Выбор и установка резца – Энциклопедия по машиностроению XXL
Следующим элементом наладки является выбор и установка резца в резцедержателе по высоте оси центров станка (рис. 9.2). Для этого резцедержатель подводят к центру задней бабки, вершину головки резца устанавливают так, чтобы вылет резца не превышал высоты его державки, определяют взаимное положение вершины головки резца и центра станка и совмещают их по высоте введением подкладок под державку резца. Подкладки должны иметь параллельные и хорошо обработанные поверхности, не должны по длине и ширине выходить за пределы опорной поверхности резцедержателя. Число подкладок должно быть не более двух. [c.298]ВЫБОР И УСТАНОВКА РЕЗЦА [c.276]
При выборе технологического процесса и последовательности отдельных переходов необходимо стремиться к тому, чтобы наиболее точные поверхности обрабатывались резцами балансира и в первую очередь передним резцом (№ 1), который может работать до жесткого упора.
Установка резцов при затачивании и выбор характеристики абразива приведены в табл. 211—213. [c.301]
Реализацию этих отступлений обеспечивает установка резцов и настройка зубострогального станка. Это облегчает выбор оптимальных параметров передачи и расширяет технологические возможности процесса зубонарезания.
Неточность и износ станка. Известно, что все металлообрабатывающие станки изготовляются с определенной регламентированной точностью согласно ГОСТу, т. е. каждый станок имеет неточность установки и перемещений рабочих органов в сравнении с идеальной кинематической схемой. Так, например, по данным ГОСТа радиальное биение шпинделей токарных и фрезерных станков допускается в пределах 0,01—0,015 мм, торцовое биение — 0,01—0,02 мм непрямолинейность и непараллельность направляющих станин токарных станков на длине 1000 мм допускается в пределах 0,02 мм, непараллельность осей шпинделей токарных станков направлению движения кареток на длине 300 мм в вертикальной плоскости 0,02—0,03 мм, а в горизонтальной плоскости — 0,01—0,015 мм. Следовательно, неточность кинематической схемы металлорежущего станка переносится на обрабатываемую деталь. При нагружении станка усилиями резания неточность кинематической схемы возрастает за счет одностороннего выбора зазоров в соединениях.
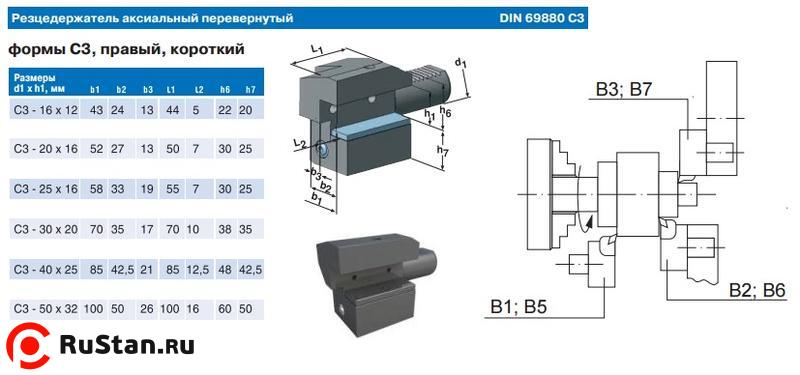
Шпон срезается с чурака ножом, работающим совместно с обжимной линейкой. Около режущей кромки линейка создает поле напряжений, при котором нагрузка на заднюю Qз.т и переднюю Опт грани мало отличается, поэтому эти грани изнашиваются одинаково и затупление резца замедляется. Организация лущения сводится к выбору углов заточки, установки ножа, профиля линейки, расположения ее относительно ножа и величины обжима шпона. Угол заточки находится в пределах р=0,324-0,44 рад (18—25°). Задний угол а изменяется
Простым и эффективным средством гашения колебаний, кроме выбора режимов резания, является установка резца под углами X, не равными 0°. Как видно из рис. 40, при [c.57]
Выбор способа установки и крепление заготовки и расположение резцов. Установочными [c.291]
Выбор способа установки и крепления заготовки и расположение резцов. Установочными базами обрабатываемой детали являются предварительно торцованные и зацентрованные концы вала. При обработке заготовка устанавливается в центрах с поджимом центром задней бабки. Крутящий момент на заготовку передается поводковым центром, установленным в шпинделе (см. рис. 229).
[c.302]
Выбор способа установки и крепления заготовки, подбор и расстановка суппортов и резцов. Установка и крепление заготовки производятся в самоцентрирую-щем трехкулачковом патроне с автоматическим зажимом от гидропривода.
[c.330]При невысоких требованиях к чистоте поверхности (в пределах 5—6-го класса) чистовую обработку наружных цилиндрических поверхностей часто ведут обычными проходными резцами, руководствуясь рекомендациями по выбору углов и других элементов, а также правилами установки резцов, изложенными ниже. [c.164]
Токарный инструмент выбирается на основе геометрических и технологических требований к выполняемым этим инструментом операциям, которые формулируются в самой общей форме, т. е. без учета характеристик какого-либо конкретного станка. Геометрические критерии выбора токарных инструментов — это геометрия режущей кромки, направление установки резца и исключение каких-либо столкновений резца во время его движения. Определяются крайние положения главной и вспомогательной режущих кромок, радиус скругления вершины резца, наибольшие размеры хвостовика и патрона, а также минимальная рабочая длина инструмента. Критерий резания — это режущий материал и граничные значения углов и размеров режущих кромок резцов. Для инструментов, которые удовлетворяют этим требованиям, гарантируется плавная обработка с хорошими (приемлемыми) условиями резания.
Выбор конструкции режущего инструмента сказывается на выполнении всех требований, предъявляемых к станку. В данном случае обработка нескольких торцов несколькими резцами позволяет уменьшить длину радиального хода летучего суппорта и дисбаланс масс, вращающихся на шпинделе. Это особенно ценно при больших вылетах суппорта (относительно направляющих), так как уменьшает возможность появления вибрации. Многоинструментная обработка повышает производительность, упрощает конструкцию станка, но имеет и недостатки необходимость дополнительного проектирования инструментальной оснастки для каждой новой детали и специального приспособления для контроля точности установки всех резцов.
Настройка на глубину врезания резца и выбор положения, при котором холостой ход салазок изменяется на рабочий, производятся соответствующей установкой передвижных упоров, расположенных с обеих сторон верхнего цилиндра. [c.76]
Натяг принимается порядка 0,1—0,15 мм. Головка имеет хвостовик, на наружной поверхности которого выполнены посадочные поверхности Б для соединения со стеблем. У головок диаметром до 90 мм резьба прямоугольного профиля двухзаходная, а у головок большего диаметра — трехзаходная. На переднем торце головки выполнено отверстие А, соосное с осью головки и имеющее резьбовой участок. В это отверстие с помощью рукоятки 1 вворачивают центрирующий палец 3 (рис.
Разработку траектории движения резцов при токарной обработке начинают с вычерчивания контура заготовки и выбора исходной точки движения вершины резца или крайней точкой его режущей кромки.

Как известно, резец рекордера при записи перемещается по прямой линии вдоль радиуса записываемого диска такое же перемещение иглы звукоснимателя при проигрывании пластинки применяется в редких случаях в проигрывателях высшего класса, обычно же игла перемещается по дуге, соответствующей повороту тонарма на ножке, общепринятой в конструкциях звукоснимателей. Поэтому между направлением колебаний иглы и радиусом, вдоль которого колеблется резец при поперечной записи, образуется некоторый угол, называемый горизонтальным утлом погрешности. Как видно из рис. 6-5, в случае прямого тонарма этот угол был бы равен углу ф между радиусом Я и касательной к дуге, проведенными через точку контакта иглы с пластинкой. Такое несоответствие в направлении колебаний резца и иглы вносит изменения в воспроизводимый сигнал— возникают так называемые угловые искажения. Соответствующим выбором конструкции тонарма и правильной установкой его на плате проигрывателя угловые искажения можно свести к минимуму. Во-первых, вместо прямого тонарма применяют изогнутый. Как следует из рис. 6-5, а, углу Ф также ра-
[c.146]
На рис. 1.24,0 приведено приспособление для наладки резцов. Резец 4 устанавливают в пазу корпуса II и крепят пружинным прихватом 6. По направляющим корпуса перемещается ползун 7 с закрепленными на нем кронштейнами 2 и 9 для установки индикатора 5 н микрометрического винта /. Вершина резца упирается в подпружиненный шток 8, связанный с индикатором, а регулировочный винт S — в торец микрометрического винта 1. Пружина 10 предназначена для выбора зазоров в измерительной цепи при смещении резца вдоль оси паза.
[c.55]
Наладка многорезцового станка, включает выбор и установку режущего инструмента по заранее составленной тёхнологической схеме (карте наладки), установку в требуемое положение всех устройств, обеспечивающих цикл работы станка, осуществление пробных циклов следующую за этим подналадку. Для сокращения времени наладки применяют эталонные детали и шаблоны. На рис. 79 показаны два способа обтатавания вала на многорезцовом станке с помощью продольного суппорта. Первый способ — обтачивание с продольной подачей (рис. 79, а). Каждый резец установлен на определенный диаметр. По мере продольного перемещения суппорта резцы последовательно вступают в работу. Длины отдельных обработанных ступеней вала определяются взаимным расположением резцов. Резец I проходит в резании путь, равный сумме длин участков /д + + /з — резец 2 — путь, равный /2 + /з и резец 5 — путь, равный /3. Второй способ — обтачивание с врезанием и последующей продольной подачей (рис. 79, б). Резцы /, 2, расположенные так же, как в предыдущем случае, начинают обрабатывать заготовку в разных местах по длине вала, а не с конца, как в первом случае. Вначале суппорт перемещается в по-
[c.92]
Выбор той или иной схемы определяется подсчетом машинного и вспомогательного времени обработки. При этом обычно возникает вопрос что выгоднее — сначала подрезать ступени, а потом обтачивать их начисто или производить чистовую обработку в обратной последовательности После подрезания всех уступов отпадает необходимость измерения длин шеек при их чистовой обработке, что является преимуществом такого порядка работы. Неудобство этого метода заключается главным образом в том. что при срезанном припуске по длине пробные стружки при установке резца на размер приходится снимать с участка шейки, который должен остаться неповрежденньш на готовом валу. В случае ошибки нри установке резца на размер концевая часть шейки может оказаться меньшего диаметра, чем это требуется по чертежу. При обтачивании шеек до подрезания полученные при установке на стружку уступы будут срезаны при подрезании торцов. Очевидно, целесообразнее все-таки сначала обтачивать, а затем подрезать последовательно торцы каждой ступени.
[c.106]
Стойкость резца. Выбор скорости резания зависит от требуемой стойкости режущего инструмента. Чем выше скорость резания при всех прочих равных условиях, тем быстрее изнашивается резец, тем чаще приходится его перетачивать и тем больше затрачивать времени на его съем и установку на станке. Таким образом, частично теряются преимущества от увеличенной скорости, а при излишнем повышении ее получается даже снижение производительности. Но из этого не следует, что нужно работать при заниженных скоростях резания. Чтобы можно было работать с высокими скоростями резания наши токари-пере-довики улучшают геометрию инструмента, увеличивают промежутки времени между переточками путем подправки лезвия резца, не снимая его со станка, и т. д. Их достижения не случайны за ними кроется большая работа, основанная на глубоком знании явлений резания и длительных подготовительных опытах.
[c.296]
Результаты, полученные при измерениях на дифракционных спектрографах, обрабатывают другими методами. В Аргоннской лаборатории была создана установка Пашена с конфигурацией, столь близкой к круговой, что можно было измерить длины волн вполне с удовлетворительной точностью (0,001 см ), пользуясь формулой решетки тА. = d(sin 0 — sin 0 ). Лишь немногие решеточные системы подобного типа обеспечивают такую точность, так что прибор приходится калибровать по эталонам длин волн. Поскольку дисперсия нелинейна, необходимо вычислить поправочную кривую (обычно пользуются методом наименьших квад-эатов и полиномиальной аппроксимацией). При выборе эталонов необходима некоторая осторожность, так как не всегда можно сравнить линии в различных порядках (особенно для старых решеток — из-за ошибки, обусловленной затуплением резца). Поскольку более новые плоские решетки допускают такое сравнение, при выборе эталона длины волны допустима большая свобода. Почти то же самое относится к эшелле.
[c.355]
Выбор карусельного станка производится по данным, приводимым в справочниках или каталогах станков (см. [18], [24] и др.). Из большого числа имеющихся отечественных карусельных станков останавливаем свой выбор на современном карусельном одностоечном станке модели 1508, имеющим диаметр планшайбы 710 мм, допускающим установку детали массой до 1300 кг и обработку детали боковым суппортом диаметром до 710 жл. Этот станок имеет дистанционное управление рабочими движениями и установочными перемещениями с подвесного кнопочного пульта. Для закрепления заготовки с внутренней стороны целесообразно применить самоцентрирующий патрон со специальными кулачками методом вразжим ( враспор ). Для закрепления режущих инструментов используется ряд вспомогательных инструментов резцедержавки, оправки для резцов и зенкеров, плавающая оправка для развертки.

Обработка всех ступеней детали может производиться либо за одну, либо за несколько операций. Выбор конкретного варианта зависит главным образом от числа ступеней, доступных для обработки при данном закреплении заготовки, и от диаметров, ступеней. Если ступеней мало и малы их диаметры, обрабатывают все ступени за одну операцию с одной установки. Когда же ступеней много и у них большие диаметры, то при объединени всех переходов в одну 01перацию возникают затруднения в пользовании лимбом поперечной подачи приходится оперировать большим числом делений на лимбе. Одновременно усложняется пользование упорами. Кроме того, удлиняется общий путь резца при обработке каждой детали. Наконец чем выше число ступе ней и чем больше их диаметры, тем интенсивнее изнашивается резец. Это ведет к быстрой потере настроенного размера и часто смене резцов, следовательно, вызывает частую переналадку” станка.
[c.201]
С Г-образным рычагом-прижимом. Для стружколомания в широких диапазонах режимов резания и упрочнения державки резца рекомендуется применять резец новой конструкции (рис. 13), состоящий из державки 5 с припаянной твердосплавной или закаленной подкладкой I, на которой помещается твердосплавная пластинка 2, закрепленная Г-образным рычагом-прижимом 4 и стружколомающим упором 3. При выборе в зависимости от режимов резания величины порожка а для дробления (ломания) стружки режущую пластинку 2 выдвинуть упором 6, который затем закрепить винтами 8. При установке и закреплении болтами резца в резцедержателе большое плечо б рычага-прижима поворачивается около оси винта 7, вследствие чего сжимается паз рычага на величину С, а короткое плечо со стружколомающим упором 3 прижимает пластинку 2 к подкладке 1 под действием сил упругости. Резец новой конструкции обладает достаточной жесткостью и надежным креплением режущей пластинки, обеспечивает устойчивое стружколомание в широких пределах режимов резания. Например, при ширине порожка а, равного 4 мм (х > 0,1 мм/об, и > 30 м/мин), стружколомаЮ1е обеспечивается на любых режимах резания.
[c.67]
Зубьями фрезы служат простые в изготовлении резцы с напаянными твердосплавными пластинами. Пазы в корпусе фрезы наклонены по отношению к оси на 10° это учитывают при заточке резцов и выборе их геометрии. Геометрию резцов и марку твердого сплава выбирают в зависимости от материала заготовки. При обработке чугуна к резцам напаивают пластину ВК8 и затачивают с углами у = +20° и а = 10°. После установки в корпус геометрия резца в процессе резания изменяется. Так как паз под резец наклонен по отношению к образующей цилиндрической поверхности корпуса под углом 10°, то передний угол уменьшается до + 10°, а задний увеличивается до 20° (рис. 67, б). При обработке стали применяют резцы, оснащенные пластинами из твердого сплава Т15К6 или Т5КЮ, затачиваемые с углами y = 0° и а = 2°. После закрепления в корпусе получают углы у = —10° а = 12°, Резцы могут быть обычными, одинарными 3 или сдвоенными 4 с напаянными по концам двумя пластинами. Сдвоенные резцы можно переставлять в пазу, переворачивая, и тем самым вдвое увеличивать время их работы между переточками. Изменяя углы резцов в плане, можно фрезой обрабатывать не только открытые плоские поверхности, но и поверхности, расположенные около уступов.
[c.158]
Установка и закрепление резцов.
Приспособления для закрепления резцов. На закрепление резцов в различного тина резцедержателях строгальщику приходится затрачивать немало рабочего времени (табл. 10). Выбор конструкции резцедержателя или державки связан с характером обработки, размерами станка и обрабатываемой детали. Рациональная конструкция резцедержателя может содействовать повышению производительности труда строгальщика.
На рис. 74, а изображен прямой резцедержатель, в котором резец закрепляется тремя болтами, а на рис. 74, б – угловой (изогнутый), где инструмент закрепляется двумя болтами. Изогнутый резцедержатель предназначен для строгания канавок и подрезки уступов в труднодоступных местах.
Более универсальный резцедержатель, позволяющий «сворачивать инструмент на необходимый угол, показан на рис. 74,в. Здесь в корпусе 1 расположен поворотный держатель 2, в окне которого болтом 8 крепится резец 4. Держатель может быть повернут на любой угол. Следует отметить сравнительно невысокую жесткость крепления резца в этом резцедержателе, что позволяет использовать его только при легких строгальных работах.
На рис. 74,г представлен жесткий резцедержатель, применяемый при тяжелых работах. Здесь к корпусу 6 прижимается диск 4, поворачивающийся на необходимый угол вокруг оси 5. В нужном положении диск закрепляется гайкой 7. К нему крепится откидная планка 2, в которой с помощью двух болтов 1 закрепляется резец. При обратном ходе ползуна (или стола) планка 2 с резцом поворачивается вокруг оси 3, резец при этом приподнимается и не задевает за обрабатываемую деталь.
При строгании крупногабаритных деталей нередко возникает необходимость работы с большими вылетами резца. Б этих случаях обычно применяют державки чипа показанных на рис. 75. В державке, изображенной на рис. 75, б, крепятся два резца, что позволяет разделить весь припуск на обработку между двумя этими резцами, установленными на разную глубину резания. На рис, 75, в представлена державка, позволяющая устанавливать резец под углом 50°, что оказывается необходимым при строгании пазов типа «ласточкин хвост». Для сравнения на рис. 75, а приведена державка обычной конструкции.
Применение державок позволяет значительно уменьшить расход металла на изготовление резцов, которые в этом случае имеют малые размеры и весьма простую конструкцию.
При строгании с очень большими вылетами инструмента, а также при обработке небольших поверхностей в деталях значительной протяженности (например, шпоночного паза в длинном отверстии) используют резцы, закрепляемые в борштангах.
На рис. 76,а изображена борштанга жесткой конструкции, закрепляемая в супиорте вместо колодки резцедержателя. Борштанга усовершенствованной конструкции с откидной резцедержавкой, приподнимающей резец при обратном ходе, показана на рис. 76,б. Эта борштанга, как и предыдущая, крепится в суппорте вместо колодки резцедержателя. В пазу борштанги на оси 5 гайкой 8 через шайбу 7 закрепляется откидная резцедержавка 6, где винтом 2 крепится резец. В рабочем положении резцедержавка фиксируется пружиной 4, расположенной между крючками 8, при этом резец прижат к торцу паза, а на холостом ходу скользит по поверхности детали.
Одновременная установка нескольких резцов. При выполнении сложных строгательных операций приходится несколько раз производить замену резцов, на что затрачивается значительное время. Если же перед началом операции сразу установить в суппорте все резцы, необходимые для выполнения данной работы, то можно совершенно отказаться от их перестановки и сэкономить значительную часть вспомогательного времени.
Для обработки детали экскаватора на Уралмашзаводе требовались три различных резца, которые последовательно устанавливались в боковом суппорте станка. Строгальщик этого завода Н. И. Гусев вместо трех раб<лает двумя резцами. Перед началом операции он устанавливает инструмент в одном суппорте таким образом, чтобы не было необходимости в их смене в процессе обработки (рис. 77).
Сокращения затрат времени на установку резцов можно добиться и путем применения поворотных резцедержателей. На поворот резцедержателя времени затрачивается примерно в 10 – 15 раз меньше, чем на снятие и установку резца. Одна из конструкций поворотных резцедержателей, применяемых при работе на строгальных станках, приведена на рис. 78.
Применение комбинированных и фасадных резцов и многорезцовых блоков также дает возможность сократить вспомогательное время за счет уменьшения числа установок и смен резцов, а также сокращения затрат времени на установку инструмента, на размер и отвод его (более подробно об этом см. на стр. 266 – 269).
Приспособления для установки резцов на заданный размер. На рис. 79 показано простейшее приспособление, применяемое на Минском заводе автоматических линий для установки строгального резца на размер в пределах от 100 до 150 мм. Аналогичные приспособления могут быть изготовлены и для других диапазонов размеров.
На стойке 1 этого приспособления нанесены размеры в миллиметрах от основания до верхней площадки стойки. Выдвинув стойку 1 на нужный размер и закрепив ее винтом 8, устанавливают резец 2 по ее верхней площадке. Режущая кромка резца при этом будет установлена на нужный размер по высоте от поверхности стола станка.
На Московском станкостроительном заводе им, С. Орджоникидзе успешно применяется универсальный раздвижной шаблон для нахождения центра детали, а также для установки резцов на нужный размер при черновом строгании, при этом разметка деталей (типа станин, салазок, траверс и колонн) не требуется.
Шаблон (рис. 80) устанавливают в нишу станины, а клин 1 опускают вниз; в результате губки 2 раздвигаются до стенок детали, определяя ее центр – среднюю часть шаблона. Этот шаблон показывает также нужный размер для обрезки направляющих. Резцы в суппорте устанавливают по торцам шаблона, так как его ширина соответствует заданному чертежом размеру.
Применение шаблона позволило получить значительную экономию вспомогательного времени как благодаря устранению разметки деталей, так и за счет сокращения времени установки резцов на размер.
Приспособления для установки резцов на заданный угол. При строгании поверхностей, расположенных под некоторым углом к поверхности стола, возникает необходимость установки под соответствующим углом главкой режущей кромки резца, формирующей обрабатываемую наклонную поверхность. Эта задача решается с помощью специальных настроечных установок (эталонов), а также различных поворотных приспособлений тля установки резца.
На рис. 81 приведен применяемый на Минском заводе автоматических линий установ-эталон для установки резца на заданный угол. Он представляет собой прямоугольную призму, на двух боковых гранях которой под строго определенными углами расположены площадки. На каждой из них маркируется величина угла наклона относительно оснований призмы.
Перед обработкой фаски или другой наклонной поверхности резцы устанавливают режущей кромкой по соответствующей площадке уста нова, расположенного па столе станка. Резец устанавливают так, чтобы между его режущей кромкой и площадкой установа не было зазоров. Площадки расположены через каждые 5°. Точность выполнения угловых размеров уста нова равна 10°.
Такие установы-эталоны выполняются не только в виде прямоугольных призм, но и других форм: квадратными, ступенчатыми и пр. Как правило, они имеют стандартный набор ступенек (через 5 – 10°). Естественно, они могут быть использованы не во всех случаях обработки наклонных поверхностей; иногда их даже невозможно установить на базирующую поверхность – стол станка. В таких случаях установка резца на заданный угол осуществляется с помощью настроечных приспособлений, одно из которых показано на рис. 82.
Приспособление устанавливается на стол станка, в губки тисков или на деталь (для этого выворачивается винт 4). Если деталь большого размера и на столе нет. места для ее установки, то приспособление располагают на штангенрейсмасе (для этого в стойке приспособления предусмотрены прямоугольные окна) и крепят винтом 4. Ио вертикальной стойке приспособление поднимают на нужную высоту. Для обработки фаски или наклонной поверхности режущая кромка резца 6 устанавливается на необходимый угол по установочной плоскости плиты 1. Точность установки проверяется щупом 0,03 мм. Необходимый угол задается путем поворота плиты вокруг оси 2 до совпадения диска с делением градуированной шкалы на стойке 3. Нужное положение фиксируется гайкой 5.
Приспособление достаточно универсально. С его помощью можно устанавливать на любой заданный угол резцы, закрепленные не только в суппортах поперечины, но и в боковом суппорте.
Приспособления для подъема резцов. Как уже указывалось, применение твердосплавных резцов при строгании часто связано с выкрашиванием их режущей кромки. Это явление наблюдается не столько при рабочем ходе – в момент врезания резца с ударом в заготовку, сколько при обратном ходе, когда задняя поверхность резца скользит по обработанной поверхности детали. В целях устранения этого недостатка строгальщики-новаторы используют специальные устройства, автоматически поднимающие резец при обратном ходе.
Таким простейшим устройством является широко распространенный скребок-подъемник (рис. 83) . Он имеет пластину 1, к которой прикреплена на шарнире вторая пластина-створка 2. Пластина 1 устанавливается в резцедержателе под резцом. Створка 2 расположена ниже вершины резца и при рабочем ходе свободно откидывается назад. В конце рабочего хода створка принимает вертикальное положение, а при обратном ходе упирается в деталь и поднимает резец, не давая ему соприкасаться с обработанной поверхностью. Применение этого несложного приспособления хотя и дает возможность устранить выкрашивание твердосплавного резца, однако имеет ряд недостатков.
На рис. 84 показано приспособление более совершенной конструкции, внедренное новаторами Минского станкостроительного завода им. С. М, Кирова. Оно состоит из корпуса 1, прижимной планки с болтами, закрепляющими резец 2, и двух щек 4 с роликом 5, внутри которого на оси 8 насажен шарикоподшипник 6. От осевого смещения шарикоподшипник удерживается распорными втулками 7.
При рабочем ходе резца в момент врезания его в деталь ролик Б откидывается и проходит над деталью, не касаясь ее. По окончании рабочего хода ролик падает вниз к резцу. При движении стола в обратном направлении он упирается в деталь и, поднимая резец с резцедержателем над деталью, катится по ней. Затем ролик соскакивает с детали, и резец становится в рабочее положение.
Для регулировки установки ролика на нужную высоту относительно резца (во избежание удара режущей кромки о деталь в конце холостого хода) в корпусе или в державке просверлено несколько отверстий для винта, являющегося осью качания щек.
При строгании длинными резцами настройка приспособления осуществляется так, как показано на рис. 84. При обработке короткими резцами, установленными в державке, щеки 4 вместе с роликом в сборе крепятся непосредственно к державке винтом 8. На верхней части суппорта устанавливается кронштейн с роликом и противовесом, который смягчает удар резцедержателя при окончании обратного хода.
При работе на тяжелых продольно-строгальных станках подъем резца или колодки резцедержателя с инструментом на сравнительно небольшой угол оказывается недостаточным, поэтому в ряде случаев используют механизированные подъемники.
На крупных продольно-строгальных станках, применяют механизированные устройства для подъема колодки резцедержателя на угол 45 – 75° с помощью пневмопривода.
Приспособление для установки токарного резца
Приспособление для установки токарного резца относится к оснастке токарных станков и может быть использовано для точной установки токарного резца по линии центров токарного станка любого типоразмера с помощью набора подкладок разной толщины. Известен способ установки токарного резца по вершине заднего или переднего центров токарного станка, являющийся приблизительным и не отвечающим техническим требованиям подготовки токарного станка к эксплуатации.
Известно приспособление для настройки и установки резца (RU 709257 A1, B23B 25/06, 15.01.1980 /Д1/), выбранное в качестве прототипа. Приспособление содержит элементы базирования с пазом под резец, в котором выполнены отверстия с резьбой для установки упомянутых элементов регулирования и введенных в приспособление элементов предварительного фиксирования и крепления резца. Настройка и установка резца может быть выполнены при наличии специального оптического прибора. Конструкция приспособления сложная, имеет ограниченный диапазон применения для револьверной головки металлообрабатывающего станка. Отличительной особенностью предлагаемого приспособления для установки токарного резца по линии центров токарного станка с помощью набора подкладок разной толщины является простота конструкции и изготовления, охват всего диапазона типоразмеров токарных станков, простота применения. Технической задачей предлагаемого приспособления для установки токарного резца является обеспечение точной установки токарного резца по линии центров токарного станка с применением набора подкладок разной толщины, устанавливаемых под резец на верхней плоскости пластины для размещения токарного резца, с последующим переносом, установкой и креплением резца с подкладками на основании резцовых площадок резцедержателя.
Технический результат достигается предлагаемым приспособлением для установки токарного резца по линии центров токарного станка с применением набора подкладок разной толщины, устанавливаемых под резец на верхней плоскости пластины для размещения токарного резца с последующим переносом, установкой и креплением резца с подкладками на основании резцовых площадок резцедержателя.
Конструкция приспособления поясняется эскизами на фиг. 1. Приспособление для установки токарного резца по линии центров токарного станка состоит из пластины для размещения токарного резца 1, на левом конце которой размещены вертикально устанавливаемая втулка 2 с установочным диском 3, прочно закрепляемые к упомянутой пластине 1 болтом 4. Пластина для размещения токарного резца 1 представляет собою плоскую деталь, длина и ширина которой позволяют нормально установить каждый типоразмер применяемых для токарного станка резцов. Вертикально устанавливаемая втулка 2 и нижняя плоскость установочного диска 3 соответствуют высоте Н, равной размеру от основания резцовых площадок 10 резцедержателя 11 до линии центров токарного станка 12. Определяется этот размер микрометром 13 от нижнего основания закрепляемой в резцедержателе технологической пластины 9 до верхней касательной проточенного для этой цели технологического цилиндра Д, минус диаметра проточенного технологического цилиндра (H=P-1/2Д). Технологическая пластина 9 и проточенный технологический цилиндр Д для определения размера Н перед замером размещаются в одной вертикальной плоскости (нижний эскиз фиг. 1). Диаметр установочного диска 3 целесообразно выполнить не менее ширины пластины для размещения токарного резца 1, нижнюю поверхность установочного диска шлифовать, для повышения износостойкости установочный диск 3 калить до твердости HRC 58-62. Точная установка токарного резца 5 в приспособлении для установки токарного резца достигается с помощью набора необходимых подкладок разной толщины 6, устанавливаемых под токарным резцом 5 на верхней плоскости пластины для установки токарного резца 1 до ощутимого соприкосновения вершины резца 8 с нижней плоскостью установочного диска 3. После завершения набора подкладок 6 под токарный резец 5 в приспособлении для установки токарного резца, устанавливаемый токарный резец 5 вместе с набором подкладок 6 переносится и ставится в нужном положении на резцовой площадке резцедержателя, надежно крепится болтами, после чего токарный станок готов для выполнения требуемых операций. Длина и ширина подкладок 6 должна соответствовать габаритам основания токарного резца 5. Приспособление представляет собою универсальную конструкцию и может переналаживаться для различных типоразмеров токарных станков изменением высоты вертикально устанавливаемой втулки 2. Наиболее удобным местом размещения приспособления для установки токарного резца может быть верхняя площадка коробки скоростей токарного станка 7. Материалами для изготовления деталей приспособления являются металлические стандартные полосы или нарезанные полосы металлических листов разной толщины, стальной круг.
Резцедержатели
Скачать каталогРезцедержатель представляет собой узел токарного станка, который предназначен для крепления режущего инструмента. От его точности в значительной мере зависит качество обработки детали.
Поэтому было разработано несколько вариантов конструкции этого устройства, подходящие для разных условий. Помимо токарных станков, резцедержатели используются в строгальных и некоторых других металлорежущих станках, но там они имеют другую конструкцию.
Условное деление
По исполнению:
– с осью вращения
– со сменными блоками
Деление резцедержателей с осью вращения:
– с горизонтальной осью вращения (параллельно оси шпинделя)
-с вертикальной осью вращения (перпендикулярно оси шпинделя)
по источнику смены позиций:
– механические (вручную) – электромеханические
– гидравлические
– серво
По креплению инструмента
– клиновым блоком – резцы 16х16, 20х20, 25х25 и 32х25 мм
– VDI – крепление в круглом отверстии позиции торцевой поверхности диска резцедержателя одним болтом с клином. направление оси Чаще всего используются VDI30, VDI40. Размеры VDI20, VDI50 и VDI60 используются относительно редко. Может использоваться для статичного и приводного инструмента
– BMT – крепление в круглом отверстии на периферийном диаметре диска резцедержателя. Крепление четырьмя болтами. Наиболее распространены BMT-45, BMT-55, реже используются BMT-65, BMT-75. Может использоваться для статичного и приводного инструмента
На универсальном токарном станке резцедержатель располагается на верхних салазках суппорта. На суппорте также размещаются поперечные и поворотные салазки, а сам суппорт находится на продольных салазках станины. Комбинация этих узлов позволяет перемещать резец по всем трем координатам и поворачивать относительно продольной оси, что и обеспечивает большое количество доступных операций универсальному токарному станку.
У тяжелых обдирочных станков конструкция суппорта несколько отличается, поскольку на него приходится значительная нагрузка. В таких станках резцедержатель располагается на дополнительных салазках. Это требуется по той причине, что у станков этого типа поперечные салазки имеют слишком массивную конструкцию и их перемещение вручную затруднительно.
Использование резцедержателя
Резцедержатель является отдельным узлом станка, закрепленным болтами. Он существенно облегчает обработку деталей. Особенно важно применение резцедержателя при точной расточке отверстий. Конструкции резцедержателей отличаются высокой прочностью и надежностью, поскольку даже от небольшого люфта точность обработки может значительно снизиться.
Токарный резцедержатель предназначается для размещения резца по высоте и в горизонтальной плоскости. Установка резцедержателя по высоте имеет большое значение для процесса обработки. Если выполняется обточка, то резец устанавливается так, чтобы режущая кромка инструмента была выше, чем линия центров станка. Для расточки резец размещается ниже линии центров.
Простой резцедержатель
Самую простую конструкцию имеет резцедержатель, называемый «солдатиком». Это устройство имеет сферическую подкладку, которая позволяет быстро закрепить резец. Путем поворота сферической прокладки регулируется угол резки и положение по высоте. Закрепление резца выполняется при помощи одного болта.
С одной стороны, это устройство резцедержателя токарного станка дает возможность установить резец за минимальное время, а с другой — вся нагрузка приходится на один болт, поэтому он должен быть плотно затянут. Однако, пытаясь обеспечить достаточный прижим, этот болт часто затягивается с избыточным усилием, отчего резьба быстро приходит в негодность. В результате происходит обрыв болта или срезание внутренней резьбы. Ремонт такого резцедержателя заключается в замене болтов и расточке отверстия на больший размер. Также возможна установка втулки с резьбой в отверстие. Для повышения стойкости болтов их изготавливают из прочных сталей, таких как 12ХН3А, подвергают цементации на глубину 0,6-0,8 мм и закалке, что позволяет добиться твердости поверхности 50-60 HRС. Благодаря этому стойкость болтов возрастает в 10-15 раз относительно сырых, изготовленных из стали 45, однако, повышается и их цена. Для большей части деталей резцедержателя используется сталь 45, у которой твердость находится в интервале 220—260 НВ.
Резцедержатель этой конструкции широко использовался на советских станках. Сейчас такая конструкция резцедержателя токарного станка считается устаревшей и используется только для некоторых легких станков. В этом резцедержателе можно закрепить только один инструмент, что требует частой замены резца. В промышленной металлообработке это приводит к большим потерям времени.
Поворотные резцедержатели
Большое распространение получил кассетный резцедержатель для токарного станка, в котором можно одновременно закрепить четыре инструмента. Таким образом можно подготовить станок к четырем последовательным операциям без смены инструмента. Наибольший эффект от этого резцедержателя достигается при обработке деталей сложных форм.
Резцедержатель имеет строение, сходное с револьвером. Главным элементом является крупный диск, в котором просверлены сквозные отверстия на равном расстоянии друг от друга. В отверстия вставляются разрезные втулки, в которые и крепятся резцы. Использование втулок позволяет установить резцы по высоте без использования прокладок, поэтому такая операция выполняется весьма быстро. Также устройство для фиксации резцов имеет жесткие пружинные державки, что дает возможность вести растачивание глубоких отверстий, нарезание внутренней резьбы и другие точные работы.
В современных станках используются еще более эффективные резцедержатели, в которых одновременно можно закрепить до 12 инструментов. Особенно эффективны такие резцедержатели для токарных станков с ЧПУ, их применение позволяет значительно повысить производительность. Электромеханический привод резцедержателя обеспечивает быстрое и надежное крепление инструмента.
У Р О К 30=31
У Р О К И 30—31
Отрезание заготовок и вытачивание канавок
Цель.
· Познакомить учащихся с правилами и при- емами отрезания заготовок и вытачивания канавок.
Оснащение. Токарно-винторезный станок, штан- генциркуль, резцы, заготовки изделий, технологи-
ческие карты, плакаты.
Объект и содержание работы. Практическая ра- бота. Отрезание и вытачивание канавок (винт для резцедержателя, болт, ось).
Новые понятия. Отрезание, отрезание вразгонку.
Методические рекомендации
При работе на токарно-винторезных станках особую сложность для учащихся представляет отрезание деталей. Нетвердое знание ими правил установки резца, характера и условий процесса отрезания достаточно часто приводит к поломке режущего инструмента. Поэтому, приступая к изложению теоретического материала, целесообразно задать учащимся вопросы по ранее пройденным темам:
1. Какие требования предъявляют к установке резца?
2. Применяют ли продольную подачу суппорта станка при точении канавок?
3. Каким образом закрепляют детали при обтачи- вании?
Затем следует показать возможные способы уста- новки резца, обратив внимание на вопросы:
1. Изменится ли величина переднего и заднего углов при установке резца выше или ниже линии центров?
2. К каким последствиям приведет такая установка?
После объяснений учителя и демонстрации им различных положений резца в резцедержателе учащиеся должны понять, что правильной является такая установка резца, когда его главная режущая кромка находится на линии центров. Если резец установить выше линии центров, то передний угол увеличивается (что ухудшает сход стружки), а углы резания и задний угол уменьшаются. Уменьшение заднего угла приводит к усилению трения зад- ней поверхности резца о заготовку и его преждевре- менному износу. Если резец установить ниже линии центров станка, то передний угол уменьшается, а углы резания и задний угол увеличиваются. В этом случае ухудшаются условия резания, под давлением стружки происходят выкрашивание режущей кромки и поломка резца.
Отрезной резец следует устанавливать строго пер- пендикулярно к оси заготовки, чтобы боковые по- верхности его головки не соприкасались со стенками прорезаемой канавки. Боковые поверхности отрез- ных резцов должны иметь угол поднутрения в пре- делах 1—20° (рис. 2). При отрезании заготовок мо- жет возникнуть вибрация, как правило, приводящая к поломке резца. Чтобы резец во время работы
не вибрировал, его вылет должен быть минимальным.
Кроме того, необходимо определить оптимальное расстояние от кулачков патрона до резца. Оно должно быть минимальным. Производить отрезание при большом вылете заготовки из патрона не следует.
Для отрезания заготовок используют несколько способов.
Первый способ — плавное перемещение резца от наружного диаметра к центру заготовки только по- перечной подачей. В этом случае надо переместить
Рис. 2. Отрезной резец
Рис. 3. Отрезание заготовки перемещением резца от наружного диаметра к центру заготовки поперечной подачей
Рис. 4. Отрезание заготовки подачей резца вразбивку
отрезной резец 2 (рис. 3) правой вершиной головки от торца заготовки на заданную длину и ручной по- перечной подачей отрезать заготовку 1.
Второй способ — использование поперечной и продольной подач резца вразбивку. Для этого надо установить его в исходное рабочее положение и по- перечной подачей сделать врезание с последующим перемещением резца влево, затем опять врезание и перемещение резца вправо до левого торца заготовки и так до полного завершения операции (рис. 4).
Для отрезания заготовки необходимой длины так, чтобы не оставался стержень на ее торце, надо режу- щую кромку резца заточить под углом 5—10° относи- тельно оси заготовки (рис. 5). В этом случае правая вершина головки резца будет отрезать таким образом, что торец заготовки будет гладким. Оставшийся
Рис. 5. Отрезание заготовки с образованием гладкого торца
Рис. 6. Установка резца для вытачивания канавки по линейке и глубиномеру штангенциркуля
на торце прутка конический стержень следует подрезать поперечной подачей резца.
Канавки на деталях вытачивают отрезными и прорезными резцами. Сравнительно узкие канавки выполняют прорезными резцами за один проход. Форма и размеры режущей кромки резца должны соответствовать форме и размерам канавки.
Для вытачивания канавки шириной 3—4 мм пря- моугольного сечения на гладкой цилиндрической по- верхности необходимо установить резец на заданном расстоянии от торцевой поверхности по линейке или глубиномеру штангенциркуля (рис. 6). Для этого то- рец линейки или глубиномер штангенциркуля следует упереть в правую вершину головки прорезного резца и переместить ее влево согласно чертежу на необ- ходимый размер. Резец подавать по лимбу винта поперечной подачи на необходимую глубину канав- ки. Длина головки прорезного резца должна быть больше глубины канавки на 3—5 мм. Диаметр вну-
Рис. 7. Измерение диаметра внутренней поверхности канавки
Рис. 8. Измерение глубины канавки штангенциркулем
Рис. 9. Определение положения правой и левой стенок канавки универсальным измерительным инструментом и по шаблону
тренней поверхности канавки можно измерить длин- ными губками штангенциркуля (рис. 7), а глубину канавки — глубиномером штангенциркуля (рис. 8).
Широкие канавки вытачивают за несколько про- ходов, положение правой и левой стенок канавки определяют с помощью универсального измеритель- ного инструмента или шаблона (рис. 9).
Для вытачивания такой канавки резец с правой стороны от торца заготовки надо установить стерж- нем глубиномера штангенциркуля. Подавать резец следует по лимбу винта поперечной подачи на глуби- ну в 2 раза меньше, чем указано на чертеже. Затем надо отвести резец на себя, в исходное положение, переместить его влево и установить левой вершиной головки с помощью глубиномера штангенциркуля или лимба винта продольной подачи на ширину ка- навки. После этого необходимо подать резец по лим- бу винта поперечной подачи на полную глубину ка- навки и, перемещая его слева направо, выполнить канавку согласно чертежу.
Особое внимание при подготовке занятий следует обратить на состояние резцов (заточка, закалка, ис- правность, состояние режущих кромок).
Целесообразно обучать учащихся освоению прие- мов отрезания деталей и вытачивания канавок в процессе выполнения практической работы. Перед ее выполнением необходимо показать и разъяснить основные приемы отрезания деталей и вытачивания канавок. Для этого надо правильно и прочно закре- пить заготовку в трехкулачковом патроне, закрепить отрезной резец по центру и установить необходимую частоту вращения шпинделя.
При выполнении операций отрезания детали и вытачивания канавки нужно плавно и равномерно вращать рукоятку поперечной подачи, так как не- равномерность подачи и даже небольшой рывок рез- ца могут привести к его поломке. Внимание учащих- ся следует обратить на завершающую стадию опера- ции. Здесь при неосторожном нажиме на резец его режущая кромка может легко сломаться.
После показа и объяснения приемов отрезания деталей и вытачивания канавок необходимо ознакомить учащихся с правилами техники безопасности при выполнении этих операций.
1. Заготовка и резец должны быть прочно закре- плены.
2. Нельзя оставлять ключ в патроне станка.
3. Во время работы резец надо перемещать плавно.
4. Нельзя подхватывать отрезанную деталь рукой.
5. После выключения станка нельзя тормозить вращение патрона руками.
6. Нельзя сдувать стружку со станка, ее надо уби- рать щеткой-сметкой.
При выполнении практической работы учащими- ся учитель наблюдает за их действиями, выявляет типичные ошибки, при необходимости показывает практически правильные приемы работы.
При подведении итогов занятия следует оценить работу каждого учащегося, тщательно проанализи- ровать наиболее типичные ошибки и указать пути их устранения.
Разработка открытого урока по теме “Токарно-винторезный станок. Приемы работы”
Цели урока:
- Ознакомить с эволюцией инструментов от простейших орудий до металлорежущих станков.
- Изучить устройство токарно-винторезного станка ТВ-4.
- Обучить приемам закрепления заготовки в патрон; резца в резцедержатель.
- Познакомить с приемами управления станком ТВ-4.
- Требовать соблюдения правил техники безопасности во время работы на станке.
Тип урока: комбинированный.
Оборудование и наглядность: класс по механической обработке металла укомплектованный токарно-винторезными станками ТВ-4 (по числу учащихся), кинематическая схема ТВ-4, плакат “Общее устройство металлорежущих станков”, плакат “Классификация станков”.
Материалы и инструменты: резцы, металлические заготовки, штангенциркуль, ключи для закрепления заготовки в патроне и резца в резцедержателе, щетка, молоток, фартук (по числу учащихся).
Формы организации работы: коллективная, самостоятельная.
Ход урока
I. Тема урока: “Устройство и назначение токарно-сверлильного станка”.
II. Прежде чем приступить к изучению нового материала, давайте с вами повторим материал предыдущего:
Дать понятие: орудие труда, инструмент и приспособление.
Орудие труда – инструменты, приспособления, станки, другие технические устройства, которыми воздействуют на материалы и заготовки с целью получения готовой продукции.
Инструмент – служит для обработки материалов, для монтажных работ.
- Как по назначению подразделяются инструменты? (Рабочие и контрольно-измерительные).
- Как различают инструменты в зависимости от источника энергии? (Ручные и механические).
- Как делят инструменты по назначению? (Режущие и ударные).
Приспособление – устройство для закрепления обрабатываемого материала или рабочего инструмента и создание условий по их взаимодействию.
Приведите пример развития приспособлений для сверления отверстий?
Как делятся металлорежущие станки в зависимости от вида обработки?
- Токарные.
- Сверлильные.
- Шлифовальные.
- Комбинированные.
- Фрезерные.
- Зубо- и резьбообрабатывающие.
- Строгальные.
- Разрезные.
- Разные.
III. Токарно-винторезный станок. Приемы работы.
Токарно-винторезный станок, так же как и сверлильный, прошел длительный путь развития: от примитивного приспособления с ручным приводом до современного токарно-винторезного станка с числовым программным обеспечением. Но если при эволюции сверлильного станка решалась задача обеспечить вращательного и поступательного движения сверла относительно заготовки, то в токарном станке эти движения были разделены – вращение заготовки и поступательное относительно ее движения резца. В примитивном приспособлении – прообразе токарного станка заготовку вращал один человек, а другой держал в руках резец и перемещал его во время обработки. Затем для вращения заготовки стали использовать лук, который приводился в действие ногой работающего. С изобретением суппорта приспособление для точения деталей превратилось в настоящий станок. Впервые станок с самоходным суппортом изготовил в начале 17 в. русский механик Андрей Нартов. Для вращения заготовки стали подводить механическую энергию от какого-либо общего двигателя: водяной мельницы, парового двигателя и т.д.
Дальнейшее развитие токарного станка шло по линии совершенствования механизмов, обеспечивающих вращение заготовки и перемещение резцов, взаимодействие этих движений, управление станком.
Токарно-винторезный станок ТВ-6 позволяет выполнять следующие основные операции: точение наружных и растачивание внутренних цилиндрических и конических поверхностей, подрезание торцов и уступов, отрезание заготовок, сверление отверстий и нарезание резьбы.
В токарно-винторезном станке различают: главное движение и движение подачи заготовки или инструмента. При токарной обработке главным движением является вращение заготовки, а движение подачи – поступательное перемещение резца. Главное движение передается следующим образом: двигатель – ременная передача – коробка скоростей – шпиндель патроном и заготовкой.
Движение подачи: двигатель – ременная передача – коробка скоростей – коробка подач – фартук – суппорт с резцом.
ТВ-4 состоит из станины, основания, коробки скоростей, коробки подач, фартука, гитары сменных колес, суппорта и задней бабки, ходового винта и ходового валика.
Литая чугунная станина коробчатой формы с окнами имеет по две призматические и плоские направляющие. Станина установлена на двух тумбах. Передняя бабка укреплена в левой части станка. Внутри ее расположена коробка скоростей, служащая для передачи вращательного движения от двигателя на шпиндель, ходовой валик и ходовой винт. В свою очередь шпиндель передает вращение заготовке при помощи трёхкулачкового патрона.
В коробке подач смонтированы механизмы, изменяющие скорость перемещения суппорта путем изменения частоты вращения ходового вала и ходового винта.
С помощью суппорта с фартуком производится продольное и поперечное вращение или подача резца. Ручное продольное перемещение осуществляется маховиком. Включение механизма подачи суппорта осуществляется включением рукоятки на себя. Перемещение резца в поперечном направлении выполняется также рукояткой.
Верхние салазки суппорта перемещаются в продольном направлении, поворачиваются на угол 40 градусов. Корпус задней бабки расположен на основании, которое перемещается по направляющим станинам. В корпусе движется пиколь, имеющая коническое отверстие, в которое вставляется упорный центр или режущий инструмент.
Зубчатые колеса коробки скоростей смазываются индустриальным маслом.
Техническая характеристика ТВ-4.
- Диаметр сквозного отверстия шпинделя: 16 мм.
- Диаметр отверстия установленного над станиной: 700 мм.
- Диаметр изделия установленного над суппортом: 80 мм.
- Частота вращения шпинделя: 130 – 170 мин.-1
- Шаг нарезаемой резьбы: 0,8; 1; 1,25 мм.
- Масса станка: 300 кг.
- Габаритные размеры станка: 1100 на 470 на 1100.
Какие операции по обработке металлов можно выполнять на ТВ-4? Из каких основных частей состоит ТВ-4? Назовите главное и вспомогательное движение на станке?
Резец – основной режущий инструмент для выполнения простейших операций по обработке металлов на токарно-винторезном станке. Он состоит из рабочей части, или готовки, и тела резца. В головке различают переднюю поверхность, по которой сходит стружка при резании, и две задние. Задняя поверхность, обращенная в поверхности резания, называется – главной задней поверхностью, вторая задняя поверхность – вспомогательной задней поверхностью.
Линия пересечения передних и задних поверхностей называются режущими кромками. Кромка, образованная передней и главной задней поверхностями, называется главной режущей кромкой. Образованная передней и вспомогательной задней поверхностями – вспомогательной режущей кромкой.
Точка пересечения главной и вспомогательной режущих кромок – вершина резца. Для работы резцом очень важны величины углов, образованными различными поверхностями его головки.
- Главный задний угол.
- Угол заострения.
- Угол резания.
- Передний угол.
Главный задний угол уменьшает трение между главной задней поверхностью головки резца и заготовкой. Передний угол улучшает процесс схода стружки. Задний и передний углы – это углы заточки резца.
По форме головок проходные резцы делятся на прямые и отогнутые.
По конструкции проходные резцы изготавливаются из одного стержня – это цельные, составные.
Из каких элементов состоит токарный резец? Что представляют собой проходные резцы и на какие виды они подразделяются? Из какого материала изготавливают резцы?
Управление ТВ-4 осуществляется с помощью рукоятки, маховиков и других органов управления.
Пуск и остановка станка осуществляется с помощью кнопок “Вперед”, “Назад”, “Стоп”. Кнопкой “Вперед” включают прямое вращение шпинделя, т.е. против часовой стрелки, если смотреть на него со стороны задней бабки. Кнопкой “Стоп” станок выключают.
Установка определенной частоты вращения шпинделя достигается поворотом рукояток коробок скоростей в положение.
Скорость перемещения суппорта, или величина механической подачи, устанавливается положением рукояток.
Перемещение резцедержателя с резцом вручную осуществляется рукояткой ручного перемещения верхних салазок суппорта, рукояткой перемещения поперечных салазок и маховиком ручной продольной подачи.
С действиями по управлению токарно-винторезным станком тесно связаны такие операции, как установка и закрепление на станке заготовок и режущих инструментов. С этих операций начинается любой вид токарной обработки.
Заготовку закрепляют на токарном станке различными способами в зависимости от характера обработки и ее размеров. Для выполнения простых токарных операций небольшие по размерам заготовки закрепляют в трёхкулачковом самоцентрирующем патроне. Для этого ключ патрона вставляют в одно из гнезд, разводят и вставляют заготовку после чего затягивают заготовку. Заготовка в патроне должна быть не менее чем 20-25 мм. Выступающая из патрона часть должна составлять не более 50-60 мм, иначе заготовка будет изгибаться во время работы.
После закрепления заготовки станок включают и проверяют не колеблется ли она, если она колеблется ее выравнивают с помощью молотка.
Для установки резца в резцедержателе нужно отвернуть торцевым ключом винты резцедержателя так, чтобы можно было свободно вставить резец. Устанавливают резец перпендикулярно к продольной оси заготовки. Это достигается следующими приемами. Если вершины центра и головки резца совпадают с центром панели, то резец установлен правильно. Затем прочно закрепляют резец винтами.
Как осуществить пуск и остановить станок? Как установить необходимую частоту вращения шпинделя? Как можно перемещать резцедержатель с резцом при неподвижном суппорте?
При работе на токарном станке необходимо соблюдать следующие требования правил безопасности:
- Включайте станок только с разрешения учителя.
- Перед началом работы проверьте исправность станка, заземление.
- Одежда должна быть застегнута на все пуговицы и не иметь свисающих частей.
- Во время работы прочно и надежно закрепляйте заготовку и режущий инструмент.
- Нельзя осматривать, трогать руками или измерять заготовку не выключив станка.
- Нельзя брать руками стружку, которая образуется во время работы.
- О всех неисправностях станка во время работы немедленно сообщайте учителю.
IV. Практическая работа.
В процессе выполнения практической работы вы должны проделать следующие операции:
- Включение и выключение станка.
- Вставление резца в резцедержатель.
- Закрепление заготовки в патроне.
- Торцевание заготовки.
- Разметка заготовки (длиной).
- Точение заготовки до диаметра 10 мм.
- Чистовая обработка.
Прежде чем приступить к практической работе я расскажу вам по каким критериям она будет оцениваться.
Критерии оценок:
- Качество обработанной детали.
- Точность соблюдения размеров по чертежу.
- Соблюдение ПТБ при работе.
- Самостоятельность в работе.
В процессе выполнения работы вы должны соблюдать правила техники безопасности и правильность проведения операций по закреплению и обработке заготовок.
V. Заключительная часть.
На сегодняшнем уроке мы с вами познакомились с устройством и назначением токарно-винторезного станка, провели практическую работу. В процессе работы обращалось внимание на качество обработки. Учащиеся производили разметку заготовок.
При подведении итогов был проведен общий анализ работы. Первый этап обучения приемам работы на станке прошел успешно.
Всем спасибо. До свидания!
Держатели инструментов 101: Cat, BT, HSK и др.
Держатели инструмента (державки) – это основная грань, которая соединяет станок с инструментами. Их способы монтажа различаются в зависимости от интерфейса. Их крепления могут варьироваться от держателей инструментов HSK, креплений VDI или устаревших стилей R8.
Все типы держателей инструмента состоят из 3 уникальных частей: гнезда цанги, фланца и конуса. Есть статический инструмент, на который не подается питание, и есть инструмент под напряжением (с приводом), на который не подается питание.
- Конус: Коническая часть резцедержателя имеет конусообразную форму. Это деталь, которая соединяется со шпинделем при смене инструмента.
- Фланец: Фланец подсоединяется к устройству автоматической смены, которое перемещает шпиндель и устройство смены инструмента.
- Гнездо цанги: Гнездо цанги обращено к различным гайкам цанги и является областью, в которой фиксируется вставка цанги.
Режущий инструмент (станок) окружен различными держателями, поэтому он остается неизменным в одном положении, в то время как многие другие обрабатывающие инструменты обеспечивают максимальный зазор для малых и больших размеров.
Типы держателей инструмента
Существует большое разнообразие типов инструментальных оправок, они индексируются в базах данных промышленного станка как таковые:
- Оправки станков: Они приводятся в действие двигателями и отвечают за токарный механизм обрабатывающих инструментов.
- Держатели для боковых резцов: Назначение этих оправок – удерживать режущие инструменты на месте.
- Держатели пильных полотен: Эти держатели удерживают пильные полотна на месте.
- Расточные головки: Они удерживают расточные оправки на местах, а также другие типы держателей инструмента.
- Патроны для нарезания резьбы: Они обеспечивают плавное нарезание резьбы, а также удерживают инструменты для нарезания резьбы на месте.
- Пустые адаптеры: В зависимости от задач обработки они могут быть адаптированы для различных приложений.
- Держатели концевых фрез: Эти держатели предназначены для фрезерования и удерживают фрезы на месте.
- Наружный диаметр (OD) и внутренний диаметр (ID): Это универсальные держатели, которые взаимозаменяемы со многими типами инструментов для резки.
- Цанговые патроны: Разнообразные цанговые патроны служат для удержания на месте различных инструментов.
- Патроны для фрезерования или сверления: Специально разработаны для размещения инструментов, связанных с сверлением и миллионами операций.
Когда вы пользуетесь держателями для инструментов, вы должны учитывать точный способ монтажа, который вам нужен.
R8 – это крепление старой школы, разработанное Бриджпортом еще в 1965 году. Эта деталь устарела и редко используется в современных станках.
Конус Морзе (MT) выпускается 4-х размеров. Дифференциал каждого размера имеет уникальный конус для облегчения переходных изменений в оснастке инструмента и использовании инструмента.
Национальные производители станков (NMTB) определили
Тип резцедержателя NMTB Taper был определен (NMBT) National Machine Tool Builders. Он используется во всех типах фрезерных станков и станков с ЧПУ. Базовое измерение требует дышла и составляет 3.5 дюймов на фут.
CAT ® от Caterpillar®, разработанная компанией Caterpillar® , индивидуальный тип крепления , в основном относится к V-образному фланцу. Это самый простой инструмент для станков Cat с ЧПУ. Все держатели инструментов, изготовленные и изготовленные Cat, имеют числовой идентификатор, связанный с размером конуса. (примеры CAT-30, CAT-40, CAT-50 и CAT-60.)
Подобно популярным инструментам Cat, это также держатели инструментов BT. Держатели BT отличаются от кошачьих, потому что все они симметричны и сбалансированы по оси вращения.Державки BT содержат те же стандарты размеров конуса, что и резьбы шпилек NMBT, которые используют метрики для перемещения.
Инструмент с полым хвостовиком (HSK) – это новая инновация в инструментальной оснастке, которая теперь используется и реализуется с различными типами станков HSM. Он изготовлен для быстрой смены инструмента, а также поставляется с прямым хвостовиком и с форматированием типа ласточкин хвост на станках.
Держатели инструмента: особенности и применение
Держатели инструментовпо характеристикам и применению сильно отличаются от держателей с открытым потоком охлаждающей жидкости через фланец или открытых компонентов.Такие модели, марки и производители (например, держатели инструментов Cat , держатели инструментов BT, держатели инструментов и HSK)
– каждый бит (без каламбура) лучших примеров для этого случая. Каждый из них различается по применению и взаимозаменяемым способностям адаптироваться к изменениям размера от маленького до большого с максимально возможным зазором. Важно понимать, что каждый изготовленный держатель инструмента адаптирован и настроен для своего конкретного назначения, задачи и работы.Это имеет огромное значение в эксплуатационной эффективности и эффективности использования.
Важность державок для точной обработки | ВВП
Важность державок в прецизионной обработке
GUHDO HSK63F Держатель инструмента, цанга, гайка цанги, фреза
Выбор и правильное использование держателя инструмента почти так же важны, как и сам выбор режущего инструмента. Держатель инструмента – это точка контакта между станком и самим инструментом, поэтому он является неотъемлемой частью целостности соединения со шпинделем станка.Важно, чтобы инструмент был правильно вставлен в цангу и вращался по траектории резания практически без биения. Гайки цанги на шарикоподшипниках помогают обеспечить надлежащий зажим цанги инструментом, чтобы избежать потери эффективности инструмента и любого возможного отклонения от источника зажима. Если вы столкнулись с биением или поломкой станка, одной из самых важных вещей, которые необходимо сделать, является повторная калибровка шпинделя с помощью оправки для биения.
Цанговый патрон, наиболее часто используемый в деревообработке, – это держатели инструмента HSK, состоящие из трех основных частей: собственно корпуса держателя инструмента, цанги и гайки цанги.В случае держателей инструментов ISO, SK и BT фиксирующая ручка (также называемая вытяжной шпилькой) является четвертой частью.
Держатель инструмента HSK
При смене инструмента важно установить инструмент в соответствующее приспособление для смены инструмента, чтобы должным образом закрепить держатель инструмента при установке / замене инструмента. Для затягивания гайки цанги следует использовать динамометрический ключ, поскольку чрезмерное или недостаточное затягивание может быть опасным для операторов механической обработки, а также отрицательно сказаться на инструменте и шпинделе из-за проскальзывания и вибрации, вызванных недостаточным равномерным сжатием на валу.
HSK63F Держатель инструмента с фрезой
При установке хвостовика инструмента в цангу важно, чтобы , по крайней мере, 3/4 дюйма цанги было заполнено хвостовиком инструмента, чтобы избежать дисбаланса, вибрации, риска соскальзывания инструмента и даже поломки инструмента. Важно убедиться, что спираль / режущая кромка не закрывается цанговым патроном, так как это может повредить кромку. Неправильно сбалансированный инструмент приведет к плохой отделке материала, а уделение пристального внимания точному зажиму инструмента увеличивает срок службы инструмента, снижает шум от станка и значительно снижает вероятность выхода из строя или повреждения шпинделя.В этом случае не забывайте, калибровочные оправки – отличные инструменты для поддержания вашего шпинделя в исправном состоянии после перемещения или поломки инструмента.
Держатель инструмента HSK63F и гайка цанги
Теги: ЧПУ, патрон с ЧПУ, цанга, резка, HSK 63 F, приспособление для наладки инструмента HSK, HSK63F, держатель инструмента hsk63f, маршрутизатор, фреза, инструмент, держатель инструмента, держатели инструмента, оснастка, инструменты, дерево, деревообработка
Вернуться на главную страницу блогаЭта запись была опубликована во вторник, 27 ноября 2012 г., в 20:04, и находится в разделах «Системы зажима», «Инструменты для маршрутизаторов с ЧПУ», «Общие записи в блоге».Вы можете следить за любыми ответами на эту запись через канал RSS 2.0. И комментарии и запросы в настоящий момент закрыты.
Принадлежности | AMMCO
- Модель #: 40111
- Номер детали: 940111
Преобразует 2800 в 2801.Переключатель блокировки, педаль хода и защитный экран. Токарный станок не может работать без присмотра с открытым капотом.
- Модель #: 40610
- Номер детали: 940610
Круглые, твердосплавные пластины, положительные грабли, 10 шт. В упаковке
- Модель #: 40609
- Номер детали: 940609
LH, положительный передний угол, для круглых – сверла No.40610
- Модель #: 40608
- Номер детали: 940608
RH, положительный передний угол, для круглого сверла No.40610
- Модель #: 40435
- Номер детали: 940435
Положительный рейк, 10шт., для токарных станков ACCUTURN (ACCUTURN – торговая марка ACCU INDUSTRIES, INC.)
- Модель #: 40430
- Номер детали: 940430
Отрицательный рейк, 10 шт., для токарных станков PERFORMANCE (PERFORMANCE – торговая марка PERFORMANCE EQUIPMENT CO., INC.)
- Модель #: 40425
- Номер детали: 940425
правый и левый, 3/8 дюйма
- Модель #: 40420
- Номер детали: 940420
Негатовские грабли, 10шт., для токарных станков HUNTER (HUNTER – торговая марка HUNTER ENGINEERING CO.)
- Модель #: 40415
- Номер детали: 940415
Положительный рейк, 10шт., для токарных станков KWIK-WAY (KWIK-WAY – торговая марка KWIK-WAY MANUFACTURING CO.)
- Модель #: 40410
- Номер детали: 940410
Положительный рейк, 10шт., для токарных станков FMC (JOHN BEAN CO. (правопреемник FMC CORPORATION) является дочерней компанией SNAP-ON-TOOLS, INC. и товарным знаком той же компании)
- Модель # 25969
- Номер детали: 925969
Положительный рейк (6918 или 7681) – левый – для моделей 3850
- Модель # 25968
- Номер детали: 925968
Положительный рейк (6918 или 7681) – правая – для моделей 3850
- Модель #: 40630
- Номер детали: 940630
Правая и левая, положительный передний угол, для круглых – сверло No.40610
- Модель #: 41201
- Номер детали: 941201
Левая и правая положительные грабли, для расточной оправки с двумя резцами0, в комплекте 2 шт.1 Биты со стопорными винтами
- Модель #: 2801
- Номер детали:
- 1
Экологичный корпус токарного станка Deluxe (ELE).В комплекте 940111. Токарный станок не может работать без присмотра с открытым капотом.
- Номер модели: 2800
- Номер детали:
- 0
Защитный кожух токарного станка (ELE).Меньше пыли в воздухе. Более чистые полы. Более тихий магазин. Добавлена безопасность и удобство.
- Модель # 5722
- Номер детали:2
Для гаек диаметром 1 7/8 дюйма и 2 1/2 дюйма
- Модель #: 3218
- Номер детали:
- 8
5/16 “x 3/8” – стандартно с моделями 1000, 3000, 3850, 4000, 4100, 7000, 7700
- Номер модели: 3022
- Номер детали:
2
1 1/4 “x 1 1/16” – стандартно с моделями 1000, 3000, 3850, 4000, 4100, 7000, 7700
- Модель #: 10651GP
- Номер детали:
1GP
Для резака № 6950 Twin Cutter
- Модель #: 10650GP
- Номер детали:
0GP
Для # 6950 Twin Cutter
- Модель #: 8899
- Номер детали:9
Для двухрезальных машин 6900 и 6950
- Модель # 7900
- Номер детали:0
с независимыми расточными оправками – для Lg.Роторы и маховики со ступицей с фланцами
- Модель #: 7750
- Номер детали:0
Преобразует модель 3000 или 7700 в барабанные / дисковые токарные станки
Руководство по эксплуатации | MITSUBISHI MATERIALS CORPORATION
Пластина с наклонной режущей кромкой
Держатель типа BAP3500-A для вставки R с малым носиком (89.76 КБ) Держатель типа BAP3500-B для пластины R с большим носом (98,36 KB) Высокоэффективная обработка чугуна
FBP415 (86,09 КБ) Концевая фреза со сменным шарниром для чистовой обработки
RM (89,31 КБ) Головка сменная
Концевые фрезы iMX Как установить головку (474.65 КБ) Концевые фрезы iMX Как наносить противозадирную смазку (1,45 MB) Пластина общего назначения с саморезом Торцевая фреза
ASX445 (111,44 КБ) Универсальная многоугольная пластина Торцевая фреза
AHX640S (91,51 КБ) Высокоэффективная обработка чугуна
AHX640W (172.04 КБ) AOX445 (436,99 КБ) Для общей резки
SE415, SE515, SE445, SE545 (370,85 КБ) Фреза с прочной кромкой для чугуна
VOX400 (92,05 КБ) Пластина с саморезом, фреза для уступа
ASX400 (118.74 КБ) Многофункциональная фреза со сменными пластинами
APX3000 оправки (ДЮЙМ) (39,62 КБ) APX3000 с хвостовиком (ДЮЙМ) (40,85 КБ) APX3000 оправка (мм) (79,96 КБ) APX3000 тип хвостовика (мм) (109,88 KB) APX3000 с резьбой (мм) (43.33 КБ) APX3000 с длинной режущей кромкой (127,62 КБ) APX4000 оправки (ДЮЙМ) (63,87 КБ) APX4000 с хвостовиком (ДЮЙМ) (60,41 КБ) APX4000 Концевая фреза с длинной кромкой (ДЮЙМ) (70,48 КБ) APX4000 оправка (мм) (98,36 KB) APX4000 тип хвостовика (мм) (88.98 КБ) APX4000 Концевая фреза с длинной кромкой и обечайкой (мм) (71,19 КБ) Для обработки алюминия и титановых сплавов
AXD4000 оправки (ДЮЙМОВ) (79,94 КБ) Тип хвостовика AXD4000 (ДЮЙМ) (86,68 КБ) AXD4000 оправка (мм) (162,15 KB) AXD4000 тип хвостовика (мм) (86.57 КБ) AXD4000A оправки (ДЮЙМОВ) (179,11 КБ) AXD4000A оправка (мм) (213,89 KB) AXD7000 оправки (ДЮЙМ) (93,64 КБ) Тип хвостовика AXD7000 (ДЮЙМ) (118,02 КБ) AXD7000 оправка (мм) (98,25 КБ) AXD7000 тип хвостовика (мм) (80.38 КБ) Тип AXD7000 HSK (мм) (42,87 КБ) Для алюминия и труднообрабатываемых материалов
BXD4000 type (INCH) (55,44 КБ) BXD (мм) (88,93 КБ) Многофункциональная концевая фреза со сменными пластинами
AQXU (ДЮЙМ) (111.01 КБ) AQX (мм) (113,01 КБ) Фреза с большим радиусом подачи
WJX14 Фреза малого диаметра со встроенным набором болтов (260,60 КБ) AJX (ДЮЙМ) (138,08 КБ) AJX (мм) (79,62 КБ) Концевая фреза с радиусом малого диаметра
Концевая фреза с радиусом ARX (133.07 КБ) Точки зажима фрезы
BRP, OCTACUT, BOE, PMF (44,10 КБ) Концевая фреза со сменными пластинами для глубокого фрезерования уступов
SPX (мм) (60,47 КБ) SPX Концевая фреза с раковиной (ДЮЙМ) (70,79 КБ) SPX Концевая фреза с корпусом (мм) (73.52 КБ) Для фрезерования титанового сплава
ASPX (ДЮЙМ) (117,19 КБ) ASPX (мм) (145,16 КБ) VFX5 (ДЮЙМ) (156,46 КБ) VFX5 (мм) (156,14 КБ) VFX6 (ДЮЙМ) (158,53 КБ) VFX6 (мм) (157.55 КБ) Концевая фреза со сменным шарниром для чистовой обработки
SRF (106,47 КБ) Концевая фреза с шаровой головкой для черновой обработки металлических форм
SRM2 (ДЮЙМ) (43,68 КБ) SRM2 (мм) (46,27 КБ) Концевая фреза со сменными пластинами для подрезания
PMC (59.83 КБ) Фрезерование с вертикальной подачей
PMR (73,35 КБ) ВИНТ модульной инструментальной системы в инструменте
ВИНТ В ИНСТРУМЕНТЕ (117,71 КБ) Торцевая фреза для высокоскоростной чистовой обработки алюминиевого сплава
V10000 (247,02 КБ) Уведомление о безопасности для V10000 (72.35 КБ) Фреза для чистовой обработки алюминиевого сплава и чугуна
NF10000 (226,98 КБ) Фреза для чистовой обработки алюминиевых сплавов с высокой подачей
FMAX (197,61 КБ) Сбалансированные уравнения: вибрация державки затрудняет обработку, но балансировка может помочь
Недавно я дважды установил в гостиной новый потолочный вентилятор.Задача была в моем списке дел в течение нескольких недель, и к этому моменту она заключалась в установке вентилятора или выкалывании сорняков. Конечно, я проигнорировал предложение жены сначала прочитать инструкцию. «Это всего лишь несколько проводов, дорогая, – сказал я ей. “Не о чем беспокоиться.”
Работа выполнена, лестница надежно уложена в гараж, я установил высокую мощность вентилятора и щелкнул выключателем. Боже, как я был рад, что этот остался позади. Затем я услышал громкий WONK-WONK-WONK… CRASH! Потолочный вентилятор сорвался с крепления и покатился в журнальный столик.Только тогда я заметил небольшой пакет балансировочных грузов в нижней части вентиляторного бокса.
Предоставлено Haimer USA
Лазер определяет положение балансировочных колец на держателе инструмента, чтобы сместить вес и исправить дисбаланс балансировочного станка Haimer TD-2009.
Полезный совет жены все еще звенел у меня в ушах, и я поехал в строительный магазин за еще одним комплектом вентилятора, все время размышляя о важности баланса. Реактивные двигатели, ветряные турбины, автомобильные колеса и даже потолочные вентиляторы – практически любой вращающийся механический компонент – должны быть сбалансированы.Это, безусловно, верно для обрабатывающих центров.
В качестве доказательства загрузите крупную товарную оправку – несбалансированный кусок стали весом несколько фунтов или более – в шпиндель станка и, если возможно, проверните его до 15 000 об / мин. Этот низкий гул – это крик веретена о помощи. Майкл Минтон, национальный менеджер по разработке приложений в компании Methods Machine Tools Inc., Садбери, штат Массачусетс, сказал, что несбалансированные резцедержатели вызывают чрезмерный нагрев подшипников шпинделя, что, наряду с вибрацией, может вызвать преждевременный выход шпинделя из строя.Большое биение несбалансированного держателя также снижает производительность резки.
Проблемы с производительностью могут включать перемещение державки в конусе шпинделя, что приводит к преждевременному износу и поломке инструмента. Часто встречаются проблемы с вибрацией и чистотой поверхности, а также ошибки геометрического допуска, вызванные биением инструмента. В результате, по словам Минтона, операторы, столкнувшиеся со снижением производительности резания из-за несбалансированных державок, снижают скорость подачи и скорость шпинделя, пытаясь решить проблему, которую они не могут контролировать.Проще говоря, несбалансированные державки не только вредны для станка, но и ухудшают чистую прибыль.
Но когда действительно нужна балансировка? Многие в отрасли считают, что только те цеха, которые работают с экстремальными скоростями шпинделя, нуждаются в этих модных и дорогих балансируемых державках и даже более дорогом балансировочном станке, чтобы они продолжали гудеть. Тем не менее Боб Руссо, национальный менеджер по продажам инструментов и принадлежностей компании Methods, рекомендует всего 9000 об / мин в качестве отправной точки, при которой балансировка становится важной – относительно стабильная скорость во многих магазинах.
Гайки и болты балансировочные
Поговорите со специалистом по балансировке, и вам будет представлен ряд сложных уравнений, использующих такие значения, как масса ротора и дисбаланса, угловая скорость и смещение центра масс. Комбинация этих значений в конечном итоге определяет качество балансировки держателя инструмента или значение G. Чем выше число, тем хуже разбалансировка при заданной скорости. Следовательно, инструмент со сплавом G2.5 вращается лучше, чем инструмент, сбалансированный с G6.3.
Вы также услышите несколько эзотерических слов – пара, статика и динамика, – которые описывают различные способы, которыми вращающиеся тела испытывают дисбаланс.Если спустило колесо во время движения по межштатной автомагистрали, ваше колесо теперь страдает статическим дисбалансом (слишком большой вес с одной стороны). Согните гребной винт на рыболовном судне, и вы почувствуете динамический дисбаланс – избыточный вес на двух или более точках – на всем пути к берегу. А слишком большой вес на противоположных лопастях вашего потолочного вентилятора приводит к дисбалансу пары.
Предоставлено Schunk
Операция скругления углов алюминиевой заготовки с использованием сбалансированного державки Tendo от Schunk.
Предоставлено Schunk
Высокоскоростное фрезерование алюминия с компактным гидравлическим держателем Tendo E от Schunk.
Чем больше добавлен вес или чем быстрее что-то вращается, тем больше дисбаланс, независимо от значения G державки. Центробежная сила увеличивается пропорционально квадрату скорости вращения, поэтому, когда шпиндель набирает обороты, вибрация увеличивается в геометрической прогрессии.
Например, головная боль из-за дисбаланса державки при 3000 об / мин будет в 25 раз хуже при 15000 об / мин.Вот почему цанговый патрон, рассчитанный на G2,5, может быть идеальным при 10 000 об / мин, но раскручивая тот же самый инструментальный узел до 50 000 об / мин, вы, вероятно, будете заняты покупкой новых подшипников шпинделя станка до конца месяца.
Как отмечалось ранее, дисбаланс инструментальной оправки влияет не только на станок. «Работа с несбалансированным державкой – это обработка, эквивалентная попытке написать письмо при движении со скоростью 60 миль в час по ухабистой дороге». Это по словам Уэса Стэнулиса, технического менеджера производителя инструментов MAPAL Inc., Городок Порт-Гурон, штат Мичиган,
Степень влияния вибрации на резание в несбалансированной ситуации во многом зависит от материала заготовки. В случае более мягких материалов, таких как алюминий, вибрация влияет на чистоту поверхности больше, чем на срок службы инструмента, как если бы во время землетрясения протаскивали острый нож по палочке с мягким маслом. Если масло застынет твердым, как сталь, этот вкусный молочный продукт будет менее восприимчив к вибрации, но режущий инструмент с большей вероятностью сломается или изнашивается преждевременно.
Сбалансированные мнения
Если отбросить все метафоры, это мутная вода, и у каждого производителя инструментов есть свой подход к приемлемым уровням дисбаланса державок. По словам Руссо, отраслевым стандартом является G2,5 при 15 000 об / мин. Для цеховой обработки 4130 отливок весь день при 3000 об / мин это явно перебор, в то время как производитель форм для жесткого фрезерования полостей при 35000 об / мин может счесть этот уровень баланса неприемлемым. Требуемый уровень зависит от ряда факторов, включая требования к допуску детали и чистоте поверхности, частоту вращения и качество шпинделя, скорость подачи и DOC, обрабатываемый материал и ожидаемый срок службы инструмента и шпинделя.
Добавьте в уравнение огромное разнообразие державок – от CAT и BT до HSK и горячей посадки – и и без того сложная ситуация станет поистине ошеломляющей. Например, почтенный держатель CAT 40 по своей природе неуравновешен из-за неровных пазов для дисководов. Держатели концевых фрез Weldon с большим установочным винтом на одной стороне тоже подходят. Станулис предположил, что магазинам, ищущим сбалансированную оправку, следовало бы упростить задачу. «Выбирайте оправки, в которых повторяемость зажимных механизмов меньше всего влияет на балансировку.Например, повторяемость хвостовика HSK с точки зрения баланса очень хорошая по сравнению с хвостовиками некоторых других распространенных инструментов. Чем меньше деталей в зажимном механизме, тем лучше. Державки с термической или горячей посадкой – хороший выбор, поскольку в них нет зажимных компонентов ».
Компания Schunk Inc. из Моррисвилля, Северная Каролина, производит инструменты, предлагающие сбалансированные на заводе держатели. «Мы продаем тонны гидравлических держателей. У них есть уплотнение, поршень и винт на одной стороне держателя, что вызывает дисбаланс », – сказал менеджер группы инструментов Мэтт Панош.«Чтобы компенсировать это, нам нужно удалить большое количество материала с противоположной стороны держателя. Однако, как только это будет сделано, держатели будут очень хорошо повторять ».
Тем не менее, многие в отрасли считают баланс как должное. «Сбалансированные державки стали настолько обычным явлением, что я даже забыл, что мы это делаем», – сказал Панош. «Единственный раз, когда я слышу о проблемах с балансом, это действительно высокая скорость, 40 000 об / мин и выше. Это связано с тем, что держатели, используемые в этой области, очень малы и их сложно сбалансировать – в них просто недостаточно массы, чтобы балансировочный станок мог обнаружить любую разницу в весе.”
Балансировочный станок является важной частью формулы балансировки державок как для мастерских, так и для инструментальных мастеров. Многие производители инструментов поставляют свои инструментальные оправки предварительно сбалансированными, что в случае с Schunk означает, что держатели станком сбалансированы до G2,5 при 25 000 об / мин. Однако, как только этот держатель инструмента попадет в цех, все ставки исчезнут – установите другой инструмент в этот держатель, и сборка в целом может оказаться более разбалансированной, чем мой двухлетний внук на скейтборде.
Панош согласился с тем, что сбалансированная сборка важна, но сделал следующее предостережение: «Это зависит от того, какие инструменты вы используете и что вы с ними делаете.Промышленность наводнена вертикальными фрезерными станками размером 20 дюймов на 40 дюймов, большинство из которых развивают максимальную скорость 12 000 об / мин или около того. На этих скоростях балансировка сборки не всегда необходима, если вы используете высококачественные сбалансированные державки и режущие инструменты ».
Хитрые вещи
Кто-то, кто может возразить против этого, – Брендт Холден, президент поставщика инструментов Haimer USA LLC, Вилла Парк, Иллинойс. «С механическими держателями, такими как фрезерные или цанговые патроны, сборка должна балансироваться каждый раз, когда вы меняете режущий инструмент», – сказал Холден.«Это потому, что эти типы держателей содержат движущиеся компоненты, которые не повторяются в точности во время зажима. Даже гидравлические патроны подвержены дисбалансу из-за изменения уровня жидкости во время зажима ».
Он также не согласен с 9000 об / мин и выше как с магическим числом для балансировки инструмента. «Мы работали с магазином, который купил балансировочный станок для их первого обрабатывающего центра с частотой вращения 20 000 об / мин. Владелец решил, что пока у них есть возможности, они могут также сбалансировать все в магазине.”
Результат, объяснил Холден, был удивительным. Даже на станках со шпинделем 8000 об / мин в цехе наблюдалось значительное повышение стойкости инструмента и качества поверхности за счет использования сбалансированных держателей. «Больше всего они были взволнованы увеличением съема металла», – сказал он. «Даже работая со скоростью 3000 об / мин, они смогли удвоить скорость подачи во многих своих операциях».
Холден признает, что это непростая тема. «Все смотрят на балансировку инструмента под другим углом. Никто не станет спорить, что это необходимо для высокопроизводительных приложений, таких как прецизионное изготовление пресс-форм, высокоскоростное трехмерное контурирование медицинских компонентов и многие аэрокосмические приложения.Но если задуматься, каждый цех – даже тот, который занимается повседневной обработкой, – хочет достичь рекомендованных скоростей и подач для всех своих инструментов. Проблема в том, что довольно часто операторы обнаруживают, что работа не выполняется должным образом при этих значениях, поэтому они снижают все до тех пор, пока не будет достигнута стабильная точка, где они могут обработать деталь надлежащим образом. Теперь они просто пожертвовали частью потенциала машины. Это реальное преимущество балансировки – она позволяет добиться максимальной производительности вашего оборудования.”
Дорогая недвижимость
Если вы хотите попробовать сбалансированные сборки инструмента, есть несколько вариантов. Вы можете нанять такую компанию, как Schunk, чтобы уравновесить их – Панош сказал, что компания взимает 50 долларов за штуку и может заменить держатели инструмента за несколько дней. Также доступны балансировочные станки. Например, Haimer предлагает машину на 33 фунта. Стоимость около 30 000 долларов, что, по утверждению Холдена, может сбалансировать практически любую оправку или сборку за считанные минуты.
Предоставлено Haimer USA
Уравновешиваемый цанговый патрон Haimer готовится к агрессивному резанию.
Том Чирино, технический менеджер компании Competitive Carbide Inc., производителя нестандартных инструментов и державок в Менторе, штат Огайо, сказал, что его балансир – самая дорогая машина на квадратный фут в магазине. Несмотря на его высокую стоимость, Cirino признал, что балансировка инструмента необходима при производстве специальных режущих инструментов, и субподряд не подходил для этого важного этапа. «У нас было несколько инструментов, сбалансированных снаружи», – сказал он. «Ожидание было слишком долгим, и иногда они выглядели довольно некрасиво из-за того, что весь металл был удален в процессе балансировки.”
Типичный процесс балансировки инструментов и державок часто начинается с проектирования. «Мы рассчитываем на то, что система CAD даст нам статический баланс», – сказал Чирино. «Это дает нам оценку. После этого мы должны выполнить динамическую балансировку в двух плоскостях с помощью балансировочного станка ».
БалансирCompetitive Carbide расположен рядом с 5-осевым обрабатывающим центром. Инструменты Virgin устанавливаются в балансировочный станок и вращаются со скоростью несколько сотен оборотов в минуту. Лазер «указывает» на зону дисбаланса, и на дисплее отображается количество материала, который нужно удалить.Затем инструмент обрабатывается соответствующим образом, и процесс повторяется до тех пор, пока не будет достигнута точная балансировка.
Предоставлено JM Performance Products
Высококачественная удерживающая ручка имеет решающее значение при использовании сбалансированных державок.
Не забудьте шпильку
Достижение баланса не всегда означает удаление металла. Некоторые державки снабжены просверленными и резьбовыми отверстиями для легкого увеличения веса там, где это необходимо, а некоторые поставщики инструментов предлагают балансировочные кольца, которые устанавливаются на державке и «набираются» в соответствии с информацией с балансировочного станка.Независимо от подхода, важно сбалансировать державку как единый узел. Сюда входит ручка удержания.
Эндрю Роули, президент JM Performance Products Inc., Фэйрпорт-Харбор, Огайо, сказал, что на это часто не обращают внимания. «Люди предполагают, что шпильки уравновешены, но на самом деле большинство из них даже не близко. По этой причине важно использовать высококачественную фиксирующую ручку и всегда включать ее в состав сбалансированной сборки ».
Предоставлено JM Performance Products
Разгрузка резьбы (область A) устраняет расширение на малом конце конической резцедержателя, обеспечивая правильную посадку и уменьшая вибрацию.
Роули указал на дополнительную проблему, вызывающую беспокойство у тех цехов, которые используют державки CAT или BT и которая усугубляет ситуацию дисбаланса, – это сам конус шпинделя. По его словам, на скоростях выше 10 000 об / мин шпиндели с длинным конусом имеют тенденцию «открываться», позволяя державке перемещаться в шпинделе. Что еще хуже, типичный вытяжной штифт, особенно тот, который был перетянут, может фактически деформировать резьбовой конец резцедержателя, вызывая неправильную посадку в шпинделе.
«Одна из мер, которые мы делаем для борьбы с этим, – это продвигаем резьбовую часть фиксирующей ручки как можно глубже в державку», – сказал Роули.«Это предотвращает появление раструба, который вы видите на многих из этих державок, и, в свою очередь, обеспечивает значительно больший контакт между державкой и конусом шпинделя. Также начинаем и останавливаем резьбу точно на 180 °. Это очень важно для поддержания должного баланса ».
Хотя балансировка державок звучит сложно и требует много времени, если вы хотите получить максимальную отдачу от своего оборудования, возможно, пришло время подумать о новом подходе. Это означает покупку предварительно сбалансированных держателей и станка для балансировки инструментальных сборок, даже если не работают так называемые «высокоскоростные» станки.А поскольку теперь вы являетесь счастливым обладателем балансировочного станка, пришло время научить и старших владельцев вращать верное устройство. Это может просто склонить чашу весов в вашу пользу. CTE
Об авторе: Кип Хэнсон (Kip Hanson) – редактор CTE. Свяжитесь с ним по электронной почте khanson@jwr.com.
Авторы
Competitive Carbide Inc.
(440) 350-9393
www.competitivecarbide.comHaimer USA LLC
(630) 833-1500
www.haimer-usa.comJM Performance Products Inc.
(800) 322-7750
www.jmperformanceproducts.comMAPAL Inc.
(810) 364-8020
www.mapal.usMethods Machine Tools Inc.
(877) 668-4262
www.methodsmachine.comSchunk Inc.
(919) 572-2705
www.us.schunk.comРезак для различных материалов для подложек | Fletcher’s FSC
Номер детали: 04-720
Нож для тяжелых условий эксплуатации со сменной платформой режущей головки, в которой используются несколько режущих лезвий, подрезные наконечники и держатели режущих дисков.Включает режущий инструмент с V-образной канавкой, используемый с материалом ACM, чтобы обеспечить методы гибки и изготовления. Резак обрабатывает листы материала высотой до 65 дюймов (1,65 м), оснащен лазерной визирной линией для резки предварительно напечатанной графики и оснащен режущей головкой с двумя рукоятками для управления и маневренности оператора. Устанавливается на стене или отдельно.
Технология сменной режущей головки
Режущие лезвия для ножей и отрезные круги производятся в соответствии с требованиями спецификации Fletcher:
- Повышенный срок службы и производительность резки
- Консистенция лезвия к лезвию
- Устранение «прогиба лезвия» при резке более твердых материалов
Алюминий
Композиты (ACM)до 4 мм
Держатель с колесами P / N # 04-771
Запасные колеса P / N # 05-223
Листы алюминия
до.063
Держатель с колесами P / N # 04-772
Запасные колеса P / N # 05-224
Гофрированный пластик,
ПВХ и пенопластдо 1/2 “
(13 мм)Держатель лезвия (1/2 “) P / N # 04-120
Держатель лезвия (1/4 “) P / N # 04-770
Сменные лезвия P / N # 05-222
Акрил / оргстекло
до 1/4 дюйма
(6 мм)Держатель P / N # 04-773
Запасной подрезной наконечник P / N # 05-712
Стекло / Зеркала
до 1/4 дюйма
(6 мм)Держатель P / N # 04-774
Запасные подрезные ролики P / N # 02-120
ACM
Инструмент для V-образной канавки
Держатель лезвия с V-образной канавкой и (2) лезвиями в комплекте P / N # 04-779
Запасной нож P / N # 05-233
Возможности резки различных материалов
- Алюминиевые композиты (ACM) до 4 мм
- Алюминиевые листы толщиной до.063 “
- Гофрированный пластик до 1/2 дюйма (13 мм)
- ПВХ и пенопласт до 1/2 дюйма (13 мм)
- Акрил / оргстекло толщиной до 6 мм
- Стекло / Зеркала до 6 мм
- МДФ до 3/32 дюйма (2,4 мм)
- Резка металла для печати на металле
Пакет покупки
Пакет закупок FSC (1) Блок FSC (настенный или отдельно стоящий) (1) Держатель лезвия 1/2 ” (1) Держатель отрезного круга ACM (1) Акриловый держатель лезвия (1) Тубус из 10 лезвий FSC (1) Трубка из 10 акриловых режущих пластин (1) Комплект алюминиевых композитных колес (1) Ящик для инструментов (2) Остановка производства материалов (1) Прицел Laser Line (1) Руководство Опции и сменные аксессуары
P / N Описание 04-770 Держатель лезвия 1/4 дюйма 04-772 Держатель колеса из алюминиевого листа с колесами 04-774 Держатель круга для резки стекла 02-120 Стальные колесные блоки со стеклом – 120 градусов 05-222 Лезвия FSC (10 на трубу) 05-223 Колеса ACM (2 / env) 05-224 Алюминиевые колеса (2 / env) 05-712 Лезвие для резки акрила / пластика (10 на трубку) (APB12) 04-779 Инструмент для V-образных канавок с лезвием Технические характеристики
- Горизонтальная экструзия: загрузка материала с левой стороны, оснащенная стальной износостойкой полосой, предназначенной для сохранения прямоугольности машины с течением времени.
- Система зажима материала: система зажима рычажного типа, которая фиксирует подложки высотой до 65 дюймов (165 см) для предотвращения коробления и смещения материала во время процесса резки.
- Зажимная система открывается на 5/8 дюйма (1,59 см), предотвращая повреждение предварительно напечатанного изображения ½ дюйма (13 мм) при загрузке. Режущая головка
- : оснащена двойной рукояткой для управления резкой жестких материалов.
Торговая и техническая документация
Изделие
РуководствоЛитература FSC
V-образная канавка
Держатель инструмента
ИнструкцииРежущая головка
Окончательная сборка
(серийный номер 927)Режущие инструменты
Номера деталейЗажимной рычаг
СборкаВертикальная направляющая /
Зажим в сбореРежущая головка
Окончательная сборка
(Серийный номер и ниже)Оптимизация вылета инструмента [Easy Guide + Bloopers! ]
Что такое вылет инструмента?Вылет инструмента – это расстояние от кончика инструмента до места, где хвостовик инструмента входит в патрон или цангу.Это один из ключевых параметров, который требует G-Wizard при настройке инструмента:
Ляпы для инструментаЯ смотрю изрядное количество видеороликов о механической обработке, когда я не занят созданием контента или написанием программного обеспечения для CNCCookbook. Удивительно, сколько «ляпов» вы видите, просматривая видео даже известных пользователей YouTube с ЧПУ. Вот лишь некоторые из тех, с которыми я столкнулся:
175000 просмотров; 51000 подписчиков. Вылет 7.6: 1 по диаметрам. Максимальная толщина среза с учетом предполагаемого вылета 1/3, что было бы лучше!
293000 просмотров, 5300 подписчиков. Вылет составляет 5,5: 1. Здесь опять же, учитывая максимальную глубину нарезки видео, выступ около 1/3 было бы намного лучше.
47000 просмотров, 68000 подписчиков. Вылет 6,4: 1. В этом видео он подошел гораздо ближе к тому, чтобы нуждаться в полном вылете, но все же мог подавиться на 2/3 этого большого вылета для лучших результатов.
Многие машинисты просто вставляют инструмент в держатель и уходят оттуда, не особо задумываясь о торможении, но вот некоторые серьезные побочные эффекты, когда у вас слишком большой вылет. Чем больше вылет, тем больше отклонение инструмента при заданной силе резания. Отклонение инструмента очень плохо сказывается на стойкости инструмента, а также затрудняет точную резку, если инструмент изгибается, как крендель, из-за прогиба.
Привыкайте к тому, как инструменты со слишком большим выступом выглядят из ляпов выше. Практическое правило – все, что больше 7-8x диаметра для карбида и 3-4x диаметра с инструментами из быстрорежущей стали – это слишком.Чем ближе вы приблизитесь к этим числам, тем больше у вас проблем с отклонением инструмента.
Думаю, люди думают, что большая длина канавки означает большую универсальность – вы можете использовать фрезу для большего количества работ. Но правда как раз наоборот. Прогиб ограничит ваши возможности использования таких фрез. Вместо этого возьмите более короткие канавки и вставьте их в держатель инструмента как можно глубже. Практическое правило – держите столько выступа, сколько вам нужно для резания, плюс один диаметр инструмента для дополнительного зазора.
Мы можем лучше оптимизировать вылет, так что давайте займемся этим.
Какой у инструмента самый лучший вылет?Какая оптимальная длина вылета инструмента из держателя инструмента? Что бы это ни было? Что бы вы ни сделали, чтобы избежать удара резцедержателя о заготовку? Есть ли другая стратегия для оптимизации вылета?
Вылет инструмента– важная тема, поскольку она определяет множество ограничивающих факторов, связанных с использованием инструмента.Вылет – это расстояние от кончика инструмента до места, где хвостовик инструмента входит в держатель инструмента. Чем больше это расстояние, тем дальше выступает инструмент. Это полезно, когда вам нужен зазор, но увеличение вылета может значительно снизить жесткость инструмента в разрезе.
В состав калькулятораG-Wizard входит калькулятор жесткости, поэтому давайте воспользуемся им, чтобы понять, о чем я говорю. Предположим, у нас есть твердосплавная концевая фреза 1/4 дюйма с вылетом 3/4 дюйма. Если мы сможем втянуть инструмент в оправку только на 1/3 вылета, другими словами, если вылет будет 1/2 дюйма вместо 3/4 дюйма, этот инструмент будет равен 3.375X более жесткий:
Предположим, мы можем уменьшить эти 1/2 дюйма вылета до 0,430 дюйма – это всего на 70 тысячных меньше. Оказывается, этого достаточно, чтобы увеличить жесткость еще на 50%. Даже относительно небольшие изменения вылета имеют большое значение для жесткости! И эта жесткость может радикально повлиять на самые разные важные области:
– Болтовня
– Прогиб инструмента
– Вибрация и обработка поверхности
– Стойкость инструмента
– Допуски.
Я начинаю привлекать ваше внимание?
Возможность оптимизировать вылет инструмента таким образом, чтобы у вас было ровно столько, а не больше, может помочь вам достичь максимальной производительности и стойкости инструмента.
Факторы, ограничивающие вылетЕсть четыре ключевых фактора, ограничивающих вылет:
1. Зазор: инструмент должен выступать достаточно далеко, чтобы он мог достичь дна любого гнезда или другого элемента без соприкосновения державки с заготовкой.Если у вас есть карман глубиной 1/2 дюйма, вы не сможете разрезать этот карман (по крайней мере, не весь его) инструментом, который выступает только на 1/4 дюйма.
2. Доступ к СОЖ. Представьте, что вы используете относительно большой держатель инструмента, скажем, цанговый патрон ER32 и концевую фрезу 1/4 дюйма, как в нашем примере жесткости. Гайка ER32 значительно больше концевой фрезы. А теперь давайте предположим, что мы серьезно уменьшили вылет. Мы вырезаем карман глубиной 1/2 дюйма, и у нас вылет 0,600 дюйма, поэтому между нижней частью держателя инструмента и верхним краем кармана остается только 1/10 дюйма.Если вы визуализируете эту ситуацию, охлаждающей жидкости будет сложно пройти через зазор 1/10 дюйма до фрезы и вниз в прорезь глубиной 1/2 дюйма с любой силой. Накопление чипов будет проблемой.
3. Длина канавок. На самом деле вы не хотите, чтобы резцедержатель давил на канавки, вы хотите, чтобы резцедержатель попадал на хвостовик инструмента. Чрезмерная длина канавки приведет к минимальному вылету. При выборе концевой фрезы используйте самые короткие канавки, которые позволяет работа.
4. Один и тот же инструмент для множества работ.У вас есть инструмент в устройстве смены инструмента или в держателе инструмента. Если вы используете фрезерный станок с ЧПУ, он уже есть в вашем шпинделе. Вы не оптимизировали его для этого конкретного задания, но хотите сэкономить время и просто запустить его для этого задания. Итак, вылет – вот что это такое, и вам нужно двигаться вперед.
Мы мало что можем сделать с зазором вокруг заготовки, но для доступа к СОЖ мы можем попытаться минимизировать диаметр державки, чтобы она меньше блокировалась. Вместо того, чтобы брать самый большой цанговый патрон, который у вас есть, возьмите самый маленький, который может вместить вашу концевую фрезу.Мы также можем попытаться сориентировать сопла охлаждающей жидкости так, чтобы они попадали в отверстие, а не отскакивали от державки.
Имея это понимание, давайте рассмотрим три стратегии оптимизации вылета инструмента.
Стратегия № 1: Минимальный вылет с зазором
С учетом оговорок о доступе к охлаждающей жидкости и длине канавки наиболее очевидной стратегией является минимизация вылета для каждого инструмента и каждой конкретной работы. Для этого нам нужно иметь возможность измерить, насколько далеко ниже верхней части запаса каждый инструмент будет уходить для конкретной работы, и нам понадобится некоторое представление о том, какой дополнительный зазор может потребоваться для очистки зажимов и других деталей приспособлений. а также любые детали, которые могут выступать и мешать.Один простой способ быстро получить представление о том, сколько зазора требуется для каждого инструмента, – это использовать наш редактор G-Wizard Editor. Как часть загрузки и моделирования программы, он создает таблицу инструментов на вкладке Инструменты, которая имеет наименьшую координату Z, используемую для каждого инструмента:
Минимальное значение Z для каждого инструмента указано в столбце «Мин. Z» в таблице инструментов. Это новая функция в GWE v1.15…
.Эта конкретная программа является одним из наших стандартных образцов файлов и представляет собой программу для гравировки тонкой алюминиевой панели электроники.Есть два инструмента: один с минимальной Z -0,060 ″ и один с -0,040 ″. Учитывая, что это работа по гравировке, большого выступа не требуется, поэтому мы можем сократить количество инструментов. Используя G-Wizard таким образом, вы можете точно сказать, сколько вылетов требуется данной программе. Конечно, вам нужно знать, какой Z соответствует верхняя часть материала, и провести математические расчеты, а также добавить припуск для любых приспособлений, зажимов или деталей, которые могут быть достаточно близко, чтобы мешать, но вы можете сэкономить много времени таким образом, а также получение действительно оптимальных вылетов, которые максимизируют жесткость.
Стратегия № 2: устранение выпадов по мере необходимости
Хорошо, у вас есть инструмент в держателе инструмента, вы ввели вылет в G-Wizard, и он выдает предупреждение об отклонении.
Черт!
Но не беспокойтесь. Во-первых, G-Wizard позволяет оптимизировать несколько переменных, чтобы исправить предупреждение об отклонении:
- Глубина реза
- Ширина реза
- Ползунок черепаха-заяц
- Вылет
Ага, возможно, вам вообще не придется прикасаться к инструменту, просто измените один из других параметров.Вы можете найти точное значение, нажав маленькую кнопку спидометра рядом с параметром (стрелки указывают на кнопки спидометра):
G-Wizard рассчитает максимальное значение параметра, при котором не выводится предупреждение об отклонении одним щелчком мыши.
Стратегия № 3: Стандартизированные выписки для облегчения управления Chatter
Есть ли причина не всегда использовать минимальный вылет для каждой работы? Можно ли получить какое-то преимущество?
Это вопрос о том, какие виды работ выполняет ваш магазин и как вы подходите к проблеме болтовни.Если вы собираетесь производить много-много одинаковых деталей, вам нужно будет оптимизировать время цикла, и это будет происходить за счет минимального вылета для конкретной работы. Если, с другой стороны, вы выполняете множество различных частей с небольшими тиражами, время настройки становится вашим ограничивающим фактором, поскольку каждое новое задание требует другой настройки. Вы можете устать выгружать устройство смены инструмента, сбрасывать все выступы инструмента, а затем довольно быстро перезагружать его.
Болтовня также усложняет вопрос с двух точек зрения.Во-первых, если вы используете одни и те же выступы, болтовня – это повторяющееся явление. Другими словами, с одним и тем же типом державки, концевой фрезы и вылета вы будете каждый раз получать вибрацию при одинаковых оборотах шпинделя. Зная это, вы можете наметить несколько оптимальных оборотов в минуту, чтобы получить так называемое стабильное измельчение без дребезга. Чтобы узнать больше обо всем этом, ознакомьтесь с моей статьей о болтовне в Поваренной книге каналов и скорости.
Поскольку изменение вылета также приводит к изменению частоты вибрации, иногда бывает полезно изменить вылет, чтобы достичь более оптимального диапазона оборотов шпинделя при резании.
Это относительно сложные соображения, которые кажутся очень специфичными для конкретной работы, так как же мы можем придумать стратегию, которая поможет магазину оптимизировать свои общие результаты?
Один из ответов – стандартизировать вылет инструмента и выбрать несколько значений для каждого диаметра инструмента. Возьмем нашу концевую фрезу 1/4 дюйма. Возможно, ваш магазин будет использовать выступы 3/4 ″, 1/2 ″ и 3/8 ″ или что-то в этом роде. Дело в том, чтобы задокументировать стандартные вылеты вашего магазина и придерживаться одного из задокументированных номеров.Чтобы настроить задание, вы должны создать отчет, такой как G-Wizard Editor, который показывает минимальные вылеты. Тогда вы найдете стандартный выступ для вашего магазина, который ближе всего к минимальному, но больше его. Это тот, который вы бы использовали, и, надеюсь, уже есть держатели с концевыми фрезами в стандартных выступах, так что вы можете просто взять один, если он еще не загружен.
Теперь предположим, что вы начали болтать. Поскольку вы стандартизировали вылет, концевую фрезу и держатель инструмента, вы можете быть уверены, что на этом станке на этой скорости шпинделя будет дребезжать каждый раз, когда вы будете работать на этой скорости и приводите фрезу в движение с такой силой, чтобы она дребезжала.Итак, вы регулируете частоту вращения шпинделя (старайтесь как больше, так и меньше, вы просто пытаетесь выйти из зоны вибрации и остановить резонанс) до минимума. Надеюсь, у вас даже есть запись, на которую вы можете сослаться, в которой рассказывается, что сработало в прошлом. Если вы используете GW Calculator, вы можете использовать его Базу знаний Cut, чтобы отслеживать эти вещи.
С такой системой вы пройдете период экспериментов, пока не наметите, как минимизировать дребезг для стандартных конфигураций резака, а затем вы сможете очень быстро переходить от работы к работе.