребованных в производственной сфере. А с учетом все более усложняющегося уровня оснащения специализированной техники, станков и оборудования, эта профессия будет требовать все более высокого уровня квалификации работников, глубоких теоретических знаний и богатого практического опыта.
tokar.guru
Особенности проведения сложных токарных работ по металлу
Металловрезание имеет несколько видов, одним из них является токарная обработка, в том числе сложные токарные работы по металлу. Она представляет собой работу с поверхностью детали либо обработка, металл или древесина, при которой верхний слой обрабатываются с помощью специальных резцов, сверл или режущих насадок ,которые образуют на заготовке своеобразные припуски и бороздки. Токарная обработка может проводиться с целью подгона деталей под необходимые габариты либо целью получения необычной заготовки с технической точки зрения или необычной поверхности заготовки, при этом заказ работы токарной нужно только у квалифицированных мастеров.
Главным процессом, без которого невозможно представить работу на токарной установке, – это главное движение, именно так именуется вращение вокруг своей оси детали, во время которого наносятся насечки либо прорезается верхний слой. Очень важным является движение подачи, которое представляет собой постоянное главное движение без остановок и замедления скорости. Комбинирование движения подачи и главного движения позволяет работать с деталями различных форм, с различной поверхностью и, таким образом, на одном станке можно обрабатывать заготовки конической формы, цилиндра, с насечками, нанесёнными специальной резьбой, или фасонными деталями, при необходимости выполню токарные работы по металлу любой сложности на своем оборудовании.
Для того, чтобы мастер выполняя токарные работы заказ спб мог работать с различными деталями, заготовками, при этом выполнять разнообразные виды работ, в комплекте к токарному станку прилагаются специальные инструменты, с помощью которых можно сделать замеры, определить форму и обозначить местонахождение поверхности, на которой необходимо будет проводить резьбу, а также сверить схему работы с окончательным результатом. В случае, если производство не имеет серийный характер, то, как правило, применяются инструменты для измерения универсального характера, к ним в частности относятся штангенциркули, нутромеры и другие инструменты, а в случае серийного производства используются предельные калибры.
В этой работе мы расскажем определение токарной работы, токарного станка, особенности её проведения и дадим основное описание типам токарных работ, а также определим основные правила, в соответствии с которыми необходимо использовать станки токарного типа, при этом выполним токарные работы по металлу в ракурсе теоретического изучения.
Информация предоставляется на базе изучение Учебной литературы научно-практическая информация, а также социально-экономическое и справочной информация, которая прилагается к работе. Всё это определяет теоретическую и методологическую основу работы.
Понятие токарной обработки. Типы проводимых работ на токарном станке
С помощью оборудования такого типа можно произвести следующие виды работ:
-
Обточить и очистить поверхность деталей, которые имеют цилиндрическую форму;
-
Скорректировать торцы;
-
Выточить канавки наружного типа;
-
Осуществить резку металла;
-
Высверлить на различные отверстия;
-
Провести зенкерование детали;
-
Развернуть или расточить отверстие канала по внутреннему типу;
-
Осуществить шлифовку и заказ металлообработки поверхности детали с помощью фасонных резцов;
-
Обработать резьбу с помощью плашек, резцов, метчиков и головок резьбы накатного устройства;
-
Работать с коническими деталями.
Работа осуществляется посредством специальных резцов, которые подбираются в зависимости от типа токарной обработки металла и делятся на черновые и чистовые. С помощью токарного станка можно обработать обширные и небольшие площади, провести сложные токарные работы по металлу, при этом обеспечить сечение необходимой глубины и регулировать срезаемый слой. Такую функцию обеспечивают различные геометрические параметры резцов.
Резцы делятся на несколько типов:
Особенностью оттянутых резцов является то, что их лезвия более узкие по отношению к крепежной части и могут закрепляться симметрично.
Если рассматривать направление движения резцов, то они могут производить обработку детали справа налево и слева направо. Если резец располагаются с правой стороны, эта работа будет проводиться со стороны правой руки, резец будет располагаться недалеко от большого пальца. Функциональная особенность резца такого типа заключается в том, что он движется от задней и передней бабке, непосредственно справа налево. Лезвия отогнутого типа располагаются аналогично, единственной особенностью является то, что движущей является левая рука и расположены они также под большим пальцем левой руки. Движение производится слева направо.
В зависимости от вида работ, которые могут ли проводиться, резцы для токарного станка делятся на:
-
Резцы проходного типа;
-
Резцы расточного типа;
-
Резцы для подрезания и отрезания;
-
Образцы для фасонной обработки;
-
Для проведения резьбовых отделочных работ.
Выбор геометрии резца влияет не только на точность выполненных работ, но и подбирается в зависимости от качества детали и поверхности, на которой будут проводиться работы. Очень важно учесть имеет ли деталь углы. В данном случае учитываются углы, которые образуются по краю резца и определяют направление движения токарной установки.
Главная и вспомогательная установка подбирается в зависимости от способа её установки, угол на вершине регулируются заточкой деталей.Если вспомогательный угол небольшой, то задействуется режущая кромка, а также повышаются показатели отвода теплоты и меняется уровень стойкости резца. При увеличении главного угла отжим увеличивается, вспомогательная кромка задействуется в меньшей степени, следовательно, уровень стойкости резца уменьшается. Если токарная установка работает с заготовкой, которая имеет большую длину и при этом небольшой диаметр, нужно учитывать возможность ее прогиба. В таком случае рекомендуется выбрать резцы, которые обладают наибольшим на главным углом, при этом для обработки детали потребуется применение меньшей силы и опасность прогиба будет практически исключена. Если работы проводятся на детали достаточно большого диаметра, рекомендуется выбирать главный угол в радиусе от 30 до 45 градусов, а для тонких заготовках выбирается угол 60 до 90 градусов.
Вспомогательный угол определяет расстояние и соотношение кромки вспомогательного типа и установкой резца. Неправильно подобранный угол может привести к тому, что кромка резца будет портить деталь, врезаясь в неё.
Резцы делятся на несколько подвидов:
-
Проходные подразделятся на прямые и изогнутые;
-
Бывают упорными или подрезного типа;
-
Расточные подразделяются на проходные и упорного типа;
-
Отрезные могут быть выполнены по типу фасонных и резьбовых.
Прямые резцы проходного отогнутого типа используются для нанесения резьбы на поверхности наружного типа. Где они, как правило, устанавливают главный угол в радиусе 45-60 градусов, а вспомогательный варьируется от 10 до 15 градусов. Проходные отогнутые резцы используются при продольном сечении. При поперечном могут использоваться исключительно подрезные. В случае, если обрабатывается цилиндрическая поверхность, возникает необходимость работы с торцовой частью, рекомендуется установить проходные упорные резцы, которые будут функционировать по продольному направлению. Резцы подрезного типа используют для отрезания заготовок, они функционируют по поперечному движению и контактируют с центром детали. Резцы различного типа устанавливают в случае необходимости увеличения отверстий, которые были предусмотрены штамповкой или выливанием детали. Такие резцы подразделяются на те, которые образуют сквозные отверстия и упорные. Основной их особенностью является форма лезвия, которое эффективно работает на разных углах. Резцы отрезного типа устанавливаются в том случае, если необходимо отрезать деталь либо выточить глубокие канавки. Резцы фасонного типа используются в том случае, если необходимо работать с фасонными поверхностями небольшой длины и при этом линия не превышает 30-40 миллиметров. Подбираются такие резцы в зависимости от профиля заготовки и могут быть стержневыми, округлыми или призматическими. В зависимости от направления работы они подразделяются на резцы радиального типа и тангенциального типа.
Такие резцы устанавливаются на токарных станках для обработки фасонной поверхности ,для которой применяются резцы стержневого типа либо резцы резьбового типа, которые помогают отрегулировать внутреннюю резьбу независимо от ее формы. Их подбирают в зависимости от профиля и размера резьбы, которая предусматривалась заготовкой.
В зависимости от строения, резцы делится на цельные, составные, припаянные, а также с механическим креплением пластин.
Державки резцов могут изготавливаться индивидуальные или серийные, их форма зависит от сечения и стали, которая используется, основными видами стали являются 40, 45, 50 и 40Х. Большой популярностью пользуется державки, которые крепятся на механическом креплении и изготовлены из твердосплавных пластин, так как они обладают большим уровнем прочности и предотвращают трещины, а также значительно продлевают срок эксплуатации крепежей.
Режущие пластины многогранного типа могут иметь три ,четыре, пять или шесть граней. Их необходимо подбирать в зависимости от положительного угла и лунок, с которыми необходимо будет работать.
Металлорежущий станок является универсальным, на него могут устанавливаться различные детали и принадлежности для того, чтобы обеспечить максимальную функциональность. Основными деталями являются патроны, центры и люнеты. Также очень часто используются такие детали, как сверлильные патроны, втулки для перехода, а также хомуты различного типа.
Кулачковый патрон обладает конструкцией, которая позволяет одновременно регулировать все 3 кулачка, в зависимости от радиального направления, именно благодаря этой особенности деталь может закрепляться по оси шпинделя.
В случае, если деталь имеет несимметричное сечение, очень важно закрепить её четырехкулачковый патрон с обязательным использованием планшайбы. Для того, чтобы обработать центр детали и обеспечить обращение, необходимо установить патроны подводкового типа. Длинные детали, которые имеют малый диаметр, закрепляются с помощью неподвижного либо подвижного люнета для того, чтобы предотвратить их деформацию.
Для конической обработки используют широкий токарный резец, регулируют верхние салазки, а также могут изменять расположение корпуса задней бабки. Это обеспечивается с помощью линейки копирной или конусной.
Широкий резец применяется для работы с короткими деталями конической формы, которые не превышают длину 25-30 мм.Коническая обработка предусматривает использование верхнего суппорта, а также регулирование угла его расположения, который должен быть равен 1/2 угла по вершине конуса детали, которая обрабатывается. В данном случае работа проводится исключительно при ручной подаче.
Если необходимо обточить заднюю бабку, то корпус смещается поперечно, если же необходимо провести обработку конической детали, то смещением детали производят под небольшим углом.
Если во время обработки использовать конусную линейку, можно изготовить поверхность конического типа, при этом угол на вершине будет достигать 40 градусов. В данном случае используется исключительно механическая подача.
Изучив форму и длину детали, можно определить какой способ крепления будет оптимальным:
-
Крепление в патроне;
-
Крепление в центре;
-
Крепление с помощью люнетов.
Работа с деталью, расположенной в центрах, позволяет устанавливать заготовку на несколько различных станках без проведения выверки. Обязательным условием такой обработки является предварительное засверливание отверстий центрового типа. Как правило, тип и размер таких отверстий стандартный. При креплении детали передняя и задняя бабка станка крепится именно в этих отверстиях и обеспечивает качественную фиксацию. Проводниковый патрон помогает вращать деталь от шпинделя по обрабатываемой поверхности.
Пиноли задней бабки и шпиндель используется для крепления центров. Такой центр обеспечивает вращение вместе с деталью, а в случае простоя и установки простого центра, который не вращается в ходе работы, наблюдается изнашивание центра и ухудшается состояние центрового отверстия детали. Для того, чтобы исключить эти негативные последствия, используют специальный центр срезанного типа, который применяется при подрезке торца, а также центр обратного типа, который может применяться в случае проведения токарных работ с деталью небольшого диаметра.
Обработка конструкционных материалов на малогабаритном широкоуниверсальном станке
Назначение и область применения станка
Малогабаритный станок мод. ЕРТ-03 относится к типу малогабаритных и позволяет проводить токарные работы с различными видами материалов, в том числе обрабатывать древесину и пластмассы. Характерной чертой данной модели является возможность настройки базового токарного варианта и изменения всех видов наладки, в том числе сверлильной и деревообрабатывающей. Такой станок многофункциональный и позволяет выполнять токарные работы по металлу, все виды сверлильных и расточных работ, а также фрезеровочные работы. А также с помощью него можно обрезать деталь, распиливать древесину, строгать, а также зачищать поверхность и полировать её.
Основные узлы и органы управления станком:
-
основа устройства;
-
рычаг для управления подачей механического запуска продольного типа;
-
покрытие гитары, под которой расположены зубчатые колеса сменного типа, они относятся к коробке подач;
-
рычаг управления диапазонами и скоростью движения шпинделя;
-
шпиндельная коробка;
-
сигнализатор работы электроустановки;
-
рычаг подключения движения шпинделя, как прямого, так и обратного;
-
кнопка «пуск» запуска блока электроустановки;
-
кнопка «стоп» для прекращения работы электроустановки;
-
крышка шпиндельной коробки;
-
стойка вертикального перемещения шпиндельной коробки с подвижной кареткой;
-
крышка блока электрооборудования станка;
-
маховик вертикального перемещения шпиндельной коробки;
-
винт вертикального перемещения стойки;
-
кожух ограждения электродвигателя и блока электрооборудования станка;
-
болт крепления каретки на стойке вертикального перемещения шпиндельной коробки;
-
трех кулачковый патрон;
-
резцедержка;
-
суппорт;
-
рукоятка зажима пиноли задней бабки;
-
задняя бабка;
-
маховик перемещения пиноли задней бабки;
-
маховик ручного продольного перемещения суппорта;
-
ходовой винт продольного перемещения суппорта;
-
маховик поперечного перемещения стола суппорта.
Основные технические характеристики станка
Диаметр детали, которая может устанавливаться на токарный станок:
-
в центральных частях – 105х440;
-
в патроне – 230 размер диаметра над суппортом;
-
на столе – 140 х 160 х 180.
Максимальные размеры детали, которая может устанавливаться:
-
на планшайбе или в патроне, 600 мм
-
Максимальный диаметр сверления, 10 мм
-
Диаметр отверстия в шпинделе, пинали задней Конус Морзе2 АТ6
-
бабки и вертикально-фрезерной головки (ГОСТ2848-75)
Максимальные перемещения рабочих органов, мм:
-
продольное суппорта при точении 440 (220)
-
продольное суппорта при фрезеровании 600 (480)
-
поперечное суппорта 100
-
вертикальное шпиндельной коробки 18
-
пиноли задней бабки 50
Максимальные наладочные перемещения стойки, мм:
-
Вертикальное 80
-
Горизонтальное 420
-
Максимальный ход зажимных губок тисок, 100 мм
-
Поворот резцедержки, град. 90х4
-
Максимальные размеры деревообработки,mmi
-
толщина распиловки (дисковой пилой) 35
-
ширина фугования 100
-
Максимальный ход вертикального стола, 100 мм
-
Максимальный ход подвижной резцедержки, 70 мм
-
Угол поворота подвижной резцедержки, 45 град
-
Максимальный угол поворота вертикально-фрезерной головки, 45 град
-
Количество ступеней частот вращения шпинделя 6
-
Диапазон частот вращения шпинделя, 1/мин. 160…2500
-
Продольная механическая подача, мм/об. 0,1…0,16
Шаг нарезаемых резьб:
-
метрических, 0,5…2,5 мм
-
дюймовых, п/1» (ниток на дюйм) 10…20
-
Цена деления лимба маховика, мм
-
суппорта, шпиндельной коробки и продольной подачи 0,02
-
пиноли задней бабки 0,04
-
Мощность электродвигателя, 0,37квт
-
Питание электрооборудования однофазное, 220B; 50 Гц
-
Габарит станка (длина х ширина х высота), 1120х680х640 мм
-
Масса (без оснастки и инструмента), 160 кг
Нормы работы с токарным оборудованием. Наиболее распространенные ошибки
Основными деталями и, на характеристики которых необходимо обращать внимание для длительной эксплуатации токарных устройств являются:
-
Вращающиеся детали и заготовки станочного типа;
-
Стружка, которая является результатом процесса резки.
Для того, чтобы обеспечить максимальный срок эксплуатации токарного устройства, необходимо хорошо закреплять детали перед началом проведения работ или регулировать скорость в зависимости от надежности крепления.
При проведении точения и чистовых видов работ точность сохраняется на уровне 7-8 квивалента, шероховатость сохраняется на уровне 1,6-3,2 мкм. Разрезка деталей осуществляется посредством специальных отрезных резцов, которые выбираются исходя из материала детали и диаметра. Могут использоваться прямые и обратные резцы такого типа. Особенностью прямых резцов является их длинная и неширокая головка, которая приспособлена для прорезывания детали и образования небольшого количества стружки. Их недостатком является невысокий уровень прочности и жесткости, эти факторы необходимо учитывать при выборе деталей, которые изготовлены из очень прочного материала. Если необходимо провести разрезание жестких заготовок, то место среза выбирается максимально близко к кулачкам патрона и не должно превышать 1 миллиметр от заготовки. Резец отрезного типа закрепляется рядом с линией центров станка, а по отношению к оси заготовки устанавливается перпендикулярно.
В случае, если возникает необходимость разреза детали большого диаметра, возможен такой вид поломки как обламывание резца. Такой эффект возникает в результате того, что перемычка прогибается и резец отрезного типа может быть защемлен в прорези. В таком случае рекомендуется не дорабатывать деталь до центра приблизительно 1,5-2,0 миллиметра, после чего прекратить работу с помощью резца и вручную далее осуществлять вращение шпинделя. Ни в коем случае нельзя поддерживать руками часть детали, которая отрезается. Также стоит учитывать, что если прорезь узкая и глубокая, то стружка может выходить достаточно медленно, поэтому режим работы станка необходимо отрегулировать, а диаметр прорези постепенно расширять.
Перед проведением сверления, зенкерование и развертывания, рекомендуется несколько раз проверить прибор для того, чтобы правильно соотнести центры.
Необходимыми условиями для правильного функционирования токарного станка являются:
-
правильная фиксация деталей;
-
правильное соотношение торца оси вращения и установка её строго перпендикулярно;
-
исключение выпуклостей на торце;
-
правильная установка сверла.
Для того, чтобы обеспечить все эти условия, необходимо подрезать торец перед началом проведения работ, а при установке детали обеспечить минимальный вылет. Для того, чтобы правильно установить направление движения сверла, рекомендуется сделать специальное углубление на детали с помощью центровочного сверла. Очень важно учесть, что глубина сверления должна соответствовать диаметру отверстия, которое должно получиться.
Очень редко сверление производится в ручном режиме, так как оно требует больших усилий и не всегда может быть проведено без нарушение центровки. В связи с этим рекомендуется обрабатывать детали диаметром более 20 мм двумя сверлами в автоматическом режиме. Первое сверло должно быть два раза тоньше предполагаемого отверстия, это обеспечивает равномерный выход стружки, постепенное врезание и значительно снизит усилие подачи.
Для того, чтобы зачистить поверхность и исключить образование заусенец, а также снять небольших фасок используют опиливание. Для его проведения выбирают напильники различной формы и с разными насечками. В зависимости от типа детали и предпочтения токаря, который проводит токарные работы по металлу в спб можно использовать насаженную или цельную ручку. Для того, чтобы избежать получения травм, рекомендуется выполнять опиливание примерно под углом 45 градусов с разворотом вправо. При этом ручка напильника должна находиться в левой руке, а его конец фиксируется правой.
Одним из заключительных этапов обработки детали является полирование, которое позволяет практически полностью исключить шероховатость и подготовить поверхность для дальнейшей обработки. Для полировки используют шлифовальные шкурки, которые подбираются в зависимости от поверхности и могут обладать разным уровнем в зернистости. Полировка проводится в ручную только правой рукой либо обеими руками, если поверхность достаточно обширна, при этом положение токаря, который проводит токарно фрезерные работы по металлу, должно быть аналогично положению при опиливании. Таким образом, шкурка удерживается левой рукой, а задний её конец придерживается правой. Меры предосторожности при ручном зашкуривании: одной из них является запрет охватывать рукой шкурку, так как существует риск наматывания на заготовку и защемления пальцев рук.
Учитывая то, что при опиливании, шлифовке с токарного станка не снимаются нерабочие резцы, необходимо проводить такой вид работы достаточно аккуратно для того, чтобы исключить порезы рук.
Заключение
При написании данной работы были выполнены все поставленные цели и задачи, а также проведён полный обзор работы на токарном станке, особенностей проведения определённых видов работы, мер предосторожности и устранения неисправностей.
На сегодняшний день обработка различных деталей на токарных станках пользуются большой популярностью, благодаря высокой точности замеров и обеспечению хорошего уровня полировки и шлифовки. Такие детали полностью готовы к дальнейшей обработке, при этом трудоемкость составляет от 20 до 35 процентов по отношению к трудоемкости обработки деталей, которые были обработаны на бортовом оборудовании. На сегодняшний день токарные станки модернизируют и основной задачей такого улучшения являются обеспечение высокой производительности и уменьшение времени на операции по подготовке перед проведением работ. Дальнейшая модернизация предусматривает полный отказ от ручного управления, которая чревато травмами и возможными неточностями при проведении работ. Основной целью модернизации токарного станка является включение ручного управления только на стадии заключительной обработки, а также изготовления деталей в единственном числе, максимальная автоматизация для того, чтобы оптимизировать оплату труда и уменьшить затраты на расходные материалы.
С помощью токарных станков можно:
-
производить различные детали цилиндрической и конической или фасонной формы, обрезать заготовки и осуществлять нарезку с помощью резцов метчиков и плашек.
-
очистить или обрабатывать резьбу различными сверлами с зенкером или развертками, которые позволяют подстроить деталь под необходимые параметры;
-
накатать рельеф или создать зубчатые колеса мелкомодульного типа.
Токарная установка пользуется большой популярностью благодаря своей функциональности и универсальности, так как на ней можно обрабатывать детали, изготовленные из различных материалов и подстраивать установку под практически любую форму и качество детали. Возможность проведения работ вручную позволяет обрабатывать даже самые хрупкие детали, при этом выполнять все требования по проведению работ. Как правило, последнее время токарная установка используется в качестве универсального оборудования с применением ручных настроек, это обусловливается большим количеством индивидуально изготовленных деталей, которые требуют индивидуального подхода, таким образом, стоимость проведения работ на токарной установке увеличивается, а квалификация токарей требует повышения.
karavangard.ru
Токарная обработка металла – Слесарное дело
Токарная обработка металла – это один из видов обработки резанием. Она осуществляется на токарном станке с ручным или автоматическим управлением. При токарной обработке в отличие от фрезерования во вращение приводится не режущий инструмент (фреза), а металлическая заготовка или полуфабрикат; при этом движение резания совершается за счет этого вращения. В процессе обработки неподвижно зажатый режущий инструмент (токарный резец) посредством суппорта приводится в движение вдоль обтачиваемой заготовки для снятия с неё стружки. Резец совершает 2 вида движений: движение подачи на врезание (движение поперечной подачи) и движение продольной подачи.
В классификации технологий изготовления согласно стандарту DIN 8580 токарная обработка отнесена к методам разделения материала.
Классической токарной обработке подвергаются главным образом вращательно-симметричные (круглые в поперечном сечении) детали. Однако современная технология токарного станка с компьютерным ЧПУ позволяет изготавливать даже заготовки, которые раньше производились только с помощью фрезерного станка.
Для изготовления же мелких и микроскопических деталей, например, в часовой, медицинской и микротехнической промышленности, применяется прецизионная токарная обработка.
Осью отсчета при токарной обработке является ось вращения главного шпинделя токарного станка, вокруг которой вращаются заготовка и зажимной патрон. Эта ось обычно называется осью Z. Она направлена от зажимного патрона к задней бабке станка. Перпендикулярно оси Z проходит ось X. При этом высота токарного резца над плоскостью XZ жестко выставляется во время наладки станка. Чаще всего режущая кромка резца располагается точно в плоскости XZ.
Показания измерительной шкалы оси X и возможных систем измерения перемещений в 2 раза превышают фактическую длину хода резца. Т.е. при перемещении резца на 1 мм на шкале будет показано 2 мм, так как его движение влияет на радиус вращающейся заготовки (изменяет его на 1 мм), поэтому её диаметр изменится на 2 мм.
В токарных станках с компьютерным управлением чаще всего дополнительно измеряется и выводится на дисплей третья координата, угол главного шпинделя, которая при наличии соответствующих возможностей аппаратного и программного обеспечения может регулироваться.
К параметрам резания, которые могут регулироваться при токарной обработке, относятся скорость резания, продольная подача и глубина резания. Путем оптимизации этих параметров достигаются:
– оптимальная стойкость резца,
– улучшенное стружкообразование,
– необходимое качество поверхности обрабатываемой детали,
– максимально возможный объем срезаемой стружки,
– небольшое усилие резания,
– скорость резания и частота вращения шпинделя.
При этом скорость резания зависит от материала заготовки, а также от применяемого токарного резца и вида токарной обработки. Ориентировочные значения скорости резания указываются в специальных табличных справочниках. Частота вращения шпинделя зависит от скорости резания и диаметра обточки.
Продольная подача резца измеряется в миллиметрах на 1 оборот шпинделя. При черновой обточке следует из экономических соображений устанавливать максимально большую продольную подачу. Её величина ограничивается мощностью токарного станка, допустимой нагрузкой на режущую кромку резца и прочностью заготовки (в связи с опасностью её загибания). При чистовой обточке чаще всего устанавливается малая продольная подача для получения более высокого качества поверхности детали.
Глубина резания при цилиндрической обточке зависит от величины подачи резца на врезание, а при поперечной прорезке – от ширины режущей кромки резца. При черновой обточке следует устанавливать максимально возможную глубину резания. При чистовой обточке она должна соответствовать величине припуска.
Технологию токарной обработки металлов можно разбить на отдельные виды по разным признакам:
1) В зависимости от расположения обрабатываемого места на заготовке различают наружную обточку и растачивание. При наружной обточке обрабатываются наружные поверхности заготовки, а при растачивании – внутренние поверхности какого либо отверстия.
2) В зависимости от направления подачи резца различают продольную обточку и поперечную обточку (торцевание). При продольной обточке резец движется вдоль оси вращения (т.е. оси Z), а при поперечной обточке – перпендикулярно к ней, т.е. вдоль оси X. Эти 2 движения являются основными при токарной обработке. Более сложные формы обрабатываемой заготовки достигаются путем совмещения этих движений. Когда резец движется прямолинейно под некоторым углом к оси Z, заготовка приобретает коническую форму. При профильной обточке резец может двигаться по траекториям любой кривизны и тем самым создавать самые разнообразные вращательно-симметричные формы.
3) В зависимости от геометрии полученной заготовки различают следующие виды токарной обработки:
а) цилиндрическую обточку, при которой образуется наружная боковая поверхность цилиндра;
б) поперечную обточку, при которой создается поверхность основания цилиндра, то есть плоскость;
в) конусную обточку, при которой формируется наружная боковая поверхность конуса;
г) винтовое точение, при котором образуются поверхности вдоль винтовой линии;
д) фасонную обточку, при которой форма резца передается заготовке, например, при скруглении углов с помощью резца с режущей кромкой в форме четверти окружности;
е) профильную обточку, при которой создается вращательно-симметричная поверхность любого профиля за счет соответствующей траектории движения резца.
Профильную обточку можно дальше разделить на:
i) свободную профильную обточку, при которой токарный резец накладывается на опору и ведется вручную, либо осуществляется ручное управление одновременно двумя маховиками (для осей Z и X). Для этого необходимы определенные практические навыки, а кроме того при этом виде токарной обработки не обеспечивается стабильная точность размеров заготовок.
ii) обточку по шаблону (копиру), при которой осуществляется электронное или механическое ощупывание формы образца и её перенос на траекторию резца и тем самым – на обрабатываемую заготовку.
iii) профильную обточку с использованием токарных станков с ЧПУ, при которой траекторией резца управляет компьютерная программа.
ж) нецилиндрическую обточку, при которой создаются поверхности, не являющиеся вращательно-симметричными, например, поверхности шестигранной головки болта.
з) затыловывание резцом, при котором образуются задние поверхности режущего инструмента, например, поверхности на заготовке для фрезы.
4) В зависимости от качества обрабатываемой поверхности различают: а) черновую и б) чистовую токарную обработку.
При черновой токарной обработке с заготовки снимается значительно больший объем стружки, чем при чистовой. При этом заготовка лишь приблизительно доводится до требуемого размера. При чистовой токарной обработке обеспечивается высокое качество поверхности.
5) Кроме того, токарную обработку металлов можно разделить на следующие виды:
а) обточку, при которой токарный резец движется вдоль поверхности заготовки,
б) отрезку резцом, при которой производится непосредственное врезание в обрабатываемую заготовку, в результате чего она отделяется от остальной части болванки.
в) обточку фасонным прорезным резцом, с помощью которой, например, создаются канавки под стопорные кольца.
6) По способу нарезания резьбы на токарном станке (за один или несколько проходов) различают: а) нарезание резьбы резцом и б) резьбовой гребенкой.
При этих двух видах токарной обработки резец выполняет продольную обточку. Однако при этом его продольная подача соответствует шагу резьбы, благодаря чему резец или же резьбовая гребенка оставляет след на желаемой винтовой линии.
а) При нарезании резьбы резцом применяется фасонный резец. Его профиль соответствует форме желаемой резьбы, например, профиль с углом 60° для метрической резьбы и с углом 55° – для трубной резьбы. При этом особенно при нарезании крупной резьбы резец несколько раз проходит по одному и тому же следу, каждый раз заглубляясь чуть дальше, так как силы резания оказываются слишком высокими для нарезания резьбы за один проход.
б) Резьбовая гребенка имеет несколько режущих кромок, расположенных друг за другом. При этом каждая режущая кромка имеет профиль резьбы, а расстояние между кромками соответствует шагу резьбы. Эти кромки смещены относительно друг друга по высоте, так что каждая следующая кромка проходит по следу предшествующей чуть глубже.
Нарезание резьбы резцом является более гибким по сравнению с нарезанием резьбы резьбовой гребенкой, так как с помощью одного и того же резца можно изготавливать резьбу с разным шагом. Зато резьбовая гребенка нарезает резьбу всего за один проход, тем самым значительно сокращая время обработки.
Метод нарезания резьбы резцом также позволяет изготавливать коническую резьбу. При этом, чтобы резец перемещался за один оборот шпинделя токарного станка точно на шаг резьбы, движение его продольной подачи либо механически привязывается к приводу шпинделя, либо электронно синхронизируется с вращением шпинделя.
< Предыдущая | Следующая > |
---|
slesario.ru
ТОЧЕНИЕ – это… Что такое ТОЧЕНИЕ?
ТОЧЕНИЕ — ТОЧЕНИЕ, действие по гл., источание. Точивый, точащий из себя, источающий. Мироточивые главы ·св. мучеников. | Точивый, тчивый, чивый, тороватый, щедрый. Точливая ель, из которой много смолы выступает; | Точить что, истачивать, исподволь… … Толковый словарь Даля
ТОЧЕНИЕ — ТОЧЕНИЕ, действие по гл., источание. Точивый, точащий из себя, источающий. Мироточивые главы ·св. мучеников. | Точивый, тчивый, чивый, тороватый, щедрый. Точливая ель, из которой много смолы выступает; | Точить что, истачивать, исподволь… … Толковый словарь Даля
ТОЧЕНИЕ — ТОЧЕНИЕ, точения, мн. нет, ср. Действие по гл. точить1 в 1 и 2 знач., то же, что точка2. Точение на токарном станке. «Он стал задремывать под звуки точения ножа.» Л.Толстой. Толковый словарь Ушакова. Д.Н. Ушаков. 1935 1940 … Толковый словарь Ушакова
точение — натачивание, очинка, обработка, вытачивание, оттачивание, зачинивание, затачивание Словарь русских синонимов. точение сущ., кол во синонимов: 8 • вытачивание (4) • … Словарь синонимов
ТОЧЕНИЕ — (токарная обработка) обработка поверхностей тел вращения резанием. Характеризуется вращательным движением заготовки (главное движение) и поступательным движением инструмента резца (подача) … Большой Энциклопедический словарь
точение — ТОЧИТЬ, точу, точишь; точенный; несов. Толковый словарь Ожегова. С.И. Ожегов, Н.Ю. Шведова. 1949 1992 … Толковый словарь Ожегова
точение — Лезвийная обработка с вращательным главным движением резания и возможностью изменения радиуса его траектории. [ГОСТ 25761 83] Тематики обработка резанием EN turning DE Drehen FR tournage … Справочник технического переводчика
ТОЧЕНИЕ — (токарная обработка) технологический процесс обработки резанием наружных, внутренних и торцовых поверхностей тел вращения, а также спиральных и винтовых поверхностей с помощью (см.) … Большая политехническая энциклопедия
точение — см. Точить. * * * точение (токарная обработка), обработка поверхности тел вращения резанием. Характеризуется вращательным движением заготовки (главное движение) и поступательным движением инструмента резца (подача). * * * ТОЧЕНИЕ ТОЧЕНИЕ… … Энциклопедический словарь
Точение — токарная обработка, одна из основных операций обработки резанием, выполняемая на металлорежущих станках (См. Металлорежущий станок) и деревообрабатывающих станках (См. Деревообрабатывающий станок) токарной группы, обычно при вращательном… … Большая советская энциклопедия
Точение — I ср. 1. процесс действия по гл. точить I 1. 2. Результат такого действия; точка V 2.. II ср. 1. процесс действия по гл. точить IV 1. 2. Звуки, возникающие в процессе такого действия; вторая часть песни глухаря. Толковый словарь Ефремовой. Т. Ф.… … Современный толковый словарь русского языка Ефремовой
dic.academic.ru